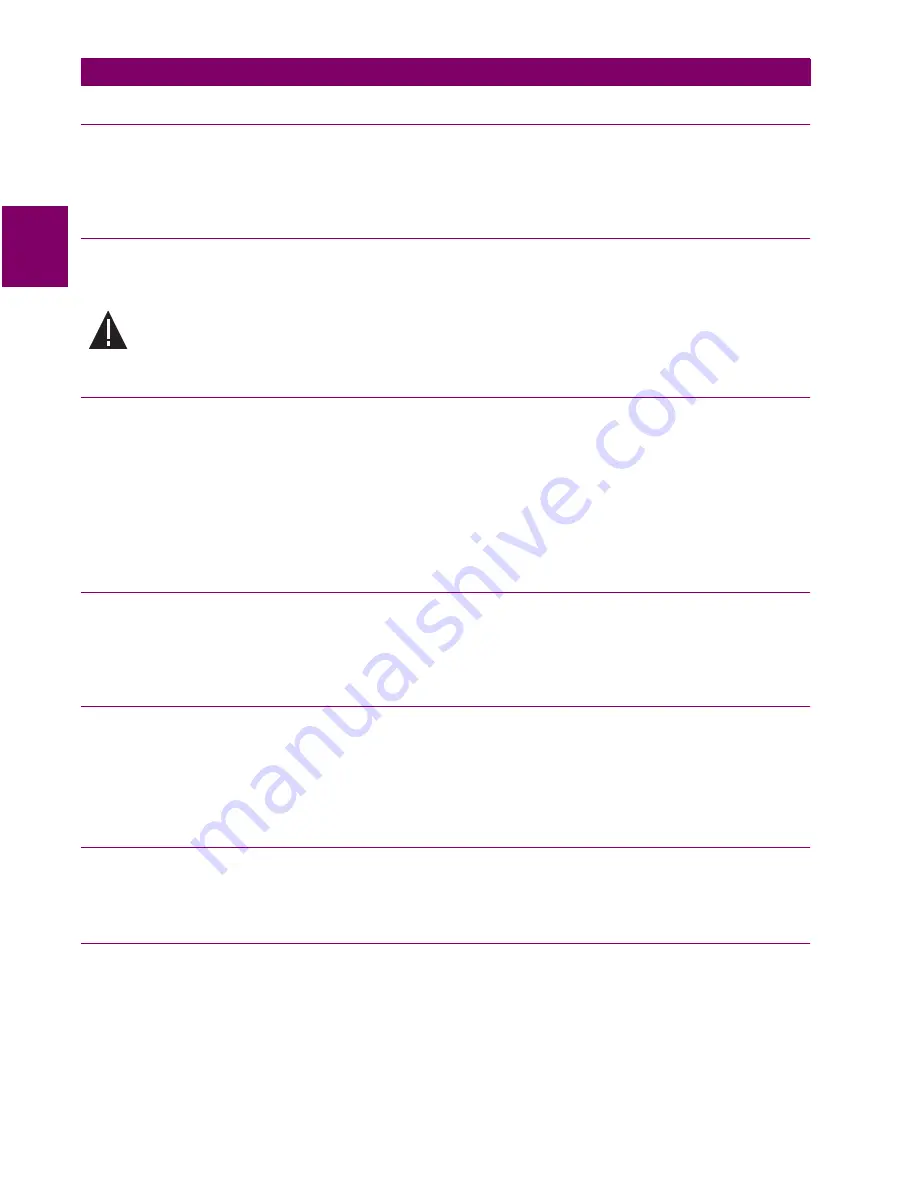
2-
6
SPM Synchronous Motor Protection & Control
GE Power Management
2.3 ELECTRICAL INSTALLATION
2 INSTALLATION
2
2.3.2 GROUNDING
The SPM relay must be solidly grounded to a suitable system ground. Extensive filtering and transient protec-
tion has been built into the SPM to ensure proper and reliable operation in harsh industrial environments.
Proper grounding of the chassis ground terminal is critical to en-sure safety and filtering.
2.3.3 FIELD AND EXCITER VOLTAGE INPUTS
The field voltage inputs (V
F
+ and V
F
–) and exciter voltage inputs (V
E
+ and V
E
–) are connected to the relay
via the supplied voltage divider network (VDN).
DO NOT ATTEMPT TO START THE MOTOR WITHOUT THE EXTERNAL RESISTOR ASSEMBLY
WIRED. SEVERE DAMAGE TO THE SPM MAY RESULT IF THE EXTERNAL RESISTOR ASSEM-
BLY IS NOT PROPERLY CONNECTED.
2.3.4 RELAY OUTPUTS
The following is a description of the relay outputs.
1.
TRIP: Trip Relay. This relay is normally energized and drops out on loss of power or when the module
senses an abnormal condition.
2.
FAR: Field Application Relay. This relay picks up at the proper time to apply DC to the motor field.
3.
FCX: Loading Relay. This relay picks up when the motor is fully synchronized and ready to be loaded. It is
controlled by the "FCX Delay" programmable setpoint.
2.3.5 CURRENT TRANSFORMER INPUT
The SPM is designed to work from a five ampere (5 A) current transformer (CT) secondary. The current trans-
former must be connected in the proper motor phase. See Figure 2–3: TYPICAL WIRING DIAGRAM on page
2–4 to determine proper phase. For brushless applications, the SPM requires inputs from two motor phases.
2.3.6 POWER FACTOR OUTPUT
This output is a 0 to 10 V DC signal that corresponds linearly to phase shift, and sinusoidal to motor power fac-
tor. 0 V is zero lagging power factor, 5 V is unity power factor, and 10 V is zero leading power factor.
Calibration: 1 volt change corresponds to an 18° phase shift (not available with power factor regulation). Do not
connect less than 1000
Ω
to this output.
2.3.7 DC FIELD CURRENT INPUT
DC field input must be sensed from a separately purchased DCCT (Direct Current, Current Transformer) and
CM (Calibration Module).
2.3.8 EXCITER VOLTAGE OUTPUT MONITOR
The output of the field exciter must be connected to the SPM through a separate resistor when exciter voltage
failure protection and/or exciter voltage display is required.
CAUTION
Summary of Contents for SPM Series
Page 2: ......
Page 4: ......
Page 10: ...vi SPM Synchronous Motor Protection Control GE Power Management TABLE OF CONTENTS...
Page 74: ...6 4 SPM Synchronous Motor Protection Control GE Power Management 6 2 STATUS 6 ACTUAL VALUES 6...
Page 120: ...C 2 SPM Synchronous Motor Protection Control GE Power Management C 1 WARRANTY APPENDIXC C...
Page 124: ...iv SPM Synchronous Motor Protection Control GE Power Management INDEX...
Page 125: ...GE Power Management SPM Synchronous Motor Protection Control NOTES...