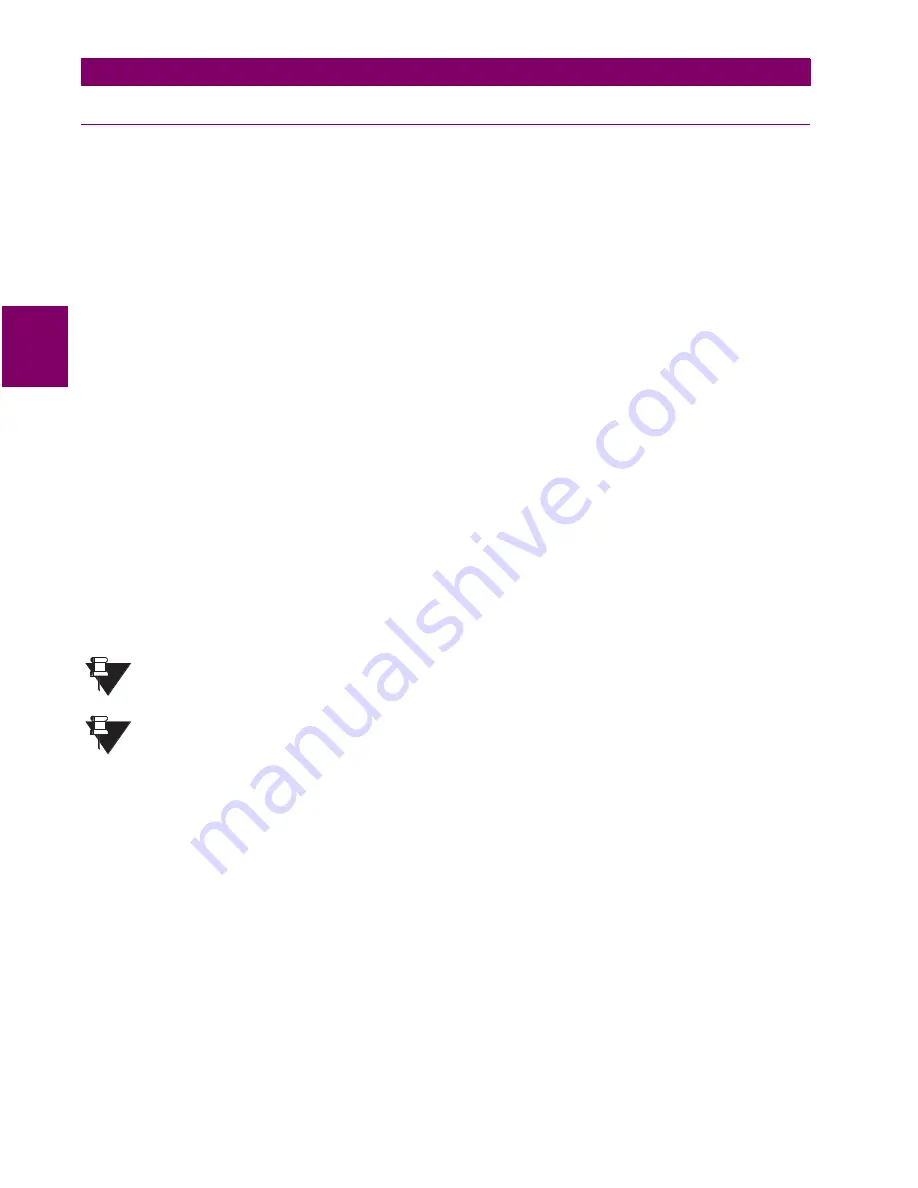
3-
8
SPM Synchronous Motor Protection & Control
GE Power Management
3.2 COLLECTOR-RING MOTORS
3 SYNCHRONOUS MOTOR APPLICATIONS
3
3.2.4 REDUCED VOLTAGE STARTING
Many synchronous motor starting applications involve either reduced voltage (starting reactor or autotrans-
former) or part-winding starting methods. When these methods are used, the available torque for acceleration
is reduced from the torque that would result from a full-voltage start. Also, the allowable stall time of a motor is
extended during a reduced-voltage start due to the reduced heating-rate resulting from lower inrush currents.
The SPM has the ability to take advantage of the motor's extended stall time so that the motor and load can
accelerate to synchronous speed in a time period longer than would be allowed with a full voltage start. The
acceleration torque is reduced as the square of the ratio of reduced voltage to full voltage, and the motor-heat-
ing rate is proportional to the square of the starting current. Since the motor inrush current is reduced propor-
tionally with the voltage reduction (due to the constant impedance of the synchronous motor at stall) the
following allowable stall time factor applies:
where:
I
PLR
= programmed full voltage locked rotor current.
I
MLR
= measured inrush current.
This ratio can be used as a factor for increasing the stall time above the full voltage allowable stall time for any
given speed. See Figure 19.
The SPM calculates the ratio, squares it, and factors this value into the stall time algorithm approximately one-
tenth of a second after motor starts. When the final step contactor closes and applies full voltage to the motor
windings, a N.O. interlock from this contactor is wired to the SPM to signal that the motor is now at full voltage.
The correction factor for reduced voltage starts then immediately becomes unity.
If, for any reason, it is not desirable to have this ratio correction factored in, a jumper may be placed across
inputs NX1 and NX2. Conversely, if the motor is started from a weak system, and significant voltage dips are
expected during starting, the factory jumper from NX1 to NX2 may be removed. The SPM will automatically
extend the stall and accelerating time per the reduced voltage factor.
To find the protective characteristic used, plot the programmed value for 50% run time and
draw in the complete curve through the plotted point using the above curves as a guide.
The curves shown in the following diagram demonstrate how the trip characteristic of the
amortisseur winding protection is adjusted for reduced voltage starts. For this example, curve
1 is taken from one of the family of curves in Figure 3–8: AMORTISSEUR WINDING PROTEC-
TION on page 3–7.
I
PLR
I
MLR
------------
2
NOTE
NOTE
Summary of Contents for SPM Series
Page 2: ......
Page 4: ......
Page 10: ...vi SPM Synchronous Motor Protection Control GE Power Management TABLE OF CONTENTS...
Page 74: ...6 4 SPM Synchronous Motor Protection Control GE Power Management 6 2 STATUS 6 ACTUAL VALUES 6...
Page 120: ...C 2 SPM Synchronous Motor Protection Control GE Power Management C 1 WARRANTY APPENDIXC C...
Page 124: ...iv SPM Synchronous Motor Protection Control GE Power Management INDEX...
Page 125: ...GE Power Management SPM Synchronous Motor Protection Control NOTES...