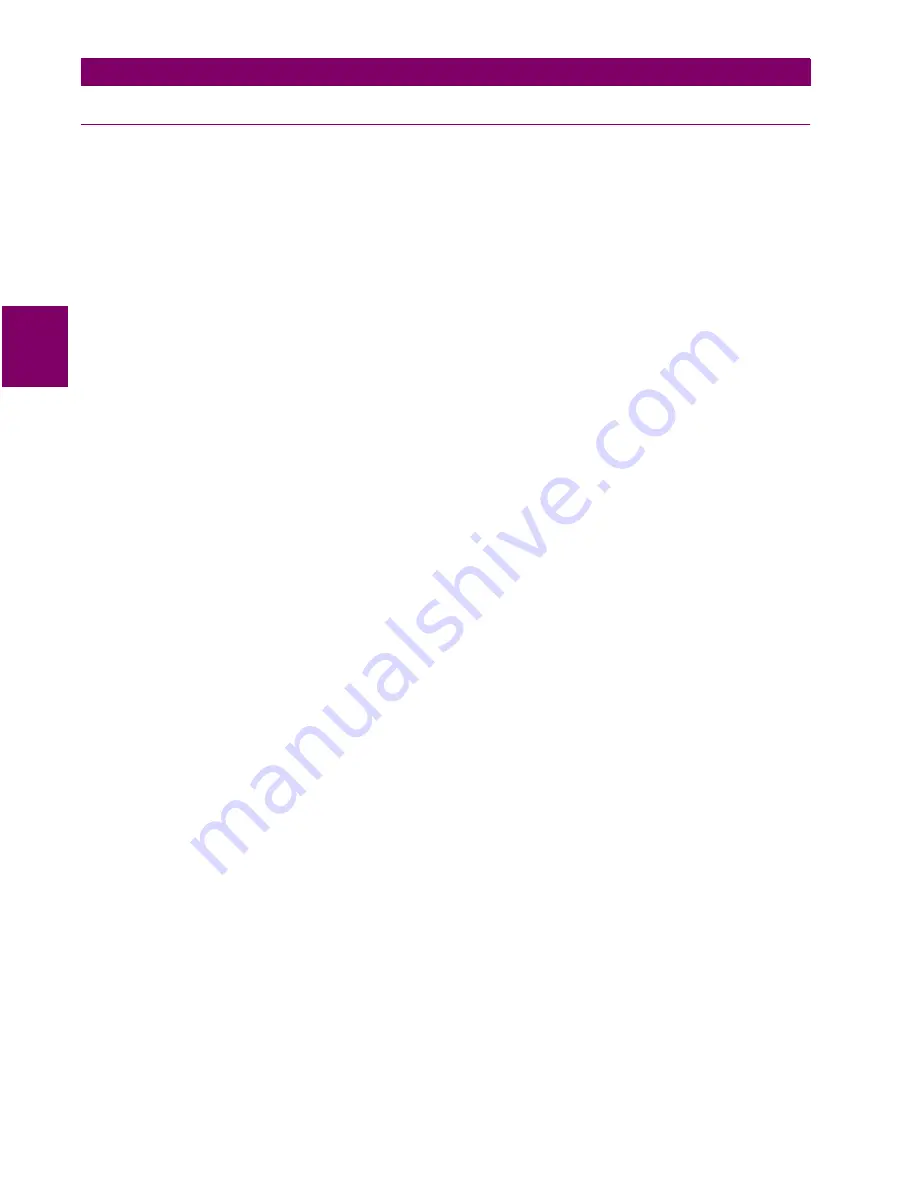
3-
10
SPM Synchronous Motor Protection & Control
GE Power Management
3.2 COLLECTOR-RING MOTORS
3 SYNCHRONOUS MOTOR APPLICATIONS
3
3.2.5 POWER FACTOR (PULL-OUT) PROTECTION
Synchronous motors are designed to run at constant speed and drive shaft loads from torque derived from the
magnetic poles on their rotors magnetically linking opposite stator poles. Whenever the rotor turns at a speed
less than that of stator rotating field, the motor is said to be slipping poles. Slip can occur with the field poles
magnetized while running in synchronism from the following four major causes.
1.
A gradual increase in load beyond the pull-out capabilities of the motor.
2.
A slow decrease in field current.
3.
A sudden large impact load.
4.
A system fault or voltage dip lasting long enough to cause pull-out.
Loss of synchronism with field applied will create intense pulsations in torque at the motor shaft each time a
stator pole passes a rotor pole. Corresponding pulsations occur in line current. Both types of pulsations can be
damaging. Torque pulsations can break a shaft, coupling, or other mechanical elements, and current pulsa-
tions can interfere with smooth power system operation. Slipping poles with field applied is always unaccept-
able for a synchronous motor, therefore some means must be provided to prevent this condition from
occurring.
One of the most reliable indicators of synchronous and asynchronous (out-of-step) operation is the motor
power factor. Power factor is related to the phase angle between voltage and current. Synchronous motors sel-
dom, if ever, operate continuously at lagging power factor. Synchronous motors run at either unity or some
value of leading power factor. Lagging power factor appears when the motor load angle increases beyond
rated, becoming almost fully lagging (90°) as the motor slips out-of-step. Therefore, lagging power factor can
be utilized to initiate action to prevent slipping.
Torque and power pulsations during slip can be reduced by removing field current to the rotor poles. The motor
will then run essentially as an induction motor on its amortisseur winding. Slip with the field current removed is
tolerable to the load and power system but intolerable for any length of time to the motor amortisseur winding
itself, since the winding is designed with limited thermal capability and for short-time operation. Motor Power
Factor during induction motor operation (that is with field removed) is always lagging. However, the degree to
which the current lags the voltage is less than at pull-out when field poles are excited. Lagging power factor
can again be utilized as an indicator of "slip" during induction motor operation.
For synchronous motors, power-factor monitoring can be employed to guard against pull-out or loss of field
conditions.
Summary of Contents for SPM Series
Page 2: ......
Page 4: ......
Page 10: ...vi SPM Synchronous Motor Protection Control GE Power Management TABLE OF CONTENTS...
Page 74: ...6 4 SPM Synchronous Motor Protection Control GE Power Management 6 2 STATUS 6 ACTUAL VALUES 6...
Page 120: ...C 2 SPM Synchronous Motor Protection Control GE Power Management C 1 WARRANTY APPENDIXC C...
Page 124: ...iv SPM Synchronous Motor Protection Control GE Power Management INDEX...
Page 125: ...GE Power Management SPM Synchronous Motor Protection Control NOTES...