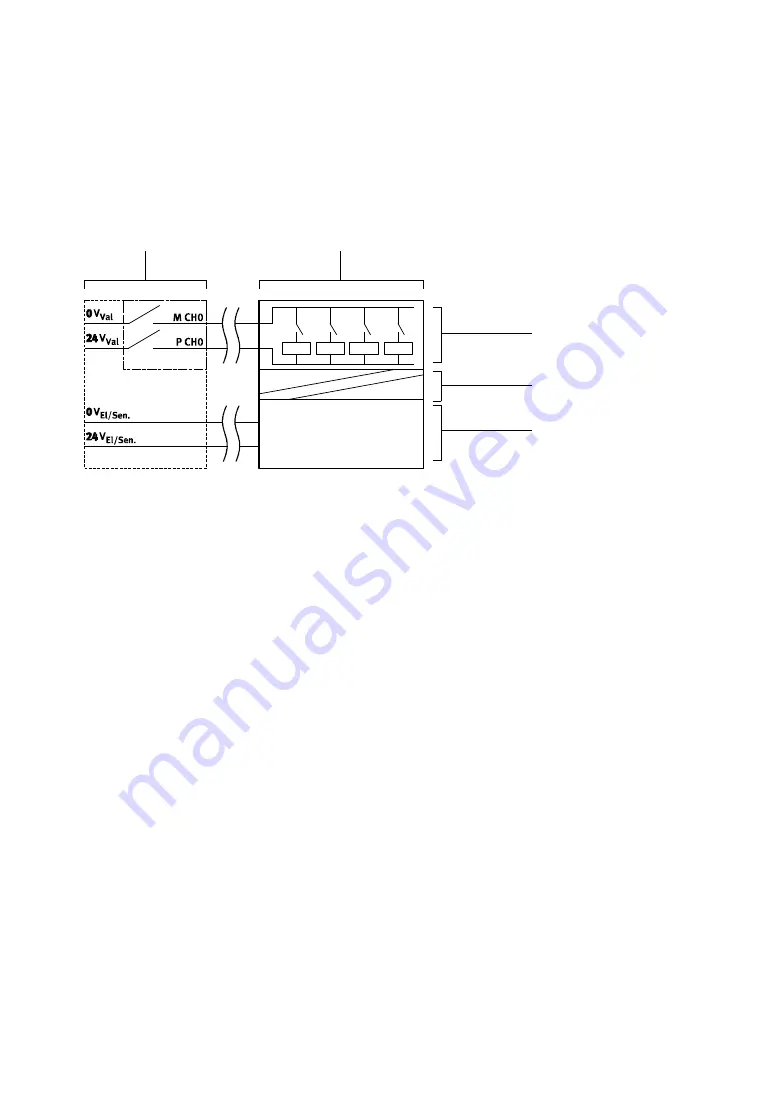
1. System overview CPX-FVDA-P2
1-24
Festo P.BE-CPX-FVDA-P2-EN en 1209NH English
Case 1:
Safe switch off of the load voltage supply for the internal
valves of the valve terminal with galvanic isolation via CH0.
1
2
3
4
5
1
Output module CPX-FVDA-P2 with
interlinking block CPX-M-GE-EV-FVO
2
Valve terminal MPA or VTSA
3
Solenoid coils of the internal
pneumatics
4
Galvanic isolation
5
Electronics side
Fig. 1/5:
Switch-off of the load voltage supply of CPX-internal solenoid coils
Summary of Contents for 1971599
Page 2: ......
Page 75: ...Installation 2 1 Festo P BE CPX FVDA P2 EN en 1209NH English Chapter 2 Installation...
Page 91: ...Commissioning 3 1 Festo P BE CPX FVDA P2 EN en 1209NH English Chapter 3 Commissioning...
Page 112: ...3 Commissioning 3 22 Festo P BE CPX FVDA P2 EN en 1209NH English...
Page 113: ...Operation 4 1 Festo P BE CPX FVDA P2 EN en 1209NH English Chapter 4 Operation...
Page 143: ...Index B 1 Festo P BE CPX FVDA P2 EN en 1209NH English Appendix B Index...
Page 144: ...B Index B 2 Festo P BE CPX FVDA P2 EN en 1209NH English Table of contents B Index B 1...
Page 150: ...B Index B 8 Festo P BE CPX FVDA P2 EN en 1209NH English W Wire break 3 12 5 4...