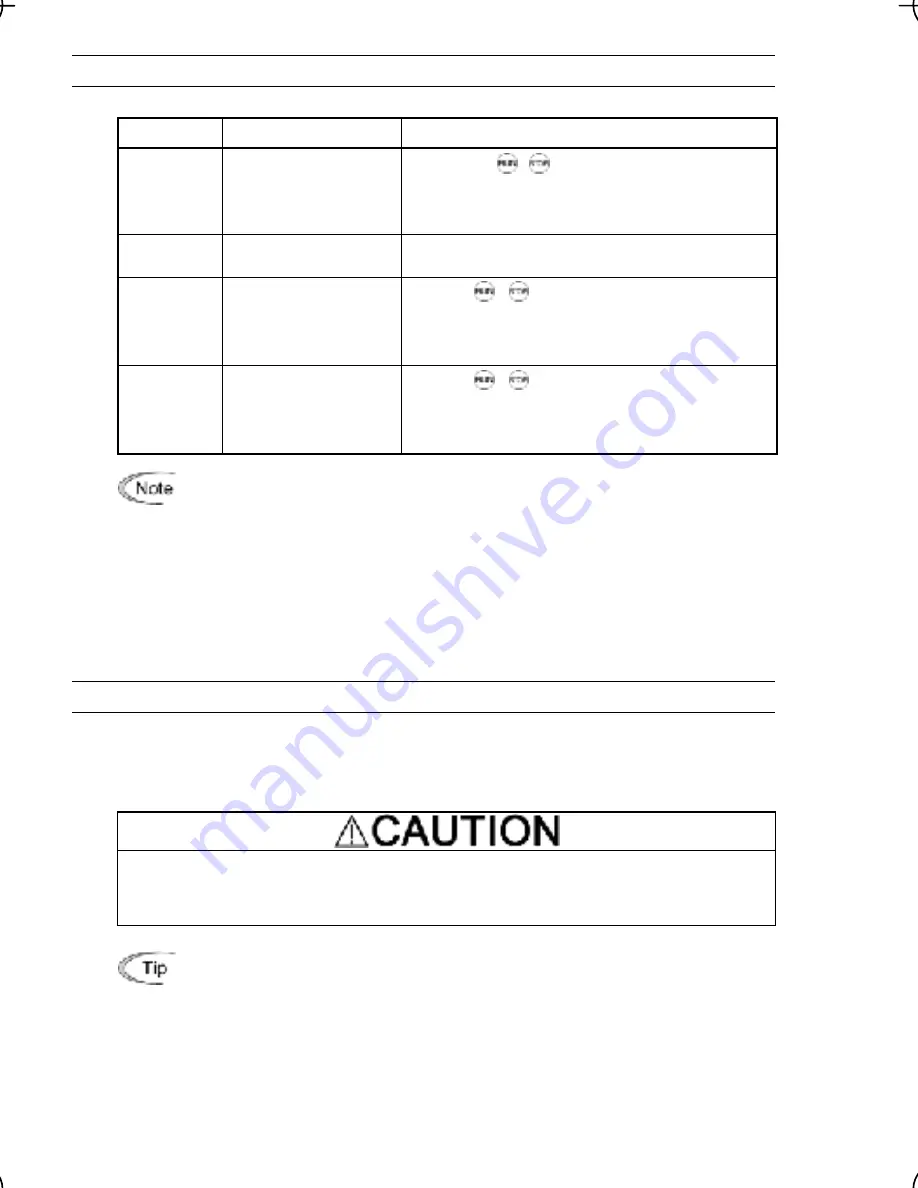
5-15
F02
eration Method
Op
F02 sel
e source that specifies a run command for running the motor.
Data f
2
ects th
or F0
Run Command Source
Description
Keypad
(Rotation direction
specified by terminal
command)
Enables the
/
keys to run and stop the motor.
The rotation direction of the motor is specified by
terminal command
FWD
or
REV
.
0
1
motor.
External
signal Enables terminal command
FWD
or
REV
to run the
2
Keypad
(Forward rotation)
Enables
/
keys to run and stop the motor.
Note that this run command enables only the forward
rotation.
There is no need to specify the rotation direction.
/
Keypad
Enables
(Reverse rotation)
keys to run and stop the motor.
Note that this run command enables only the reverse
rotation.
There is no need t
3
o specify the rotation direction.
• When
reverse"
RE
function code F02 = 0 or 1, the "Run forward"
FWD
and "Run
V
term
[REV],
resp
• When
the
FWD
or
REV
is ON, the F02 data cannot be changed.
inal commands must be assigned to terminals [FWD] and
ectively.
• When assigning the
FWD
or
REV
to terminal [FWD] or [REV] with F02 being set
to "1," be sure to turn the target terminal OFF beforehand; otherwise, the motor
may unintentionally rotate.
• In addition to the run command sources described above, higher priority
command sources including communications link are provided.
F03
Maximum Frequency 1
F03 speci
frequency
a dangero
um frequency setting matches the equipment
rating.
fies the maximum frequency to limit a reference frequency. Specifying the maximum
exceeding the rating of the equipment driven by the inverter may cause damage or
us situation. Make sure that the maxim
The inverter can easily accept high-speed operation. When changing the speed setting, carefully
check the specifications of motors or equipment beforehand
Otherwise injuries could occur.
Modifying F03 data to allow a higher reference frequency requires also changing
F15 data specifying a frequency limiter (high).
Summary of Contents for FRENIC-Multi series
Page 194: ...MEMO MEMO...