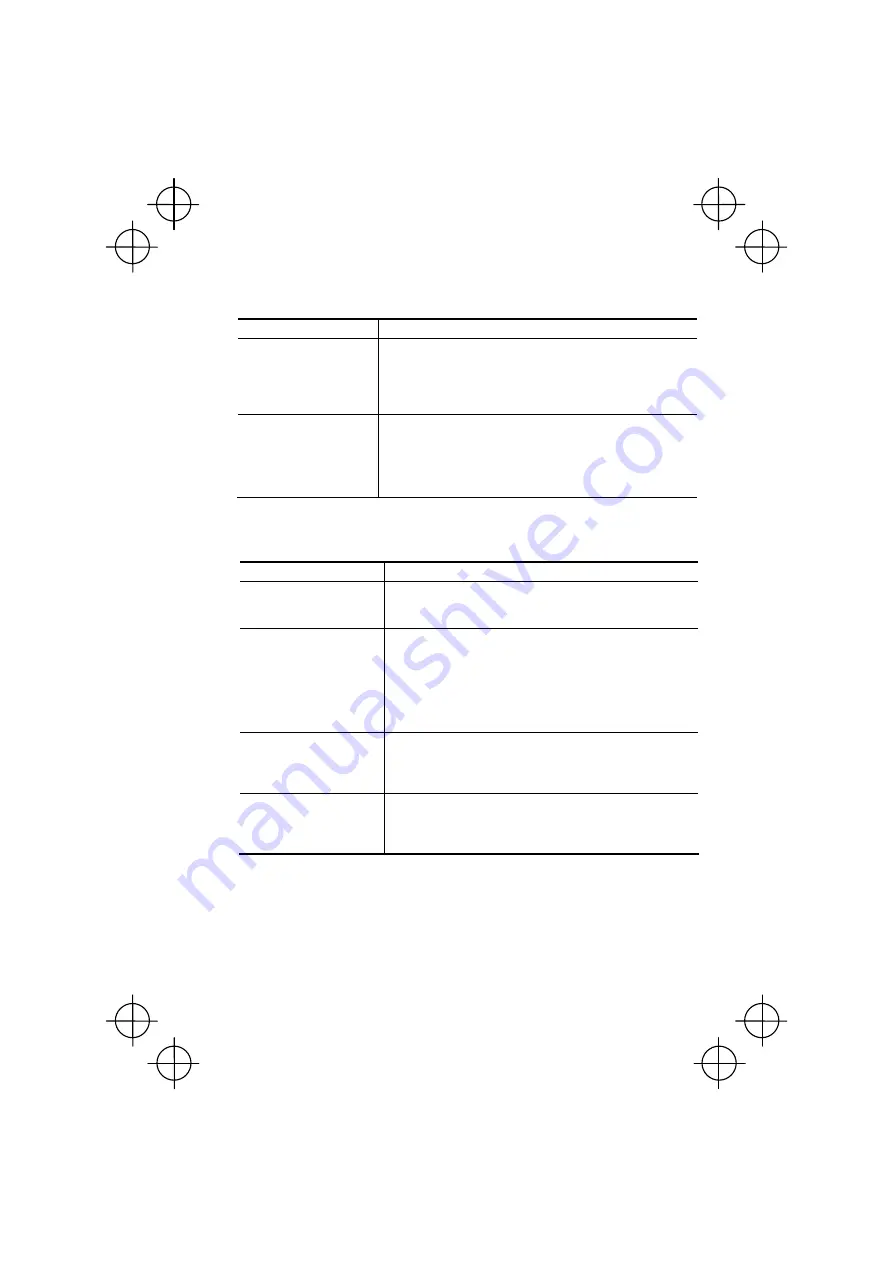
6-23
[ 20 ]
cof
PID feedback wire break
Problem
The PID feedback wire is broken.
Possible Causes
What to Check and Suggested Measures
(1) The PID feedback
signal wire is broken.
Check whether the PID feedback signal wires are connected
correctly.
Î
Check whether the PID feedback signal wires are connected
correctly. Or, tighten up the related terminal screws.
Î
Check whether any contact part bites the wire sheath.
(2) PID feedback related
circuit affected by
strong electrical noise.
Check if appropriate noise control measures have been
implemented (e.g., correct grounding and routing of signal wires,
communication cables, and main circuit wires).
Î
Improve the noise control measures.
Î
Separate the signal wires from main power wires as far as
possible.
[ 21 ]
erd
Step-out detection (for drive of permanent magnet synchronous motors)
Problem
The step-out of the PMSM was detected.
Possible Causes
What to Check and Suggested Measures
(1) Mismatch with the
characteristics of the
motor.
Check whether the settings of F04, F05, P02, P03, P60, P61, P62,
P63 agree with the motor parameters.
Î
Set the motor parameters to those function codes.
(2) Starting torque was
insufficient.
Check the settings of the acceleration time (F07, E10) and the
reference current at starting (P74).
Î
Change the acceleration time to match the load.
Î
Increase the reference current value at starting.
Î
Set the holding time of the starting frequency 1 (F24).
Î
Set the S-curve (H07 = 1 or 2).
Î
Increase the control switching level (P89).
(3) Load is light.
Check the setting of the reference current at starting (P74).
Î
Decrease the reference current value at starting.
Set it to 80% or lower when running a motor alone in a test run
etc.
(4) Control system not
stabilized.
Check the settings of the armature resistance of PMSM (P60) and
the V/f damping control compensation gain (P91, P92).
Î
Adjust the armature resistance of the motor.
Î
Adjust the settings of the compensation gain (P91, P92).