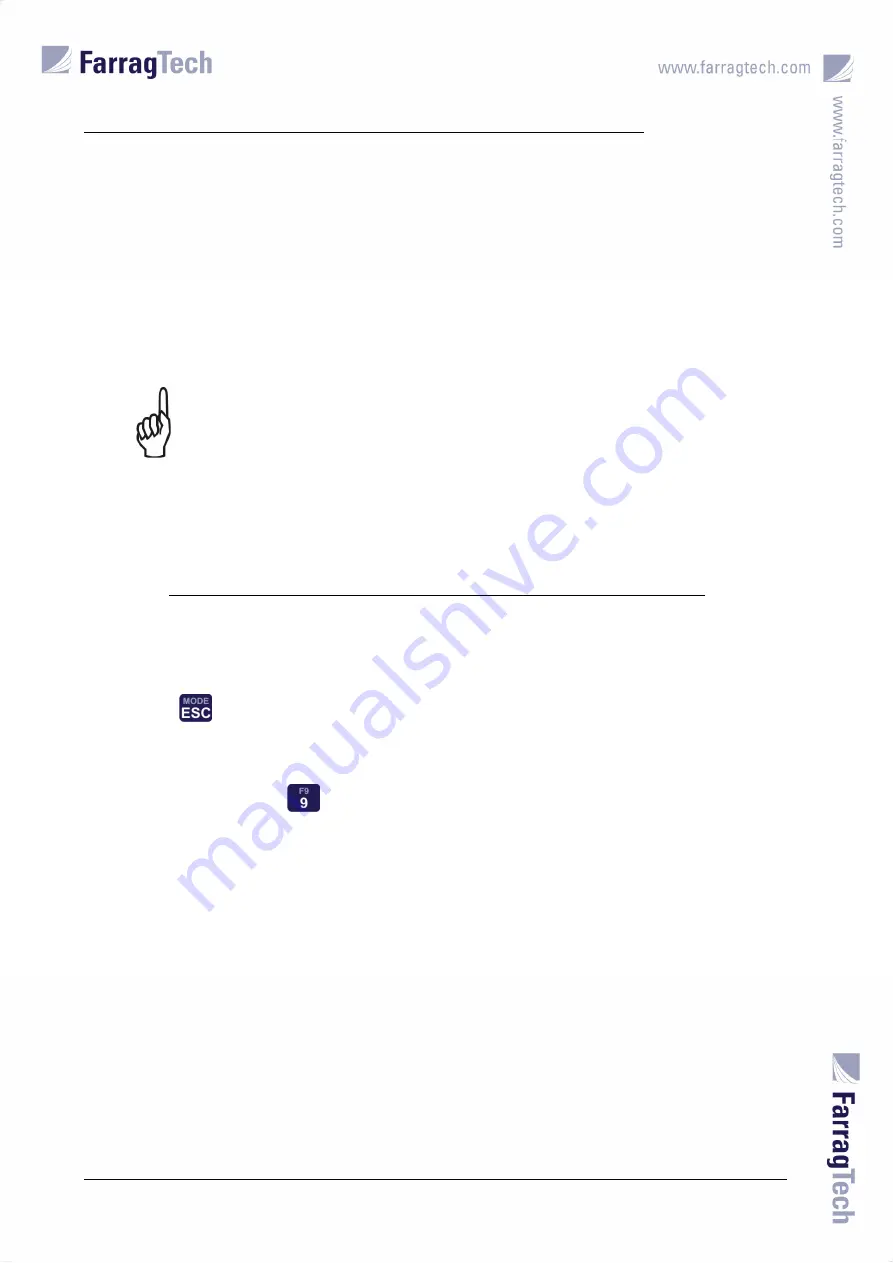
EXTENDED MODE
CARD G / FIT
70
V 6.15 E / April 2010
The other parameters in this screen allows the operator to select the process data which are to
be included in the data recording.
The appropriate data will be transferred if ON is chosen.
The appropriate data will not be transferred if OFF is chosen.
Unintended power failures on the CARD G FIT unit may cause corrupted data
on the USB-stick. It is strongly recommended to backup these data
periodically.
The data on the USB-stick can be accessed through an Ethernet connection to
the FIT-controller. The IP addresses needs to be adjusted according to the
local network requirements (see chapter 17.10.2 on page 71). The process data
can then be accessed on drive c/ on the FIT-controller using the File Transfer
Protocol (FTP).
The key
is to be used to return from this screen back to the screen C
ONVEYING
M
ODE
.
The key
is to be pressed to return to the M
AIN
S
CREEN
.
Summary of Contents for CARD G
Page 2: ......
Page 11: ...HOW IT WORKS CARD G FIT 9 V 6 15 E April 2010 6 HOW IT WORKS ...
Page 26: ...MENU STRUCTURE CARD G FIT 24 V 6 15 E April 2010 12 MENU STRUCTURE ...
Page 27: ...MENU STRUCTURE CARD G FIT 25 V 6 15 E April 2010 12 1 EASY MODE ...
Page 28: ...MENU STRUCTURE CARD G FIT 26 V 6 15 E April 2010 ...
Page 29: ...MENU STRUCTURE CARD G FIT 27 V 6 15 E April 2010 12 2 EXTENDED MODE ...
Page 30: ...MENU STRUCTURE CARD G FIT 28 V 6 15 E April 2010 ...
Page 31: ...MENU STRUCTURE CARD G FIT 29 V 6 15 E April 2010 ...
Page 32: ...MENU STRUCTURE CARD G FIT 30 V 6 15 E April 2010 12 3 SYSTEM PARAMETERS ...
Page 33: ...MENU STRUCTURE CARD G FIT 31 V 6 15 E April 2010 ...
Page 92: ......
Page 93: ...ANNEX ...
Page 94: ......
Page 95: ......
Page 96: ......
Page 97: ......
Page 98: ......
Page 99: ......
Page 100: ......
Page 101: ......