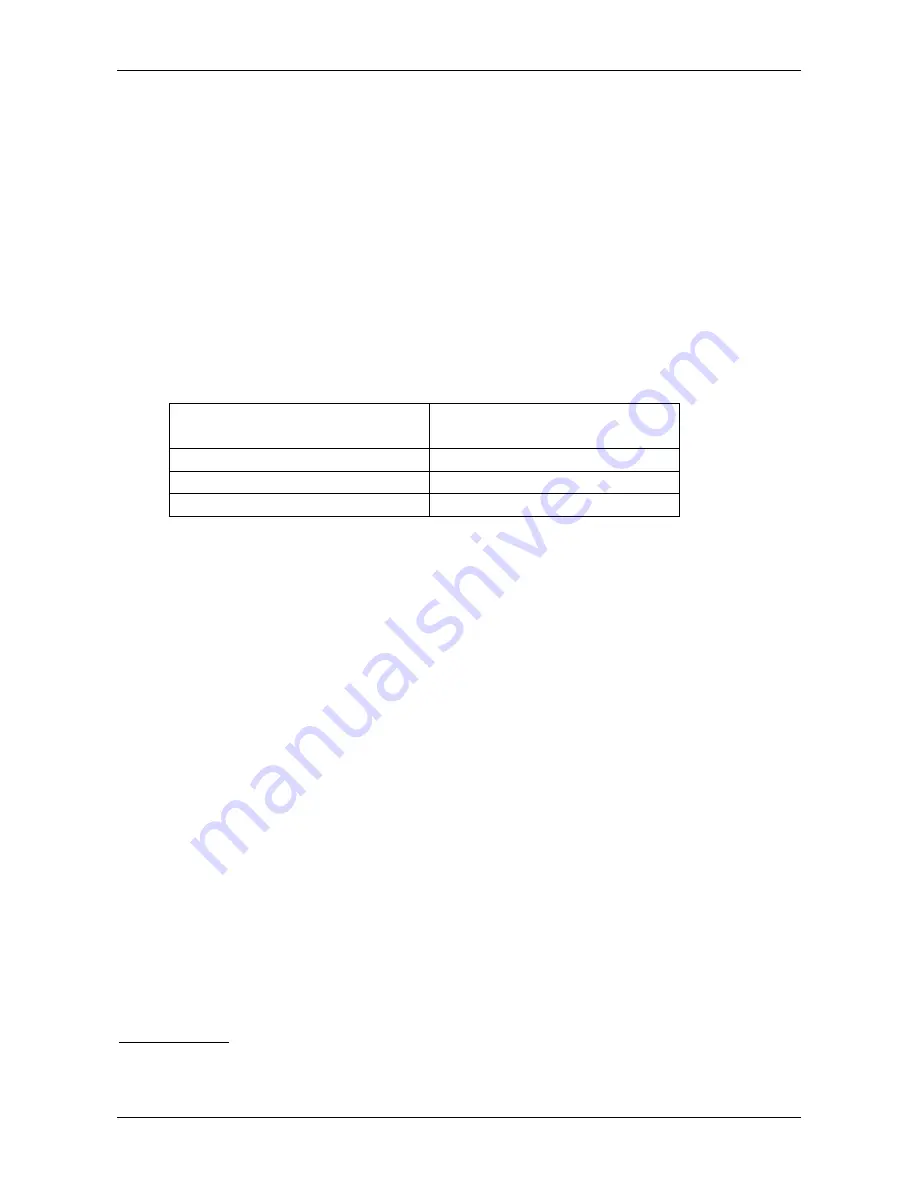
© ElektroPhysik
MiniTest 725, MiniTest 735, MiniTest 745
28 / 85
geometry and substrate material as the later object to be measured (please refer to section
6.2.2.3 Multi-point calibration).
The block statistics defines a number of 3 readings per block.
To compensate for roughness, a correction value according to the table below must be
used. As an alternative, a specific correction value can be determined and set accordingly.
If the roughness value is not known and no uncoated sample is available, a correction value
“25 microns” should be used.
-
A suitable number of readings should be taken according to the size of area to be
measured.
The block statistics defines a number of 3 readings per block.
Roughness profile according to
ISO 8503-1
Correction value
(roughness) microns
fine
10
medium
25
coarse
40
Case 2: The sample is not coated completely (the substrate can be accessed)
-
A calibration according to section 6.3.4 \ Method C or according to the predefined
calibration method “Rough” is to be carried out. During the creation of a batch select
“Manual” our “Rough”. Set the block statistics to 3 reading per block.
6.3 Blasted and rough surfaces
6.3.1 General remarks
To remove rust in order to ensure a good adhesion of the paint, surfaces are commonly blasted in
pre-treatment. As a result, the base material gets rough. Roughness influences the measuring
results, i.e. readings will be higher than the actual thickness.
The following section describes some steps how to remove the influence of roughness in coating
thickness measurement.
For calibration and for determining the average, it is generally recommended to take at least a set
of 10 readings.
If you proceed on thickness measurement according to the steps below, the average thickness
over the peaks will be displayed. Note that the statistics program is of great benefit in this
procedure.