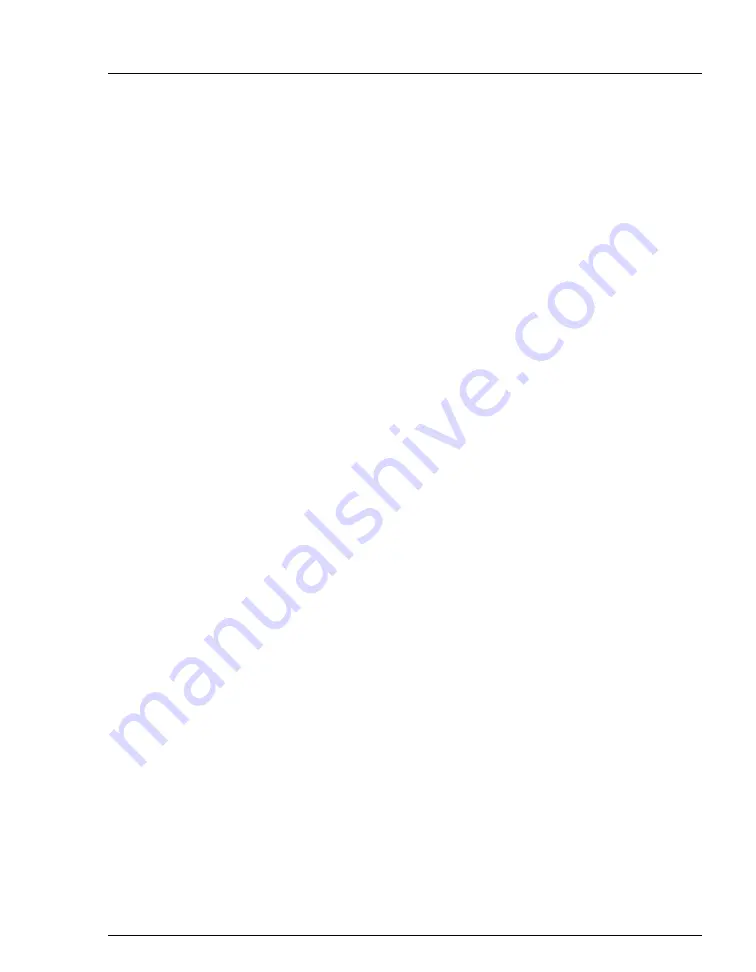
3 • Operation and Maintenance
Doc. 031644-02 9/03
3-29
3.6
Routine Maintenance
The following maintenance procedures may be performed by the user. Other
maintenance procedures must be performed by trained Dionex Service personnel.
•
Before shutting down the detector for more than 24 hours, flush the system
with deionized water or methanol for at least 15 minutes at 1.0 mL/min (or
maintain a continuous flow at 0.2 mL/min). This rinses corrosive acids, salts,
or bases from the flow paths.
•
Periodically check the drain tube connected to the leak tray in the bottom of
the optical bench; verify that the tubing is unclogged and remains routed
below the leak tray.
•
Periodically check the flow cell tubing connections for leaks or restrictions.
Replace tubing and fittings as necessary.
•
Periodically check all tubing and fittings, and replace as necessary (see
Section 5.1). Tubing and fitting components may eventually become loose
and leak, or pinched off and plugged. Look for these symptoms:
Decreasing pressure; this may indicate a leak.
A sudden increase in backpressure; this may indicate plugged tubing. (A
slow increase in backpressure is normal as the separator column ages.) To
troubleshoot, bypass the column and then start the pump; the
backpressure should decrease substantially.
Without the column, backpressure is usually less than 0.34 MPa (50 psi),
depending on the flow rate and tubing ID. However, if the backpressure
remains high, remove the fittings and tubing from part of the flow path,
section by section; start at the waste line and work back “upstream” until
the section causing the substantial backpressure is identified. Replace
tubing and fittings as necessary.
•
Periodically repassivate stainless steel systems. This is especially important
when operating with extremes of pH (which shortens the life of the
passivation finish) or after a major disassembly. For instructions, see
Passivation of Stainless Steel Systems and Components
(Document No.
031152).