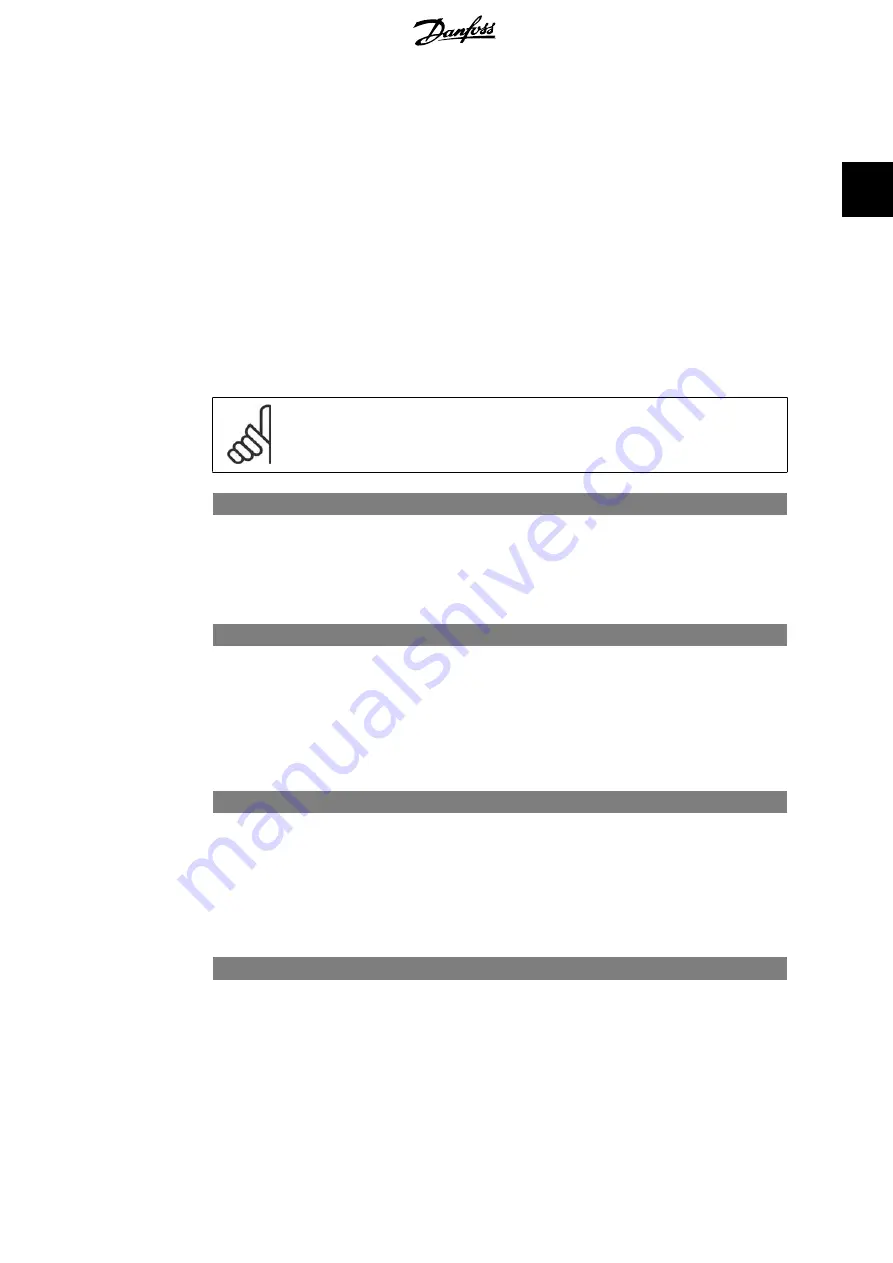
1.
Close the main valve to stop flow
2.
Run with motor until the system has reached normal operating temperature
3.
Press Hand On button on the Local Control Panel and adjust speed for approx. 85% of
rated speed. Note the exact speed
4.
Read power consumption either by looking for actual power in the data line in the Local
Control Panel or call par. 16-10 or 16-11,
Power
, in Main Menu. Note the power read out
5.
Change speed to approx. 50% of rated speed. Note the exact speed
6.
Read power consumption either by looking for actual power in the data line in the Local
Control Panel or call par. 16-10 or 16-11,
Power
, in Main Menu. Note the power read
7.
Program the speeds used in par. 22-32/22-33 and par. 22-36/37
8.
Program the associated power values in par. 22-34/35 and par. 22-38/22-39
9.
Switch back by means of
Auto On
or
Off
NB!
Set par. 1-03,
Torque Characteristics
, before tuning takes place.
22-30 No-Flow Power
Range:
Function:
[Depends on the pow-
er size detection of
No-Flow]
Read out of calculated No Flow power at actual speed. If power
drops to the display value the frequency converter will consider
the condition as a No Flow situation.
22-31 Power Correction Factor
Range:
Function:
100%
[1-400%]
Make corrections to the calculated power at No Flow Detection
(see par. 22-30).
If No Flow is detected the setting should be increased to above
100%. If however No Flow is not detected the setting should be
decreased.
22-32 Low Speed [RPM]
Range:
Function:
0 RPM [0.0 - par. 4.13 (Motor
High Speed Limit)]
To be used if par. 0-02,
Motor Speed Unit
, has been set for RPM
(parameter not visible if Hz selected).
Set used speed for the 50% level.
This function is used for storing values needed to tune No Flow
Detection.
22-33 Low Speed [Hz]
Range:
Function:
0 Hz
*
[0.0 - par. 4-14 (Mo-
tor High Speed Limit)]
To be used if par. 0-02,
Motor Speed Unit
, has been set for Hz
(parameter not visible if RPM selected).
Set used speed for the 50% level.
The function is used for storing values needed to tune No Flow
Detection.
VLT
®
AQUA Drive Programming Guide
2. Parameter Description
MG.20.O2.02 - VLT
®
is a registered Danfoss trademark
199
2