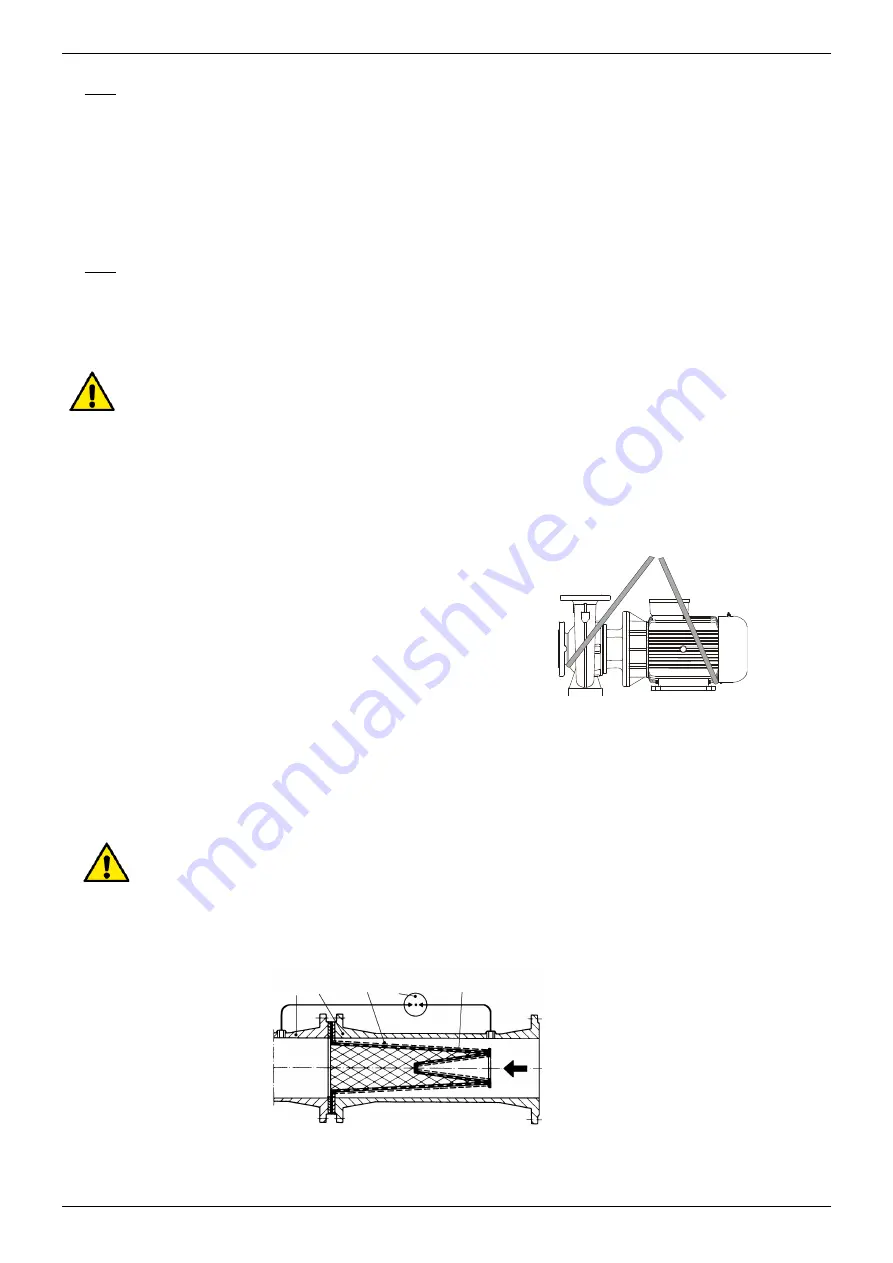
ENGLISH
17
4.
TECHNICAL DATA AND RANGE OF USE
Pump
−
Liquid temperature range:
from -10°C to +140°C standard pumps
from -25°C to +140°C oversize pumps
−
Rotation speed:
970-1450-2900 1/min
−
Flow rate:
from 1 m³/h to 1100 m³/h depending on the model
−
Head up – Hmax (m):
pag. 110
−
Maximum environment temperature:
+40°C
−
Storage temperature:
-10°C +40°C
−
Relative humidity of the air:
max 95%
−
Maximum working pressure (including any pressure at intake):
16 Bar - 1600 kPa (for DN 200- DN 250 max 10 Bar-1000 kPa)
−
Weight:
See plate on package
Motor
−
Supply voltage:
see electrical data plate
−
Degree of motor protection :
IP55
−
Thermal class :
F
−
Absorbed power :
see electric data plate
−
Motor construction :
in conformity with Standards CEI 2 - 3
−
Class AM line fuses: see table 4.1. page 104
If a fuse trips which protects a three-phase motor, it is recommended to change the other two fuses as well, not only
the one that is burnt-out.
5.
MANAGEMENT
5.1. Storage
All the pumps/electropumps must be stored indoors, in a dry, vibration-free and dust-free environment, possibly with constant air humidity.
They are supplied in their original packaging and must remain there until the time of installation, with the intake and delivery mouths closed
with the special adhesive disc supplied. In the case of long storage, or if the pump is stored after a certain period of operation, only the parts
made of low-percentage alloy materials, such as cast iron GG-25, GGG-40 which have been wet with the pumped fluid, should be kept in the
special preserving mediums available on the market.
5.2. Transport
Avoid subjecting the products to needless jolts or collisions.
To lift and transport the unit, use lifting equipment and the pallet supplied standard (if
applicable).
Use suitable hemp or synthetic ropes only if the part can be easily slung, as indicated
in fig.5.2. If an eyebolt is provided on the motor, it must not be used for lifting the
whole assembly.
(fig. 5.2.)
5.3. Dimensions and weights
The adhesive label on the package indicates the total weight of the electropump.
6.
WARNINGS
6.1. Checking pump/motor shaft rotation
Before
installing the electropump,
it is good practice to check that the pump shaft and/or the motor are moving freely. For this purpose, if
the pumps are supplied without a motor, check them by turning the pump coupling by hand. If the electropump is supplied as a complete unit,
check by turning the coupling by hand after having removed the coupling cover. When you have finished checking, put the coupling cover
back in its original position.
Do not force the shaft or the fan of the motor (if supplied) with pliers or other tools to try to free the pump, but look
for the cause of the blockage.
6.2.
New systems
Before running new systems the valves, pipes, tanks and couplings must be cleaned accurately. Often welding waste, flakes of oxide or other
impurities fall off after only a certain period of time. To prevent them from getting into the pump they must be caught by suitable filters. The
free surface of the filter must have a section at least 3 times larger than the section of the pipe on which the filter is fitted, so as not to create
excessive load losses. We recommend the use of TRUNCATED CONICAL filters made of corrosion-resistant materials (SEE DIN 4181):
(Filter for intake pipe)
1) Filter body
2) Narrow mesh filter
3) Differential pressure gauge
4) Perforated sheet
5) Pump intake aperture
6.3.
Protections
6.3.1.
Moving parts
In accordance with accident-prevention regulations, all moving parts (fans, couplings, etc.) must be accurately protected with
special devices (fan covers, coupling covers) before operating the pump.
1
2
3
4
5
Summary of Contents for NKM
Page 96: ... 93 105 ...
Page 98: ... 95 ...
Page 99: ... 96 ...
Page 117: ......
Page 118: ......
Page 119: ......