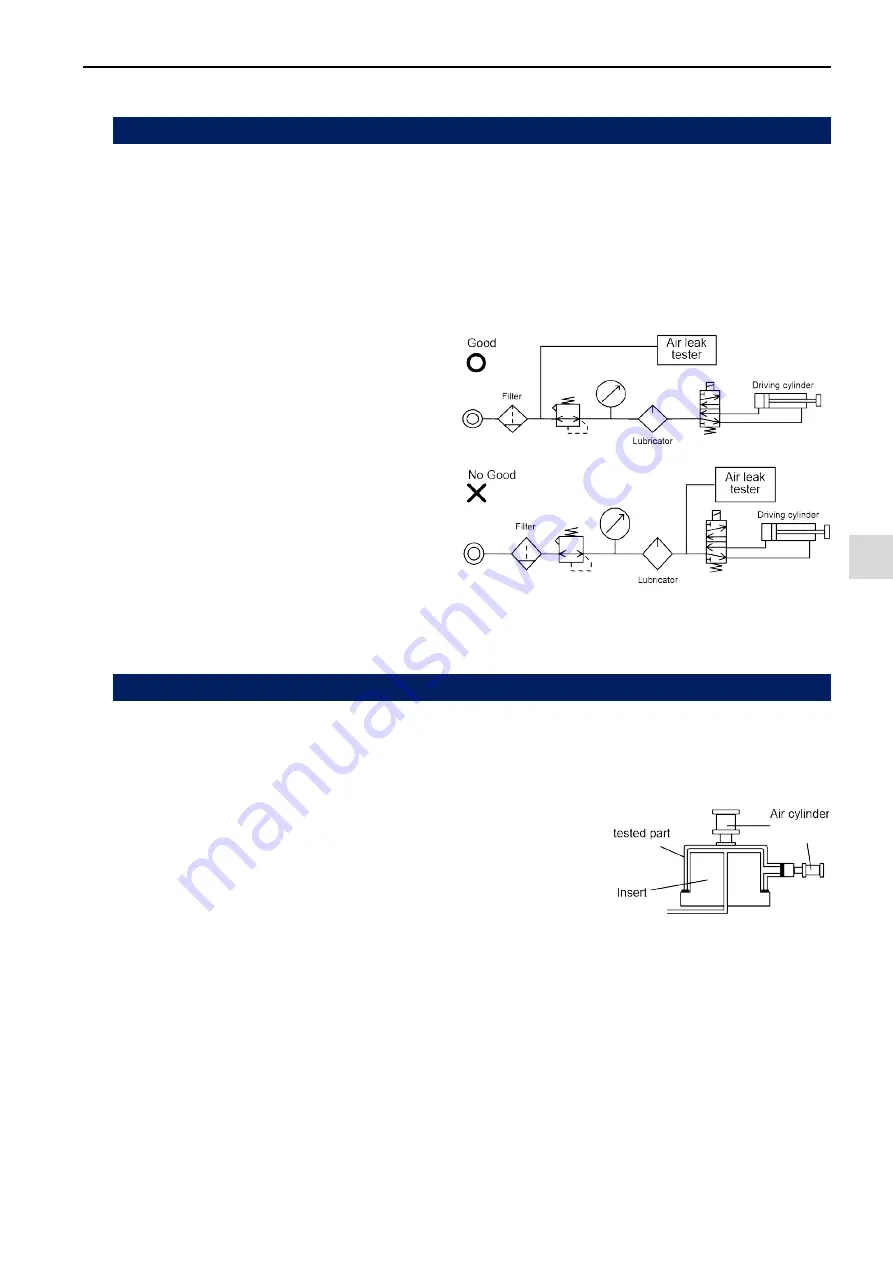
5 INSTALLATION
25
5.3.3 Notes on source air
1) Air that is supplied from a pressure source must be clean and dry. Water or oils penetrating inside of
the leak tester may cause the DP sensor to fail.
•
Symptoms of a differential pressure sensor failure caused by water and oil.
Water or oil present in the source air may result in a significant drift of the DPS offset to produce an
offset error or large leak failure, requiring repairs by the manufacturer.
•
Even though the leak tester model comes standard with an oil mist separator, add an additional oil
mist separator or air dryer to it if water or oils are present in the source air.
2) Keep the tubing free from condensation. If the tubing is installed in contact with the air outlet of an air
conditioner, the temperature difference may promote condensation.
3) Do not connect air passing through a driving
lubricator to the leak tester as shown in the
diagram. Never connect a pressure source
containing oils.
4) Notes on using a vacuum pump
If an oil rotating vacuum pump is used,
install an air release solenoid valve to
prevent oil back flow with the pump turned
off. Have the leak tester installed at a height
above the vacuum pump.
5
5
.
.
4
4
C
C
o
o
n
n
n
n
e
e
c
c
t
t
i
i
n
n
g
g
M
M
a
a
s
s
t
t
e
e
r
r
a
a
n
n
d
d
T
T
e
e
s
s
t
t
e
e
d
d
p
p
a
a
r
r
t
t
5.4.1 Notes on designing a sealing fixture
1) Internal and external leaks
The seal must be designed to prevent leaks from inside the tested part such as other sealed spaces,
gaps between part and seal and cavities that are not open to atmosphere, as well as external leaks.
Since those internal leaks are hardly visually noticeable, it requires extra attention.
2) Reducing internal volume of tested part
A smaller internal volume allows a shorter test time and gives better
sensitivity. A spacer and/or a filler can be used to reduce the
internal volume of the work. The material of the insert can be
resinoid but should not be plasterboard, wood or any porous
material.
3) Effects of plant temperature on leak testing
Temperature change of tested part causes drift in the measurement. In order to prevent these effects,
the part temperature must be stabilized.
Please consider following when installing leak tester.
•
Do not put the leak test station just after heating, cooling, welding or washing processes. The leak
tester works best with the tested part that is ambient temperature.
•
Avoid fluctuations in temperature while testing.
•
When the temperatures of the floor and test bench are different, and the tested part is taken from
the floor and then tested on the test bench, heat transfer will take place between the tested part
and the fixture. The tested parts should be stored at the same level as the test bench in order to
keep the temperature the same.
4) Seal packing deformation
Beware that clamping deforms seals, which causes change in part internal volume and erratic reading
especially in case the sealing surface is large.