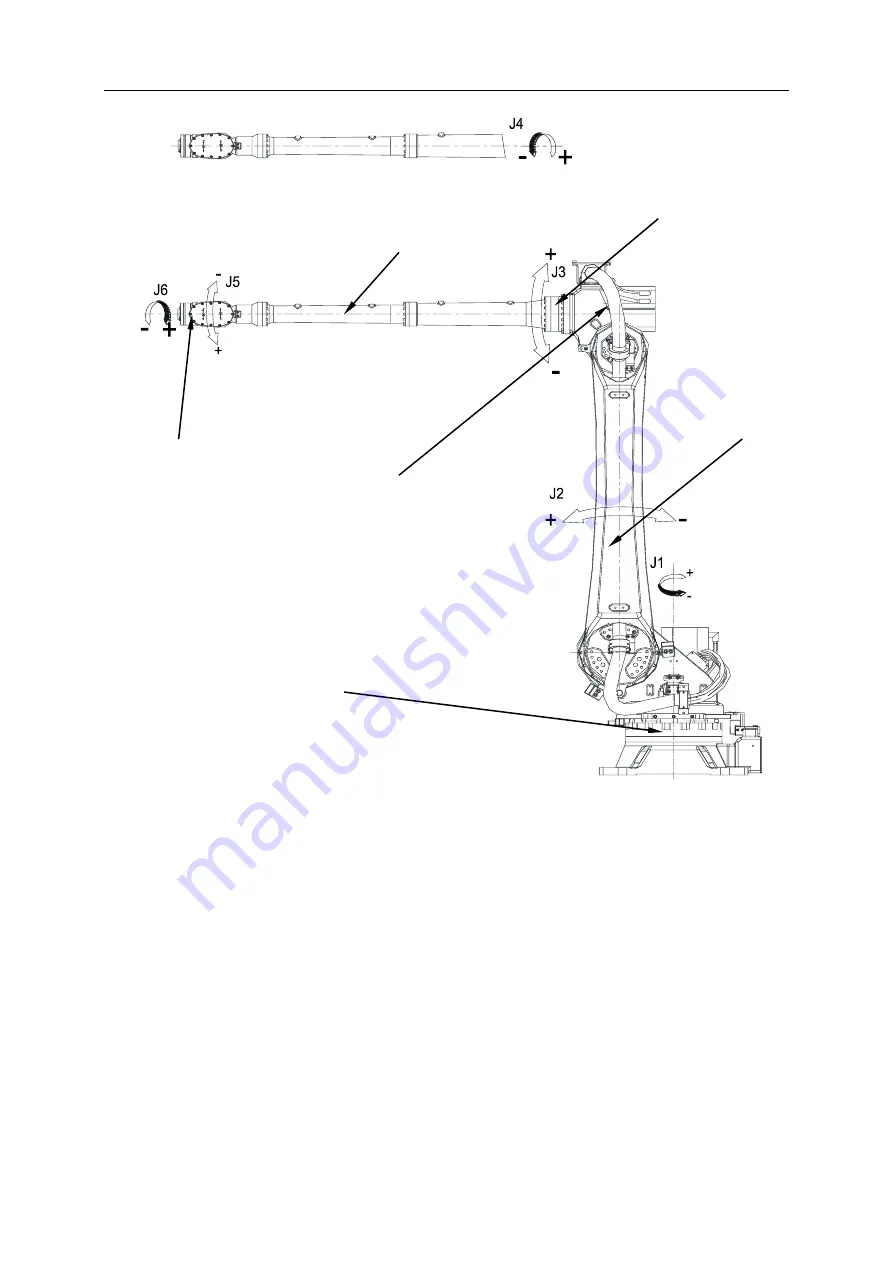
CMA (WuHu) Robotics CO., LTD
希美埃(芜湖)机器人技术有限公司
17
Fig 2.1Robot mechanical system diagram
图
2.1
机器人机械系统组成图
2.3 The mechanical performance parameters
2.3
机械性能参数
2.3.1 The definition of performance parameters
2.3.1
性能参数定义
The performance parameters of robot mainly includes working space, the robot load, the
robot movement speed, the robot's maximum motion range and repeat positioning accuracy.
机器人性能参数主要包括工作空间、机器人负载、机器人运动速度、机器人最大动
作范围和重复定位精度。
The big arm
大臂
The base components
底座部件
Forearm parts
小臂部件
Ontology pipeline package
本体管线包
Wrist parts
手腕部件
Forearm stretch
小臂加长
Summary of Contents for GR 6160
Page 7: ......
Page 75: ...CMA WuHu Robotics CO LTD 68 4 9 Fig 4 9 maintenance area...