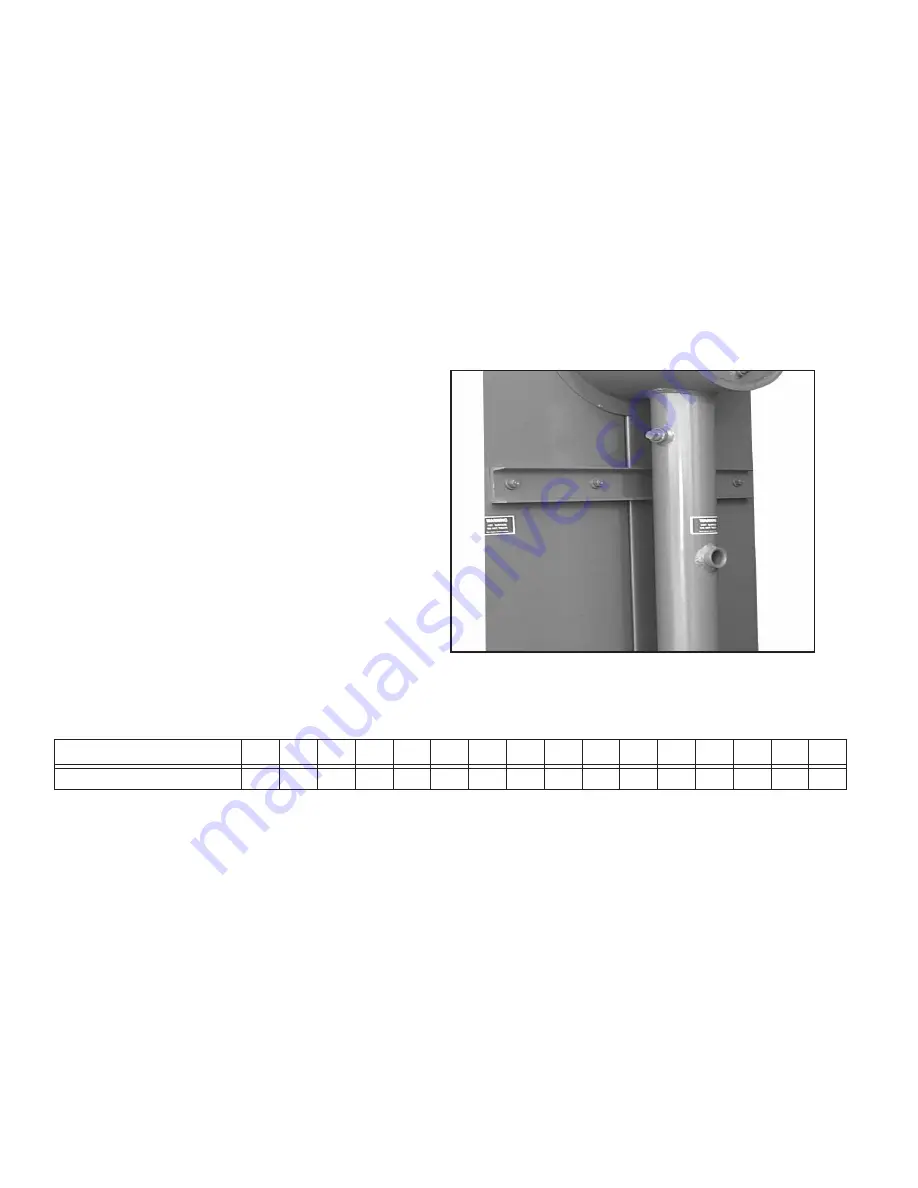
Chapter 3
General Description
3-4
750-177
Variations in water temperature and firing rates will result if care is not taken to ensure proportional flow through
the boilers. In extreme cases, differences in firing rates could result in a net header water temperature below
the desired temperature.
C. WATER REQUIREMENTS (STEAM BOILERS)
Deaeration
The most important factor in the life of a steam pressure vessel is the proper conditioning of the boiler feed
water. Corrosive gasses, such as oxygen and carbon dioxide, must be removed from the feed water in order to
prevent degradation of the pressure vessel. For this reason Cleaver- Brooks recommends the use of a deaeration
system as an integral part of a complete boiler installation. If circumstances do not allow the implementation of
a deaeration system, then serious consideration should be given to effective alternatives such as a feed water
preheater combined with a chemical oxygen scavenger. Complete boiler water chemistry parameters are given
in Table 3-3.
Feed Water Supply
Figure 3-3: Feed Water Inlet Steam Boiler
The internal dynamics of the Model FLX steam boilers
require the capability to deliver large quantities of feed
water to the boiler on demand. (Feed water inlet Figure
3-3.) Sudden changes in firing rate or operating
pressure of the
boiler will initiate a “call for water” from the
make-up controller, which will require that the feed water be
delivered to the boiler in sufficient quantities to prevent a low
water cutoff trip. Table 3-2 lists the minimum feed water
flow requirements for the various boiler models. In addition,
feed water must be warmed to a minimum of 60°F. in order
to ensure reliable operation of the boiler. The feed water
supply should be adjusted to deliver water to the boiler at or
above these minimum rates.
Table: 3-2
Minimum Boiler Feed Water Flow Rates (Steam Boiler)
BOILER MODEL
150
200
250
300
350
400
450
500
550
600
700
800
900
1000 1100 1200
Minimum Feed Rate (gpm)
4.9
6.6
8.2
9.9
11.6 13.2 14.9 16.5 18.2 19.8 23.1 26.4 29.7 33.0 36.3 39.6
Note: Feedwater to the boiler must be at least 60
F for minimum performance; 212
F is preferred.
D. Water Treatment
Properly treated boiler water will result in maximum effectiveness and long trouble-free life of the pressure
vessel. Contact your local Cleaver-Brooks Representative or water management consultant for complete
information on how to prevent damage resulting from inadequate water treatment.
The objectives of water treatment in general are to:
•
Prevent hard scale and soft sludge deposits that inhibit heat transfer and that could lead to overheated metal and
costly downtime and repairs.
•
Eliminate corrosive gases in the supply or boiler water.
Summary of Contents for FLX 1000
Page 12: ...Chapter 1 General Description 1 6 750 177...
Page 68: ...Chapter 2 Profire V Burner 2 56 750 177...
Page 90: ...Chapter 4 Sequence of Operation 4 10 750 177...
Page 104: ...Chapter 5 Adjustment Procedures 5 14 750 177...
Page 110: ...Chapter 6 Troubleshooting 6 6 750 177...
Page 122: ...8 2 750 177 Figure 8 1 Typical Hot Water Flextube Casing...
Page 124: ...8 4 750 177 Figure 8 2 Typical Low Pressure Steam Flextube Casing...
Page 126: ...8 6 750 177 Figure 8 3 Typical High Pressure Steam Flextube Casing...
Page 128: ...Parts Chapter 8 8 8 750 177 Steam Pressure Controls...
Page 129: ...Chapter 8 Parts 750 177 8 9 Water Level Controls...
Page 130: ...Parts Chapter 8 8 10 750 177 Water Level Controls continued...
Page 131: ...Chapter 8 Parts 750 177 8 11 Water Column Main and Aux 15 Steam...
Page 132: ...Parts Chapter 8 8 12 750 177 Water Column Main and Aux 150 Steam...
Page 133: ...Chapter 8 Parts 750 177 8 13 Safety Valves...
Page 134: ...Parts Chapter 8 8 14 750 177...
Page 135: ......
Page 136: ...e mail info cleaverbrooks com Web Address http www cleaverbrooks com...