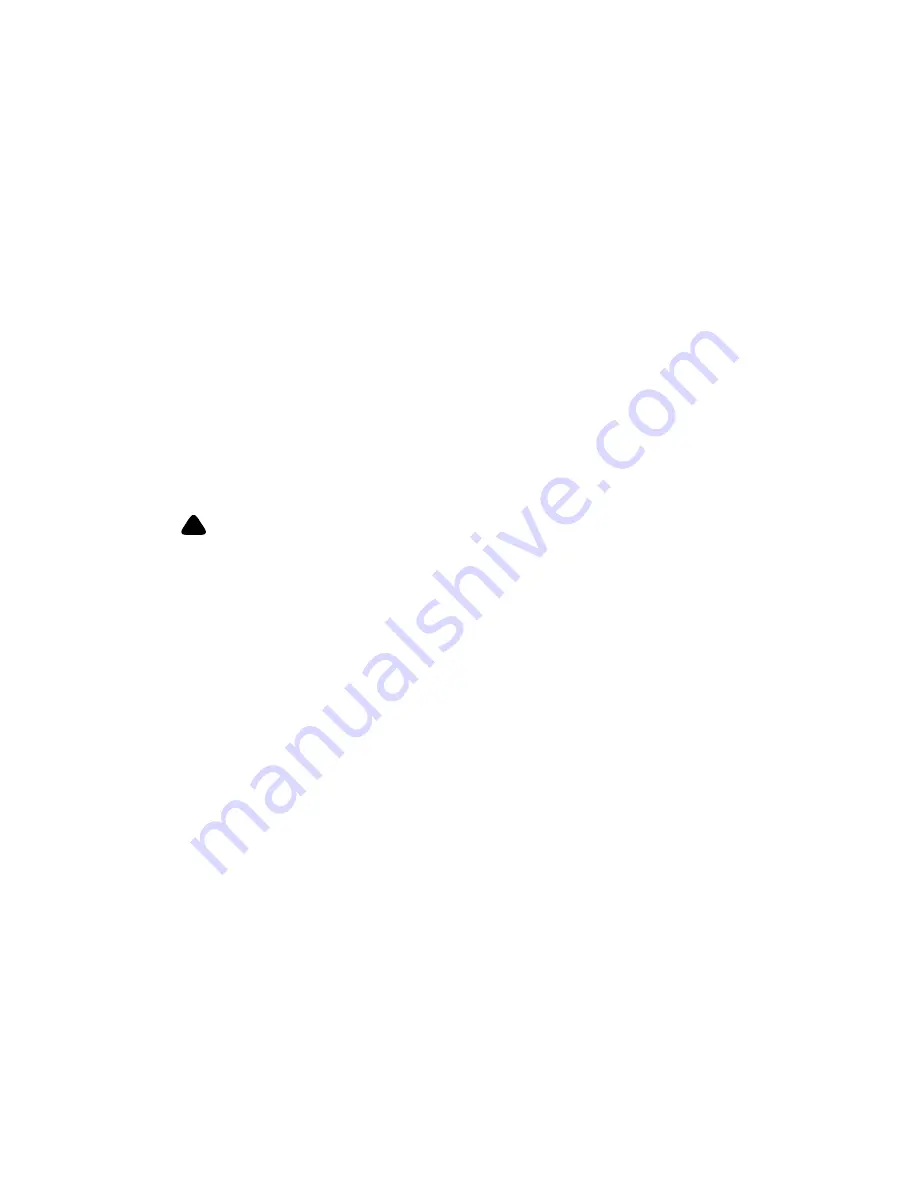
Chapter 7
Inspection and Maintenance
7-6
750-177
Always be sure of the boiler water level. The water column should be blown down routinely. Check samples
of boiler water and condensate in accordance with procedures recommended by your water consultant. Refer
to sections E and I in Chapter 3 for blowdown instructions and internal inspection procedures.
A typical water level control is mounted in the water column and has float actuated mercury switches. One
switch is connected to the burner limit circuit and will stop the burner if a low water condition occurs. The
other switch is connected to the feedwater circuit to energize a water pump or feeder valve to maintain water
at the proper operating level.
Usually, the control is of the automatic reset type and will remake the limit circuit when the water level is
restored. Some applications require that a control be equipped with a manual reset mechanism that must be
manually reset before the burner can be restarted. This is usually accomplished with the use of a second or
auxiliary control that has this feature.
Since low water cutoff devices are generally set by the original manufacturer, no attempt should be made to
adjust these controls to alter the point of low water cutoff or point of pump cut-in or cut-out. If a low water
device should become erratic in operation or if its setting changes from previous established levels, check for
reasons and correct: Repair or replace as required.
These controls normally function for long periods of time, which may lead to laxity in testing on the assumption
that normal operation will continue indefinitely.
The controls' operation may be checked by stopping the water supply to the boiler while the burner is operating
at low fire. While under constant attendance, allow the water level to drop at a normal rate. Check for proper
operation of the feedwater controller and the low water cutoffs.
!
DANGER
CAUTION
If a control does not break the circuit to stop the burner at the proper point then shut down the burn-
er immediately. Failure to do so may result in damage to the equipment.
Do not restart until all cross-connecting piping is checked for obstructions. Also check the float bowl. If these
are clean, repair or replace the control. Repeat the above test to ensure proper operation prior to returning the
boiler to service.
On a steam boiler, the head mechanism of the low water cutoff device(s) should be removed from the bowl
at least once a month to check and clean the float ball, the internal moving parts, and the bowl or water
column.
Remove the pipe plugs from the tees or crosses and make certain the cross- connecting piping is clean and
free of obstructions. Controls must be mounted in a plumb position for proper performance. Determine that
piping is vertically aligned after shipment and installation and throughout the life of the equipment.
A scheduled blowdown of the water controls on a steam boiler should be maintained.
Water Gauge Glass
A broken or discolored glass must be replaced at once. Periodic replacement should be a part of the
maintenance program. Always use new gaskets when replacing a glass. Use a proper size rubber packing. Do
not use “loose packing,” which could be forced below the glass and possibly plug the valve opening.
Close the valves when replacing the glass. Slip a packing nut, a packing washer, and packing ring onto each
end of the glass. Insert one end of the glass into the upper gauge valve body far enough to allow the lower
end to be dropped into the lower body. Slide the packing nuts onto each valve and tighten.
If the glass is replaced while the boiler is in service, open the blowdown and slowly bring the glass to operating
temperature by cracking the gauge valves slightly. After glass is warmed up, close the blowdown valve and
open the gauge valves completely.
Check trycocks and gauge cocks for freedom of operation and clean as required.
Summary of Contents for FLX 1000
Page 12: ...Chapter 1 General Description 1 6 750 177...
Page 68: ...Chapter 2 Profire V Burner 2 56 750 177...
Page 90: ...Chapter 4 Sequence of Operation 4 10 750 177...
Page 104: ...Chapter 5 Adjustment Procedures 5 14 750 177...
Page 110: ...Chapter 6 Troubleshooting 6 6 750 177...
Page 122: ...8 2 750 177 Figure 8 1 Typical Hot Water Flextube Casing...
Page 124: ...8 4 750 177 Figure 8 2 Typical Low Pressure Steam Flextube Casing...
Page 126: ...8 6 750 177 Figure 8 3 Typical High Pressure Steam Flextube Casing...
Page 128: ...Parts Chapter 8 8 8 750 177 Steam Pressure Controls...
Page 129: ...Chapter 8 Parts 750 177 8 9 Water Level Controls...
Page 130: ...Parts Chapter 8 8 10 750 177 Water Level Controls continued...
Page 131: ...Chapter 8 Parts 750 177 8 11 Water Column Main and Aux 15 Steam...
Page 132: ...Parts Chapter 8 8 12 750 177 Water Column Main and Aux 150 Steam...
Page 133: ...Chapter 8 Parts 750 177 8 13 Safety Valves...
Page 134: ...Parts Chapter 8 8 14 750 177...
Page 135: ......
Page 136: ...e mail info cleaverbrooks com Web Address http www cleaverbrooks com...