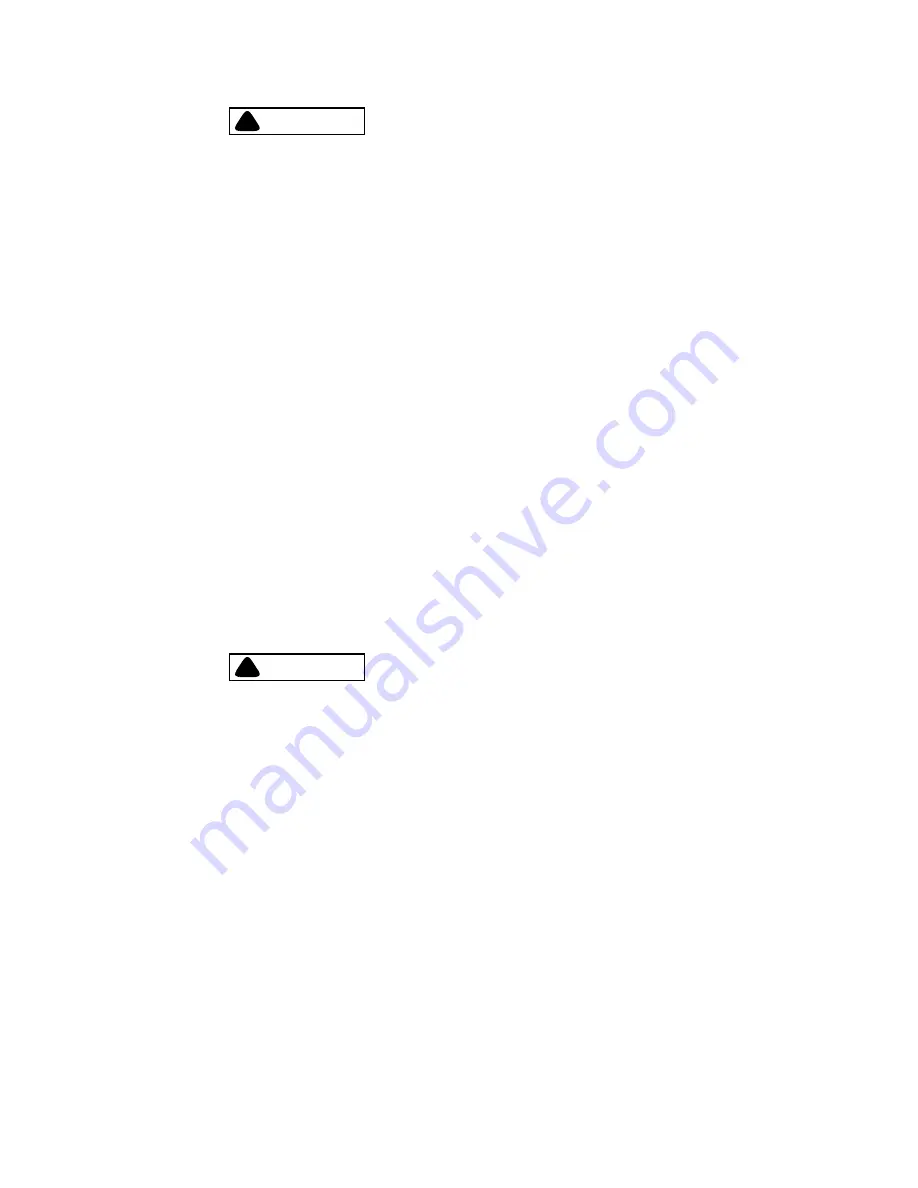
Inspection and Maintenance
Chapter 7
750-177
7-9
!
DANGER
WARNING
Be sure to disconnect the main power supply to the boiler in order to prevent the possibility of electrical shock,
which could result in serious personal injury or death.
Check the coil position and make sure that any insulating washers or retaining springs are reinstalled in the
proper order.
H. Refractory
The boiler is shipped with completely installed refractory. High temperature refractory lines the burner door
and floor of the boiler. Front and rear walls, side casing panels, the roof section, the bottom drum and the
drum vent are protected with high temperature insulation. Preventive maintenance through periodic inspection
will keep the operator aware of the condition of the refractory and insulation and will guard against unexpected
downtime for repairs.
I. Casing Seals
The most obvious indication of a problem is the appearance of discolored paint on the casing or soot and hot
gases escaping at seal joints. It is important that at start-up any problems are noted and corrected before the
boiler is put back into operation. The following are areas requiring inspection.
Burner Door
Inspect the area around the door and look for discolored paint or evidence of combustion gas leakage. If a
problem is noted or the door is being opened for scheduled maintenance look for warped sealing surfaces and
make sure that the insulation on the front wall around the door has not pushed away from the wall. Cracks
may appear in the burner door refractory as a result of expansion and contraction from operation. If cracks are
larger than 1/8” when the refractory is cooled, the cracks should be filled with a high temperature bonding
air-dry mortar such as Cleaver- Brooks “Corline.”
!
DANGER
WARNING
Disconnect main power to the boiler and the pilot fuel supply to the burner before the burner door is opened.
Electrical power and fuel supply must remain shut off at all times when the burner door is open. Failure to
heed this warning could result in serious personal Injury or death.
Access to the boiler furnace area is gained through the burner door opening at the front of the boiler. Whenever
the burner is opened, the gasket and gasket surfaces of the burner door should be inspected. A good seal
between the burner door and the boiler is necessary to prevent leakage of combustion gases and loss of
efficiency. Combustion gas leaks can cause hot spots with subsequent damage to the burner door and
surrounding refractory. Damaged or hardened gaskets must be replaced before the burner is put back in
operation.
If a new gasket is necessary, remove the old gasket and clean the gasket surface on the wall and burner door.
A spray adhesive is used to hold the rope gasket in place around the burner opening. A high temperature
silicone may be needed to seal under the rope gasket at the wall seams. The rope gasket should wrap around
the opening at least two times.
Before the burner door is closed, inspect studs and clean threads if necessary with 1/2"-13 die. Apply a small
amount of Cleaver-Brooks "Never-Seez" (p.n. 797-1814 or 797-1816) to the studs. Any nuts that are difficult
to thread on studs should be replaced. Door fasteners should be run in and tightened evenly to avoid distorting
the door or damaging the gasket. Start tightening at the top and proceed around the door, alternately tightening
opposite fasteners until all are snug. After the boiler is back in operation, check for gas leaks around the door
opening, and retighten the fasteners as required to provide a gas-tight seal.
Summary of Contents for FLX 1000
Page 12: ...Chapter 1 General Description 1 6 750 177...
Page 68: ...Chapter 2 Profire V Burner 2 56 750 177...
Page 90: ...Chapter 4 Sequence of Operation 4 10 750 177...
Page 104: ...Chapter 5 Adjustment Procedures 5 14 750 177...
Page 110: ...Chapter 6 Troubleshooting 6 6 750 177...
Page 122: ...8 2 750 177 Figure 8 1 Typical Hot Water Flextube Casing...
Page 124: ...8 4 750 177 Figure 8 2 Typical Low Pressure Steam Flextube Casing...
Page 126: ...8 6 750 177 Figure 8 3 Typical High Pressure Steam Flextube Casing...
Page 128: ...Parts Chapter 8 8 8 750 177 Steam Pressure Controls...
Page 129: ...Chapter 8 Parts 750 177 8 9 Water Level Controls...
Page 130: ...Parts Chapter 8 8 10 750 177 Water Level Controls continued...
Page 131: ...Chapter 8 Parts 750 177 8 11 Water Column Main and Aux 15 Steam...
Page 132: ...Parts Chapter 8 8 12 750 177 Water Column Main and Aux 150 Steam...
Page 133: ...Chapter 8 Parts 750 177 8 13 Safety Valves...
Page 134: ...Parts Chapter 8 8 14 750 177...
Page 135: ......
Page 136: ...e mail info cleaverbrooks com Web Address http www cleaverbrooks com...