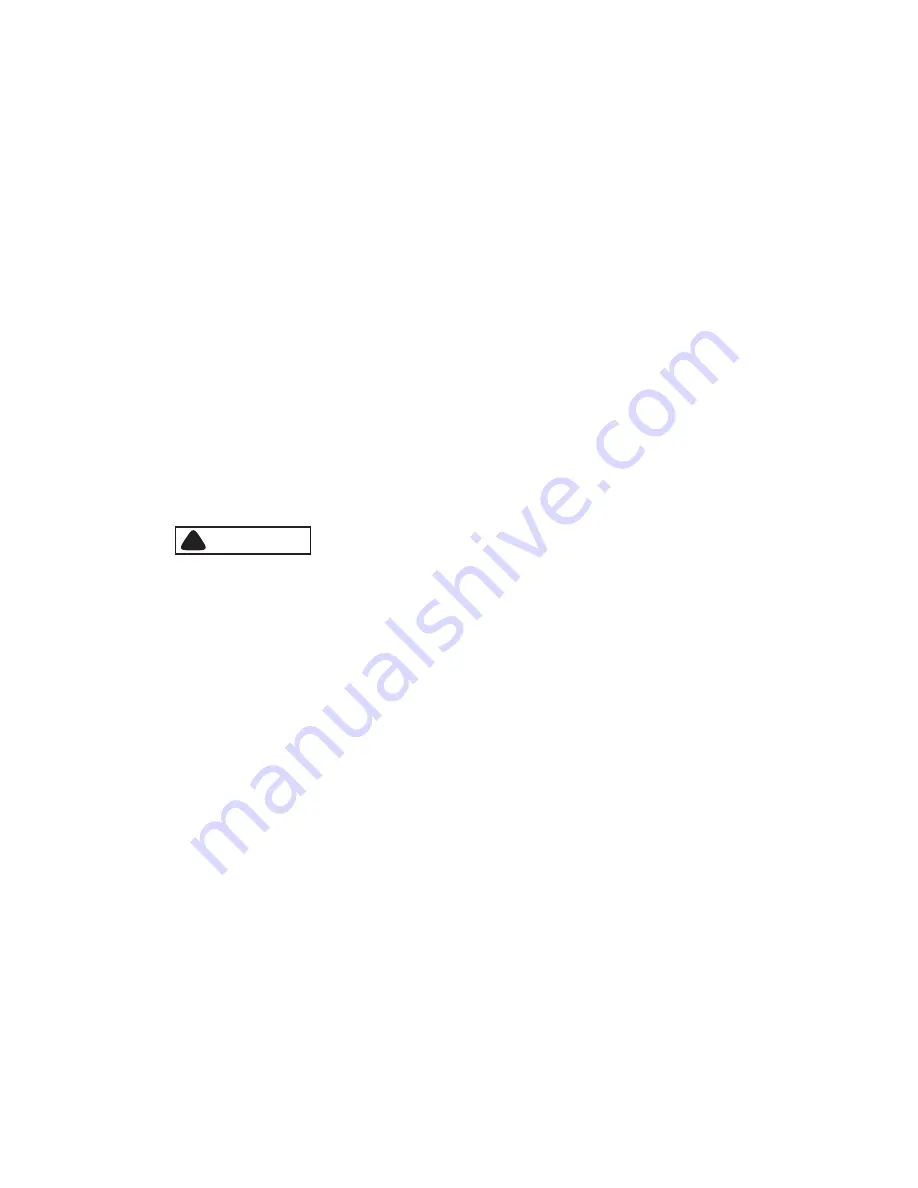
Chapter 3
General Description
3-10
750-177
I. Periodic Inspection
Insurance regulations or local codes and good maintenance will require that the pressure vessel be inspected
periodically by an authorized inspector. Sufficient notice is generally required to allow removal of the boiler
from service and preparation for inspection. An internal inspection may be required before cleaning or flushing.
Have the following information available for the inspector: boiler design, dimensions, generating capacity,
operating pressure and temperature, time in service, defects found previously, and any repairs or
modifications made to the unit. Reference records of previous inspections also should be available. Be
prepared to perform any testing required by the inspector, including a hydrostatic test.
When shutting down a boiler, the load should be reduced gradually and the pressure vessel should be cooled
at a rate that avoids a temperature differential that can cause harmful stresses. Normally, all pressure should
be relieved before a vessel is drained in order to prevent uneven contraction and temperature differential that
can cause tubes to leak. Draining the unit too quickly may cause the baking of deposits that may be present
on the heating surfaces.
Note: Check to see that system valves, feedwater valves, all fuel valves, expansion tank, and
electrical switches are shut off prior to opening the handholes or the burner access door. After
proper cooling and draining of the vessel, flush out the waterside with a high pressure water stream.
Remove any scale or deposits from the waterside surfaces and check for internal or external
corrosion or leakage.
Fireside surfaces also should be cleaned so that metal surfaces, welds, joints, tube fittings, and any previous
repairs can be readily checked.
!
DANGER
WARNING
To avoid the hazard of electrical shock, which could cause serious personal injury or death, the use
of a low voltage flashlight is recommended during an internal inspection.
Fireside Inspection
Access for inspection of the firing chamber, or furnace, is gained through the hinged burner door. Inspection
of the upper pass requires removal of the side casing panels and second and fourth pass cover plates. Refer
to Chapter 8, Section C, “Fireside Cleaning,” for information regarding outer and inner casing removal.
Fireside tube surfaces should be checked for corrosion or accumulation of soot. Use a vacuum cleaner and
wire brush to remove light corrosion or soot.
Localized, heavy corrosion on fireside tube surfaces may indicate a leaking tube or ferrule connection. If a tube
or tube ferrule leak is indicated, the source of the leakage must be found and repaired before putting the boiler
back in service. A leak from a tube-to-drum connection may require removal and reseating of the tube. A
heavily corroded or leaking tube must be replaced in order to assure continued reliable operation of the boiler.
Information regarding tube replacement can be obtained from your local Cleaver-Brooks authorized
representative.
Waterside Inspection
Check all water piping and valves for leaks, wear, corrosion, and other damage. Replace or repair the piping
and valves as necessary. Inspection covers at one end of the upper and lower drums provide access to the
interior of the drums for visual inspection or washout. The interior surfaces of the drums should be examined
for any sign of corrosion or accumulation of deposits.
Summary of Contents for FLX 1000
Page 12: ...Chapter 1 General Description 1 6 750 177...
Page 68: ...Chapter 2 Profire V Burner 2 56 750 177...
Page 90: ...Chapter 4 Sequence of Operation 4 10 750 177...
Page 104: ...Chapter 5 Adjustment Procedures 5 14 750 177...
Page 110: ...Chapter 6 Troubleshooting 6 6 750 177...
Page 122: ...8 2 750 177 Figure 8 1 Typical Hot Water Flextube Casing...
Page 124: ...8 4 750 177 Figure 8 2 Typical Low Pressure Steam Flextube Casing...
Page 126: ...8 6 750 177 Figure 8 3 Typical High Pressure Steam Flextube Casing...
Page 128: ...Parts Chapter 8 8 8 750 177 Steam Pressure Controls...
Page 129: ...Chapter 8 Parts 750 177 8 9 Water Level Controls...
Page 130: ...Parts Chapter 8 8 10 750 177 Water Level Controls continued...
Page 131: ...Chapter 8 Parts 750 177 8 11 Water Column Main and Aux 15 Steam...
Page 132: ...Parts Chapter 8 8 12 750 177 Water Column Main and Aux 150 Steam...
Page 133: ...Chapter 8 Parts 750 177 8 13 Safety Valves...
Page 134: ...Parts Chapter 8 8 14 750 177...
Page 135: ......
Page 136: ...e mail info cleaverbrooks com Web Address http www cleaverbrooks com...