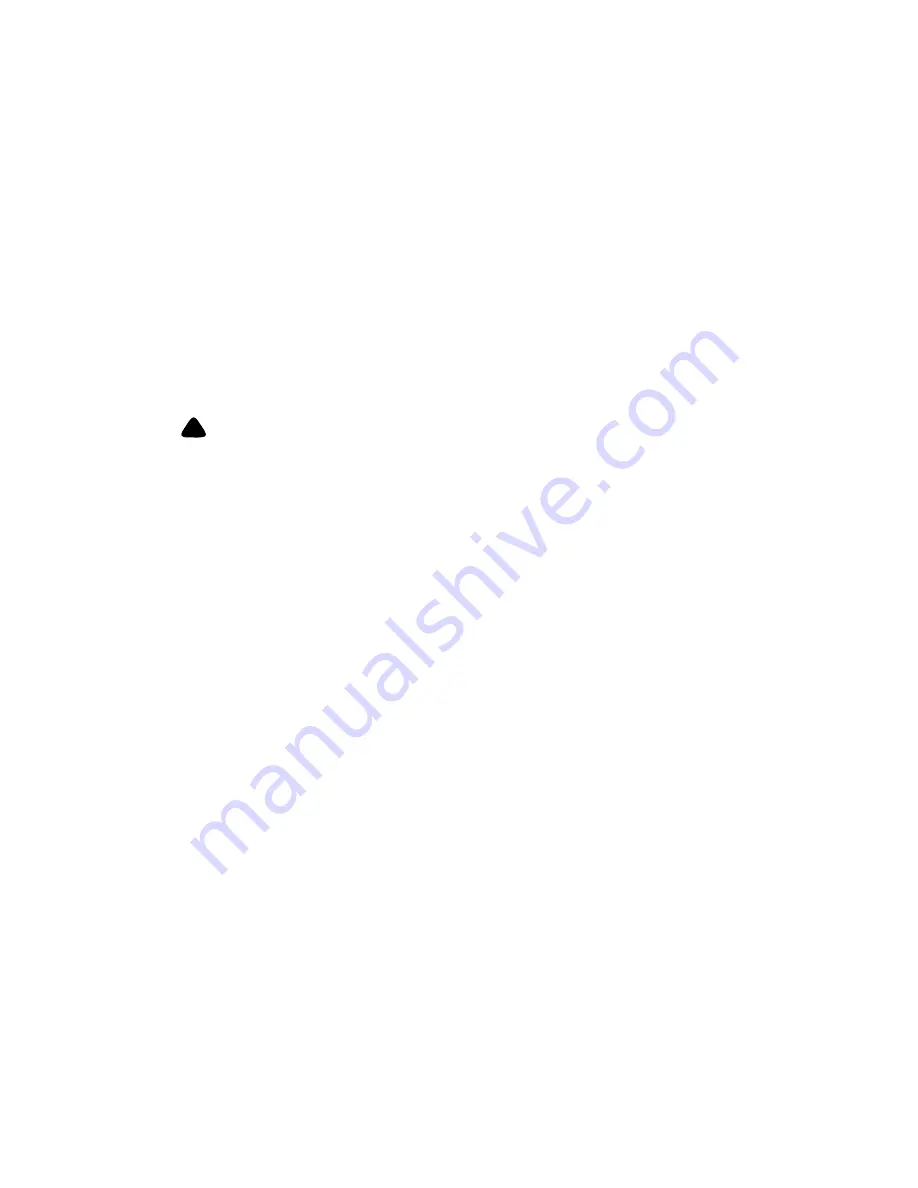
Chapter 2
Profire V Burner
2-14
750-177
INSTALLATION CHECKLIST
1.
All burners are carefully assembled and tested at the factory, but before being placed in service all connectors should again be
checked for looseness caused during shipment.
Check:
a. Electrical terminals in the control panel and on all electrical components.
b. Pipe fittings and unions.
c. Tubing connections.
d. Nuts, bolts, screws.
2.
Open all necessary oil shutoff valves. Do not run pumps or fuel unit without oil.
3.
Before connecting electrical current to any component, be sure the voltage is the same as that specified on component name-
plates.
4.
Before burner operation, be sure all motors are rotating in the proper direction.
5.
Before firing, make sure the burner firing head and dry areas of the boiler are protected with refractory. The burner mounting
flange must be properly sealed against the vessel front plate.
6.
Make certain that the operator in charge is properly instructed in operation and maintenance procedures.
!
DANGER
CAUTION
BEFORE OPENING THE MANUAL GAS SHUTOFF VALVES, READ THE REGULATOR INSTRUCTIONS CAREFULLY. THE IN-
STRUCTIONS ARE IN THE REGULATOR BOX. FOLLOW THE MANUFACTURER RECOMMENDATIONS. OPEN SHUTOFF
VALVE ON THE INLET SIDE OF THE REGULATOR SLOWLY AND CAREFULLY TO ALLOW INLET PRESSURE TO BUILD UP
SLOWLY IN THE REGULATOR UNTIL IT IS FULLY PRESSURIZED. OPEJNING THE SHUTOFF VALVE QUICKLY WILL DAM-
AGE THE REGULATOR. DO NOT EXCEED THE REGULATOR PRESSURE RATINGS.
V BURNER FIRING MODES
Different modulation modes are available with the Profire V burner. The Model FLX will utilize one of the
following:
Low - High -Low (60% damper purge).
Low - High -Low (open damper purge).
Full Modulation (open damper purge).
See following pages for operating descriptions of each firing mode.
Summary of Contents for FLX 1000
Page 12: ...Chapter 1 General Description 1 6 750 177...
Page 68: ...Chapter 2 Profire V Burner 2 56 750 177...
Page 90: ...Chapter 4 Sequence of Operation 4 10 750 177...
Page 104: ...Chapter 5 Adjustment Procedures 5 14 750 177...
Page 110: ...Chapter 6 Troubleshooting 6 6 750 177...
Page 122: ...8 2 750 177 Figure 8 1 Typical Hot Water Flextube Casing...
Page 124: ...8 4 750 177 Figure 8 2 Typical Low Pressure Steam Flextube Casing...
Page 126: ...8 6 750 177 Figure 8 3 Typical High Pressure Steam Flextube Casing...
Page 128: ...Parts Chapter 8 8 8 750 177 Steam Pressure Controls...
Page 129: ...Chapter 8 Parts 750 177 8 9 Water Level Controls...
Page 130: ...Parts Chapter 8 8 10 750 177 Water Level Controls continued...
Page 131: ...Chapter 8 Parts 750 177 8 11 Water Column Main and Aux 15 Steam...
Page 132: ...Parts Chapter 8 8 12 750 177 Water Column Main and Aux 150 Steam...
Page 133: ...Chapter 8 Parts 750 177 8 13 Safety Valves...
Page 134: ...Parts Chapter 8 8 14 750 177...
Page 135: ......
Page 136: ...e mail info cleaverbrooks com Web Address http www cleaverbrooks com...