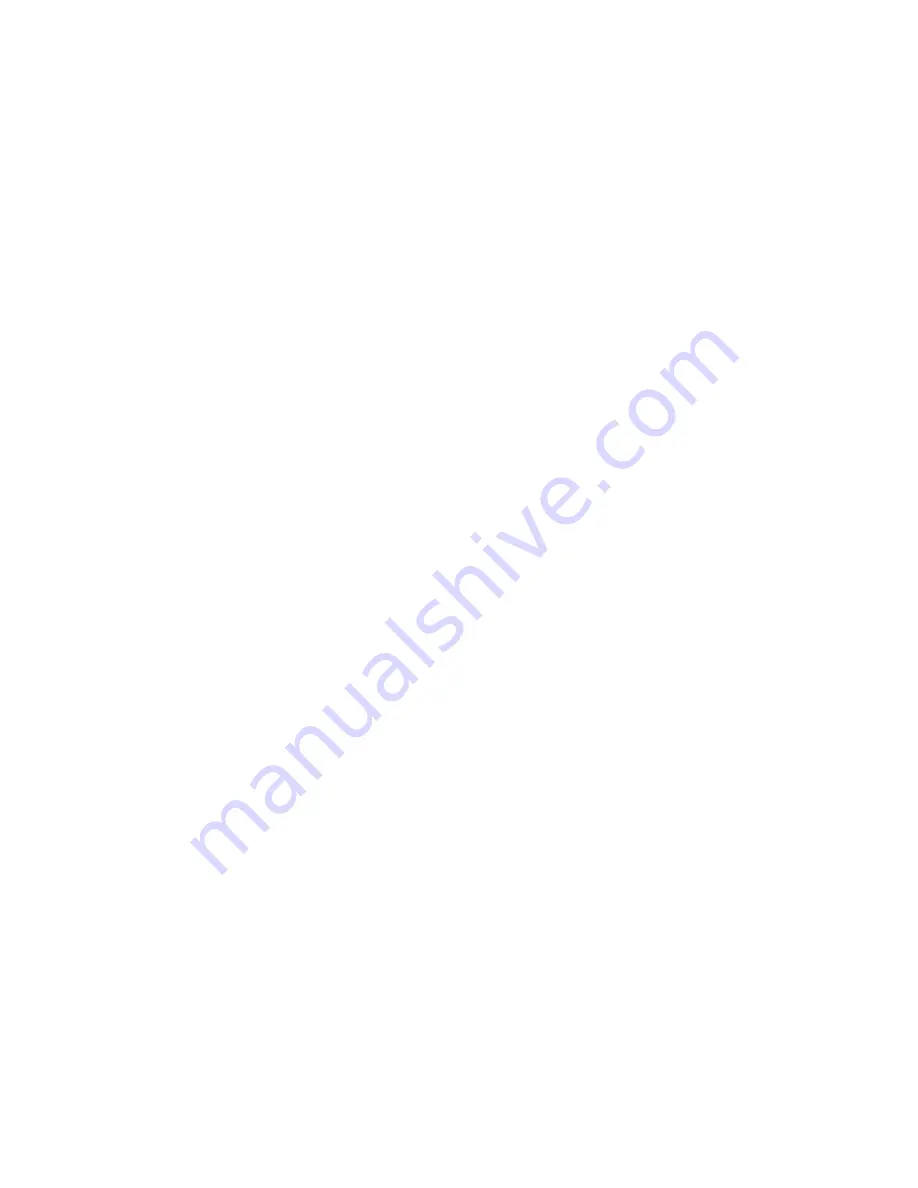
Chapter 2
Profire V Burner
2-2
750-177
OPERATING CONTROLS - PANEL
The burner control panel may be integral to the burner or remote, and contains: a flame safeguard
programming control, motor relays (starters), and terminal strips mounted internally on a panel
subbase.Lights, switches, and a control circuit breaker are mounted externally on the panel.
The following table lists typical panel items. Some or all of the items may be provided depending on the burner
configuration selected.
1. ON-OFF BURNER SWITCH
2. FUEL SELECTOR SWITCH - Gas-Off-Oil
Gas position: Selects gas as the firing fuel
Off position: Burner off
Oil position: Selects oil as the firing fuel
3. CONTROL CIRCUIT BREAKER
Supplementary low overcurrent protection only. No larger than 15 amps.
4. AUTO-MANUAL MODULATION SELECTOR SWITCH
Auto position: Selects boiler modulation control. In this position, the burner will operate automatically in response
to load demand.
Manual position: Selects 135 ohm potentiometer for manual modulating control.
5. MANUAL MODULATING CONTROL -
135 ohm (full modulation burners only) increases or decreases the burner
firing rate.
6. SIGNAL LAMPS
a) LOAD DEMAND (white): Illuminates when the control circuit is energized (powered).
b) LOW WATER (red): Illuminates when the water level in the boiler gets too low.
c) FUEL VALVE (green): Illuminates when the main fuel valve or valves (gas or oil) are energized (open).
d) FLAME FAILURE (red): Illuminates when the flame safeguard system fails to detect pilot or main flame.
FLAME SAFEGUARD CONTROLS
The flame safeguard controls the burner's operating sequence: pre-purge, trial for ignition, main flame and
shutdown. This safety control also includes flame detection system to confirm proper operation or cause a
manual reset lockout in the event of a pilot or main flame failure. External controls connected to the flame
control's limit circuit, such as the boiler operating control, will trigger normal burner startup, and upon
reaching operating set point, normal burner shutdown. Safety devices in the flame control's running interlock
circuit, such as the combustion air switch, will cause an immediate safety shut down if conditions are not
correct for safe operation.
When a parallel positioning system is furnished, the flame safeguard may be incorporated as an integral
component to the parallel positioning control. Consult boiler controls documentation. If using a C-B Hawk
control system refer to manual 750-366 (Hawk 1000) or 750-342 (Hawk 4000) and to the flame safeguard
manual 750-234 (CB780E) or 750-264 (CB120).
FIRING RATE CONTROLS
LHL burners use a two position actuator and linkage to control the air and gaseous fuels (oil burners control
oil flow with electric valves). At startup fire, the air damper and fuel valves are positioned for stable low fire
operation. When the actuator is commanded to its second position, the linkage drives the air damper and fuel
valves open until high fire is reached. LHL burners typically use a boiler-mounted control that keeps the burner
at its low fire rate to prevent thermal shock, until conditions are suitable for high fire.
Full modulation burners are capable of firing at any rate between the burner's low and high fire limits. For
“single point” modulating systems, a single rotary actuator controls both air and fuel volume via control arms
and linkage attached to its shaft. As the actuator rotates from low to high fire, the linkage opens the air damper
A
B
C
D
E
F
G
8
Summary of Contents for FLX 1000
Page 12: ...Chapter 1 General Description 1 6 750 177...
Page 68: ...Chapter 2 Profire V Burner 2 56 750 177...
Page 90: ...Chapter 4 Sequence of Operation 4 10 750 177...
Page 104: ...Chapter 5 Adjustment Procedures 5 14 750 177...
Page 110: ...Chapter 6 Troubleshooting 6 6 750 177...
Page 122: ...8 2 750 177 Figure 8 1 Typical Hot Water Flextube Casing...
Page 124: ...8 4 750 177 Figure 8 2 Typical Low Pressure Steam Flextube Casing...
Page 126: ...8 6 750 177 Figure 8 3 Typical High Pressure Steam Flextube Casing...
Page 128: ...Parts Chapter 8 8 8 750 177 Steam Pressure Controls...
Page 129: ...Chapter 8 Parts 750 177 8 9 Water Level Controls...
Page 130: ...Parts Chapter 8 8 10 750 177 Water Level Controls continued...
Page 131: ...Chapter 8 Parts 750 177 8 11 Water Column Main and Aux 15 Steam...
Page 132: ...Parts Chapter 8 8 12 750 177 Water Column Main and Aux 150 Steam...
Page 133: ...Chapter 8 Parts 750 177 8 13 Safety Valves...
Page 134: ...Parts Chapter 8 8 14 750 177...
Page 135: ......
Page 136: ...e mail info cleaverbrooks com Web Address http www cleaverbrooks com...