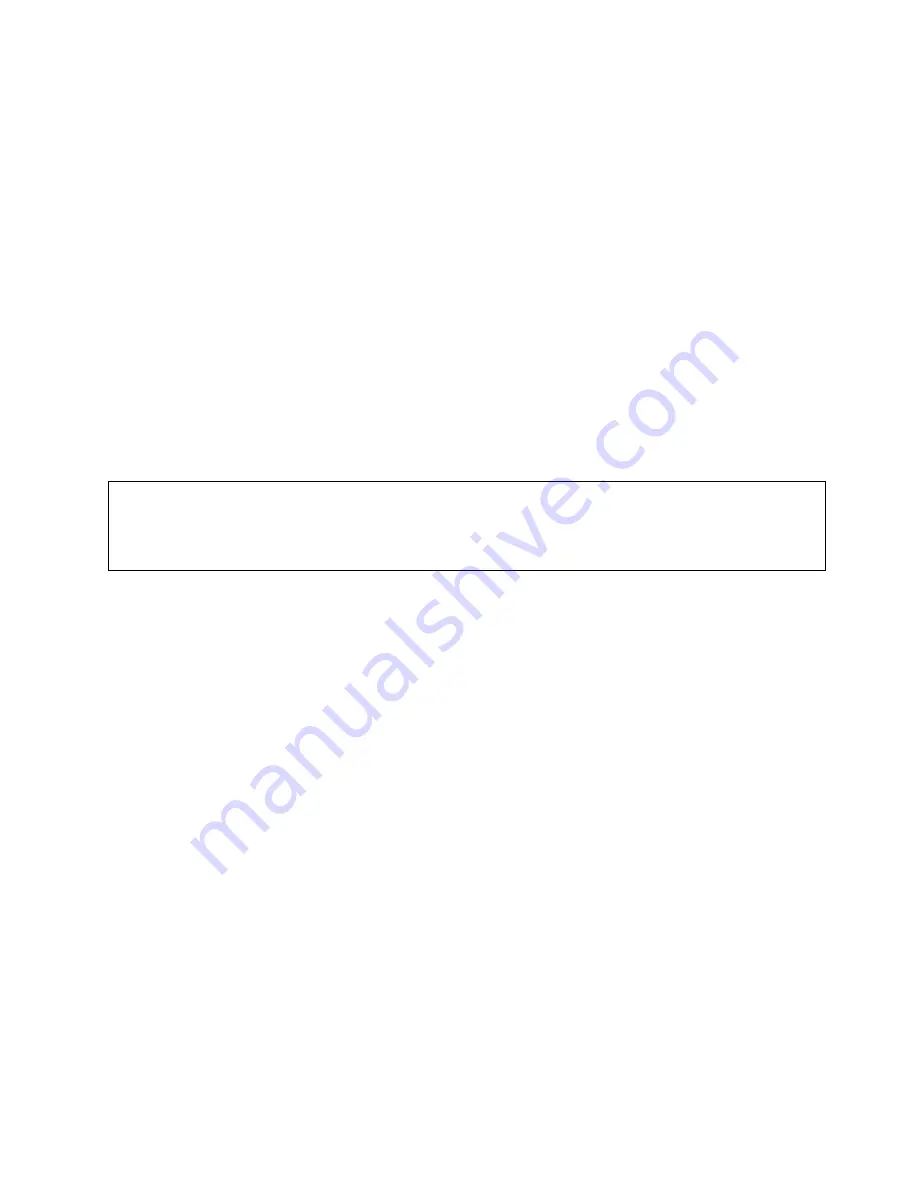
Profire V Burner
Chapter 2
750-177
2-25
The burner should be set up and maintained to yield smoke spot levels less than a #1 spot (ASTM D2156
Shell-Bacharach Scale) to minimize soot buildup in the boiler.
Do not disturb established low fire adjustment. Allow the burner to return to low fire position before adjusting
high or intermediate settings.
When conditions covered above are assured, refer to NORMAL OPERATION below.
Combination Gas-Oil Burners
In general, the combination fueled system is to be started first using oil, because, as a fuel, oil has a greater
combustion air requirement than natural gas.
Refer to the Gas Burner or Oil Burner adjustment procedures.
Once the adjustments are set for oil, shut down the burner and restart the adjust the natural gas fuel. DO NOT
READJUST THE AIR DAMPERS. The adjustment is made by balancing the fuel input rate against the existing
flow of combustion air.
When conditions covered above are assured, refer to NORMAL OPERATION below.
Note: SIZE 1 & 2 COMBINATION GAS/OIL UNITS USE A DIRECT COUPLING FROM THE BLOWER MOTOR
TO THE OIL PUMP. WHEN FIRING GAS FOR AN EXTENDED PERIOD OF TIME, THE COUPLING SHOULD BE
MANUALLLY REMOVED AND REPLACED ONLY WHEN FIRING OIL. IF THE COUPLING IS LEFT CONNECTED
TO THE BLOWER MOTOR, ENSURE THAT THERE IS PROPER OIL CIRCULATION AT ALL TIMES TO AVOID
DAMAGE AND SEIZURE OF THE PUMP.
NORMAL OPERATION
Normal operation must be with the MANUAL-AUTO switch selector on AUTO.
In automatic operation, the operating cycle always proceeds sequentially through pre-purge, pilot ignition,
main flame ignition, run and post-purge. The length of purge and ignition trial vary according to the type of
programmer used.
During the run cycle, burner input is regulated to the load demand by the modulating pressure or temperature
control on the boiler. The burner will continue to modulate until the operating pressure or temperature is
reached.
Programmer control operation should be tested when the burner is initially placed into service, when a control
is replaced, and at scheduled intervals in the maintenance program.
SHUTDOWN
When the operating limit control setting is reached or the burner switch is turned OFF, the following sequence
occurs:
1. The fuel valve(s) de-energize and flame extinguishes. The blower motor continues running during post-purge (if so
equipped with post-purge feature).
2. At the end of the post-purge the blower motor is de-energized. The programmer returns to its starting position and
stops. Unit is ready to restart.
Abnormal shutdown might result from motor overload flame outage, low water, current or fuel supply
interruption, combustion or atomizing air pressure below minimum level, tripped circuit breakers, blown fuses,
or other interlock devices. Check for cause and correct before restarting burner.
Summary of Contents for FLX 1000
Page 12: ...Chapter 1 General Description 1 6 750 177...
Page 68: ...Chapter 2 Profire V Burner 2 56 750 177...
Page 90: ...Chapter 4 Sequence of Operation 4 10 750 177...
Page 104: ...Chapter 5 Adjustment Procedures 5 14 750 177...
Page 110: ...Chapter 6 Troubleshooting 6 6 750 177...
Page 122: ...8 2 750 177 Figure 8 1 Typical Hot Water Flextube Casing...
Page 124: ...8 4 750 177 Figure 8 2 Typical Low Pressure Steam Flextube Casing...
Page 126: ...8 6 750 177 Figure 8 3 Typical High Pressure Steam Flextube Casing...
Page 128: ...Parts Chapter 8 8 8 750 177 Steam Pressure Controls...
Page 129: ...Chapter 8 Parts 750 177 8 9 Water Level Controls...
Page 130: ...Parts Chapter 8 8 10 750 177 Water Level Controls continued...
Page 131: ...Chapter 8 Parts 750 177 8 11 Water Column Main and Aux 15 Steam...
Page 132: ...Parts Chapter 8 8 12 750 177 Water Column Main and Aux 150 Steam...
Page 133: ...Chapter 8 Parts 750 177 8 13 Safety Valves...
Page 134: ...Parts Chapter 8 8 14 750 177...
Page 135: ......
Page 136: ...e mail info cleaverbrooks com Web Address http www cleaverbrooks com...