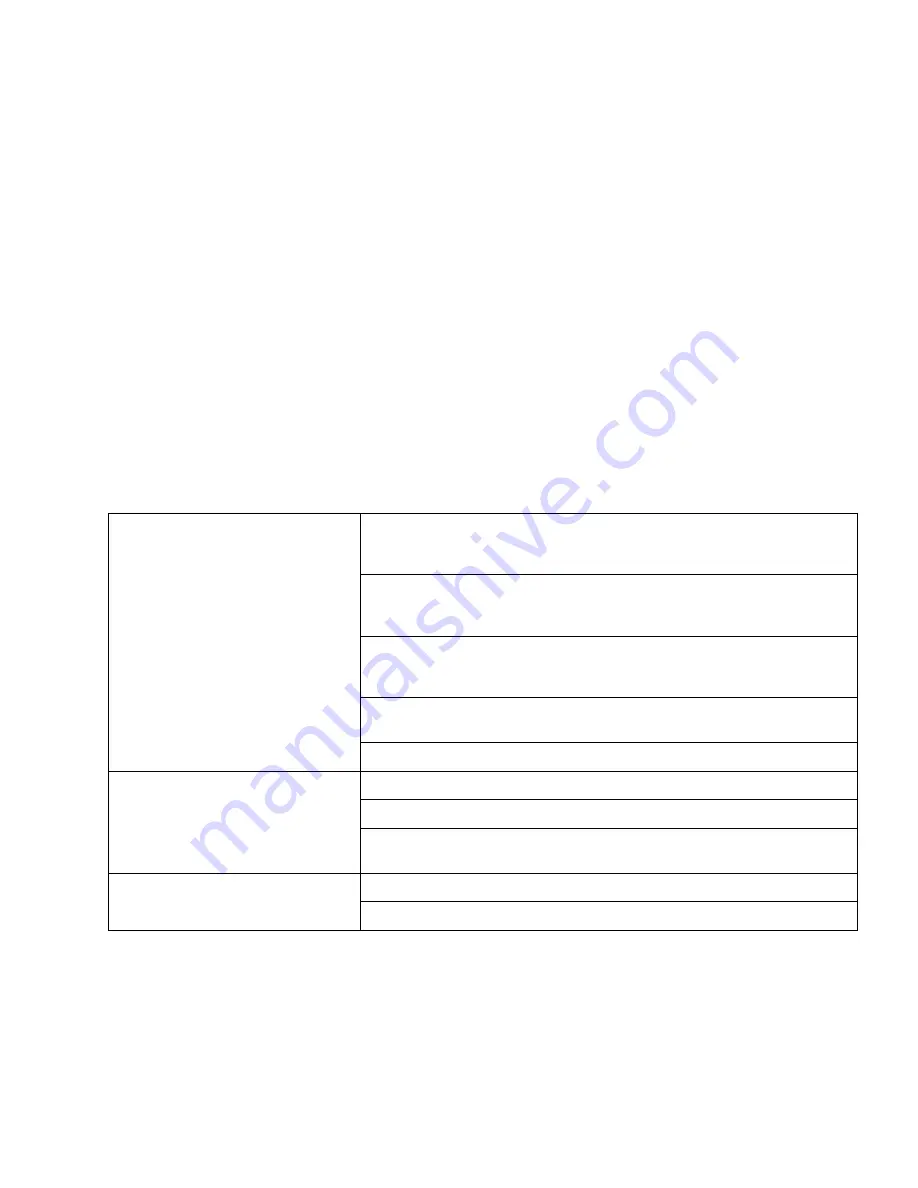
Profire V Burner
Chapter 2
750-177
2-3
and fuel metering valves increase the firing rate. Optional “CAM” trim provides additional precision to the air/
fuel mix with the use of several discrete set point adjustments across the modulation range. Further
combustion efficiency may be achieved with the use of parallel positioning controls which use multiple
directly-coupled actuators (linkeageless) to position the air damper, fuel metering valves and, if applicable,
flue gas recirculation (FGR) across the modulation range.
COMBUSTION AIR HANDLING SYSTEM
1. MOTOR AND BLOWER
The impeller is directly driven by the motor at 3450 rpm.
2. AIR VOLUME REGULATOR
Air dampers are located in the air inlet housing and mechanically linked to the modulating motor.
3. COMBUSTION AIR PROVING SWITCH
A pressure sensitive, differential switch actuated by air pressure created by the blower fan. Contacts close to
prove combustion air flow.
4. DIFFUSER
Contained by the burner’s firing head, an air flow diffuser shapes combustion air flow and improves flame
stability.
When determining boiler room air requirements, the size of the room, air flow, and velocity of air must be
reviewed as follows (fpm = feet per minute; cfm = cubic feet per minute):
Size (area) and location of air supply
openings in boiler room:
Two (2) permanent air supply openings in the outer walls of the boiler room are rec-
ommended. Locate one (1) at each end of the boiler room, preferably 7 foot or
lower. This allows air to sweep the length of the boiler.
A boiler room vent fan is not recommended. Under certain conditions, these fans
can cause a light vacuum and “steal” combustion air from the burner resulting in
unsatisfactory combustion performance.
A vent fan in the boiler room is not recommended, as it could create a light vacuum
under certain conditions and cause variations in the volume of combustion air. This
can result in unsatisfactory burner performance.
Under no condition should the total area of the air supply openings be less than
(1)square foot.
Size the openings by using the formula: Area (sq-ft) = cfm/fpm
Amount of air required (cfm):
Combustion Air = Rated bhp x 8 cfm/bhp.
Ventilation Air = Maximum bhp x 2 cfm/bhp.
Total recommended air = 10 cfm/bhp – up to 1000 feet elevation. Add 3% more
per 1000 feet of added elevation.
Acceptable air velocity in Boiler Room
(fpm):
From floor to (7) foot height – 250 fpm
Above (7) foot height – 500 fpm
Example: Determine the area of the boiler room air supply openings for one (1) 300 hp boiler at 800 feet
altitude. The air openings are to be 5 feet above floor level.
1.Air required: 300 x 10 = 3000 cfm
2.Air velocity: Up to 7 feet - 250 fpm
3.Area required: Area = cfm = 3000/250 = 12 sq-ft total
4.Area/Opening: 12/2 = 6 sq-ft/opening (2 required)
A
B
Summary of Contents for FLX 1000
Page 12: ...Chapter 1 General Description 1 6 750 177...
Page 68: ...Chapter 2 Profire V Burner 2 56 750 177...
Page 90: ...Chapter 4 Sequence of Operation 4 10 750 177...
Page 104: ...Chapter 5 Adjustment Procedures 5 14 750 177...
Page 110: ...Chapter 6 Troubleshooting 6 6 750 177...
Page 122: ...8 2 750 177 Figure 8 1 Typical Hot Water Flextube Casing...
Page 124: ...8 4 750 177 Figure 8 2 Typical Low Pressure Steam Flextube Casing...
Page 126: ...8 6 750 177 Figure 8 3 Typical High Pressure Steam Flextube Casing...
Page 128: ...Parts Chapter 8 8 8 750 177 Steam Pressure Controls...
Page 129: ...Chapter 8 Parts 750 177 8 9 Water Level Controls...
Page 130: ...Parts Chapter 8 8 10 750 177 Water Level Controls continued...
Page 131: ...Chapter 8 Parts 750 177 8 11 Water Column Main and Aux 15 Steam...
Page 132: ...Parts Chapter 8 8 12 750 177 Water Column Main and Aux 150 Steam...
Page 133: ...Chapter 8 Parts 750 177 8 13 Safety Valves...
Page 134: ...Parts Chapter 8 8 14 750 177...
Page 135: ......
Page 136: ...e mail info cleaverbrooks com Web Address http www cleaverbrooks com...