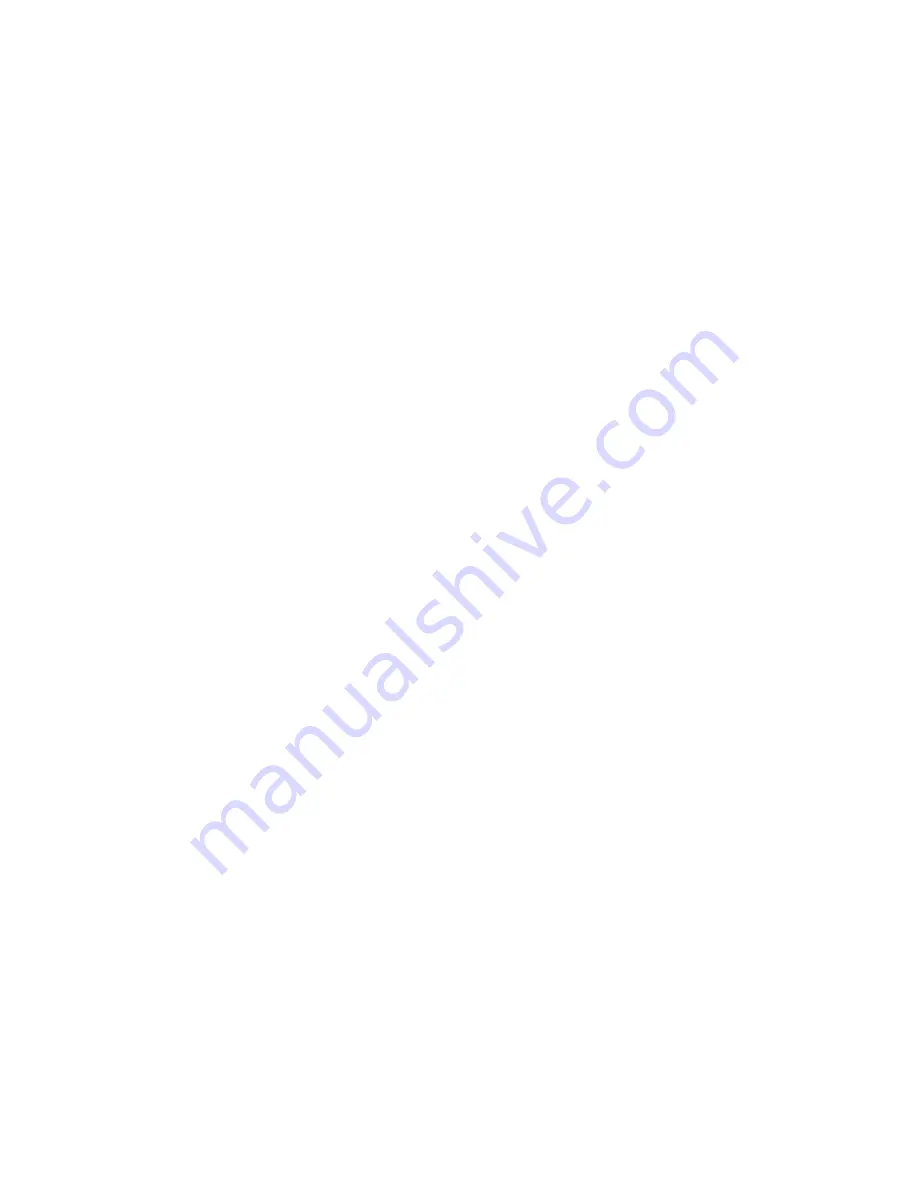
Sequence of Operation
Chapter 4
750-177
4-3
To comply with requirements of insurance underwriters such as Factory Mutual (FM), Industrial Risk Insurers (IRI) or
others, additional interlock devices may be used in addition to the circuits mentioned in Section B.
High Fire Proving Circuit
• High fire switch (HFS)
Running Interlock and Limit Circuit
• Low oil pressure switch (LOPS)
• High oil pressure switch (HOPS)
• Auxiliary low-water cutoff (ALWCO)
C. SEQUENCE OF OPERATION - OIL OR GAS
On a combination fuel unit, the gas/oil switch must be set for the proper fuel.
The following sequence occurs with power present at the program relay (PR) input terminals and with all other operating
conditions satisfied.
Pre-Purge Cycle -
When the burner switch (BS) is turned “on,” and controls wired in the “limit” and “fuel valve interlock”
circuits are closed and no flame signal is present, the “blower motor start circuit” is powered energizing the blower motor
starter (BMS). The load demand light (LDL) turns on.
At the same time, the program relay signals the modulating damper motor (MDM) to open the air damper. The damper
begins to open and drives to its full open or high fire position. Opening the damper motor allows a flow of purging air
through the boiler prior to the ignition cycle.
On certain boilers the circuitry will include a high fire switch (HFS). The purpose of the switch is to prove that the
modulating damper motor (MDM) has driven the damper to the open position during the pre-purge cycle. In this instance,
the “high fire proving circuit” is utilized.
The controls wired into the “running interlock circuit” must be closed within 10 seconds after the start sequence. In the
event any of the controls are not closed at this time, or if they subsequently open, the program relay will go into a safety
shutdown.
At the completion of the high fire purge period, the program relay signals the modulating damper motor (MDM) to drive
the air damper to its low fire position.
To assure that the system is in low fire position prior to ignition, the low fire switch (LFS) must be closed to complete the
“low fire proving circuit.” The sequence will stop and hold until the modulating damper motor (MDM) has returned to
the low fire position and the contacts of the low fire switch (LFS) are closed. Once the low fire switch is closed, the
sequence is allowed to continue.
Note: The ignition trial cannot be started if flame or a flame simulating condition is sensed during the pre-
purge period. A safety shutdown will occur if flame is sensed at this time.
Ignition Cycle -
The ignition transformer (IT) and gas pilot valve (GPV) are energized from the appropriate pilot ignition
terminal.
Note: An oil-fired burner may be equipped with a direct spark rather than a gas pilot. The ignition sequence
of both is identical.
The pilot flame must be established and proven by the flame detector (FD) within a 10 second period in order for the
ignition cycle to continue. If for any reason this does not happen, the system will shut down and safety lockout will occur.
Note: Depending upon the requirements of the regulatory body, insurer or fuel being burned, either the 10 or
15 second pilot ignition terminal may be used. Both provide the same function but differ in time interval
allowed for proving main flame ignition. Refer to the boiler wiring diagram.
A
B
Summary of Contents for FLX 1000
Page 12: ...Chapter 1 General Description 1 6 750 177...
Page 68: ...Chapter 2 Profire V Burner 2 56 750 177...
Page 90: ...Chapter 4 Sequence of Operation 4 10 750 177...
Page 104: ...Chapter 5 Adjustment Procedures 5 14 750 177...
Page 110: ...Chapter 6 Troubleshooting 6 6 750 177...
Page 122: ...8 2 750 177 Figure 8 1 Typical Hot Water Flextube Casing...
Page 124: ...8 4 750 177 Figure 8 2 Typical Low Pressure Steam Flextube Casing...
Page 126: ...8 6 750 177 Figure 8 3 Typical High Pressure Steam Flextube Casing...
Page 128: ...Parts Chapter 8 8 8 750 177 Steam Pressure Controls...
Page 129: ...Chapter 8 Parts 750 177 8 9 Water Level Controls...
Page 130: ...Parts Chapter 8 8 10 750 177 Water Level Controls continued...
Page 131: ...Chapter 8 Parts 750 177 8 11 Water Column Main and Aux 15 Steam...
Page 132: ...Parts Chapter 8 8 12 750 177 Water Column Main and Aux 150 Steam...
Page 133: ...Chapter 8 Parts 750 177 8 13 Safety Valves...
Page 134: ...Parts Chapter 8 8 14 750 177...
Page 135: ......
Page 136: ...e mail info cleaverbrooks com Web Address http www cleaverbrooks com...