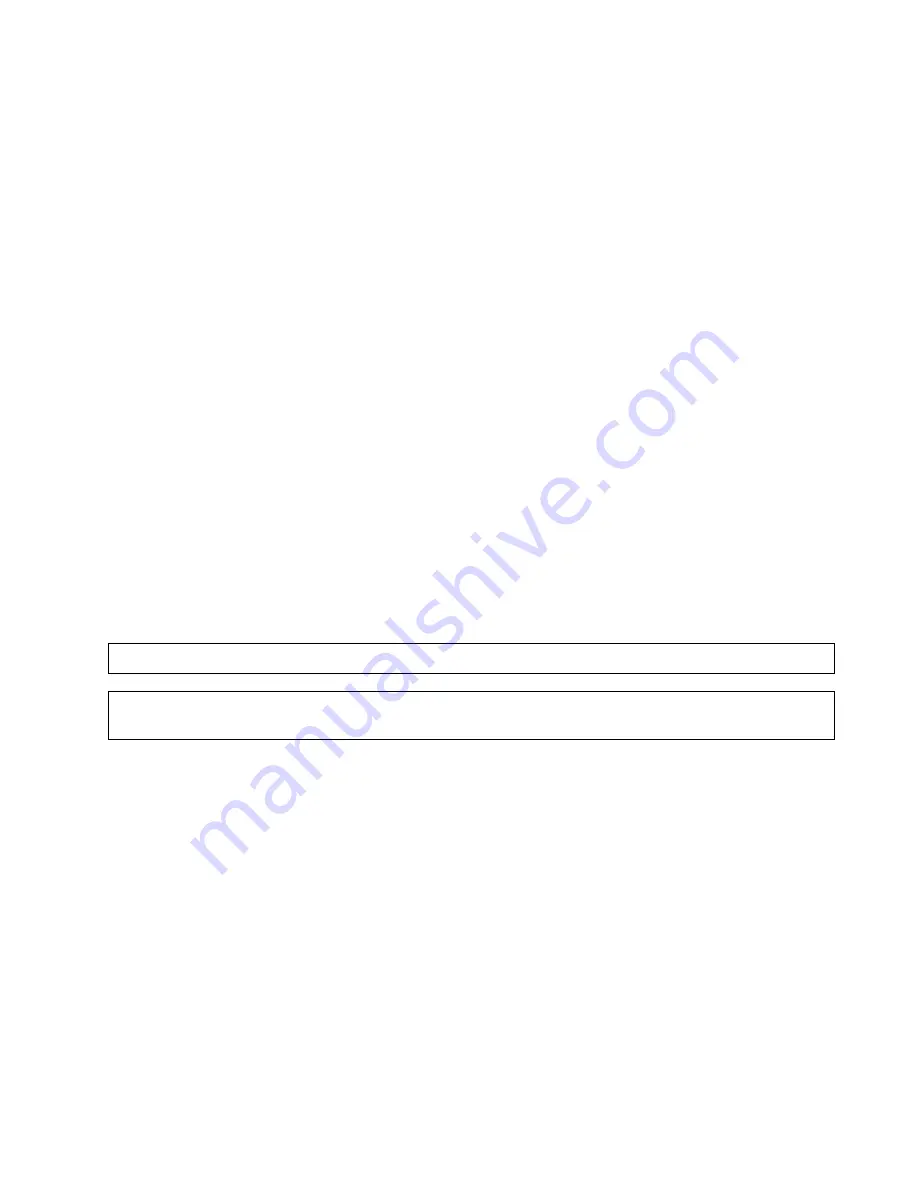
Profire V Burner
Chapter 2
750-177
2-39
than No. 1 smoke (Bacharach).
5. Operate the boiler at low-fire until it is up to operating pressure (steam) or temperature (hot water). Then increase
the fuel input to the boiler by turning the manual flame control potentiometer towards “OPEN” in small increments.
This will cause the metering valve to close, resulting in an increase in the oil pressure feeing the burner nozzle.
6. At each point, allow the burner to operate for a few minutes before recording the O2, CO, smoke, and pressure
readings. Observe that your O2 and CO levels remain within an acceptable limit. Adjust the oil pressure as neces-
sary to correct this situation. For burners with the cam trim option, adjust the cam screws throughout the range to
obtain correct O2 and CO levels. Continue to do this until the burner reaches high-fire (the potentiometer is at the
“OPEN” position).
7. Adjust the high-fire fuel input to match maximum oil pressure. At high-fire, the metering valve should be pressures.
high-fire is typically 3.5% to 4.5% O2 with less than No. 1 smoke (Bacharach). Adjust the high-fire excess air rate
using the high-fire shutter adjustment.
8. Modulate the burner to low-fire. Verify the readings once again. The burner should be adjusted to provide correct
fuel flow at a constant rate, at the low-fire and high-fire position as indicated on the burner data plate.
9. Tighten all linkages and marked settings. Complete the Startup Report.
10. Turn the “MANUAL-AUTO” switch to “AUTO”. The burner will now modulate according to the load demand to the
boiler.
J. Combination Gas-Oil System
In general, the combination fueled system is to be started first using oil, because as a fuel, oil has a
greatercombustion air requirement than natural gas. After being completely adjusted for oil combustion, the
burneris restarted and adjusted using natural gas as fuel. Combustion adjustment of the combination burner
fornatural gas involves balancing the input rate only against the existing flow of combustion air, as
establishedinitially for oil.
NOTE: Do not readjust the air shutter when tuning the combination burner for combustion of natural gas.
NOTE: For burners equipped with a Siemens modulation motor, fuel-air adjustments for each fuel are inde-
pendent of each other. Refer to the Siemens modulating motor product literature for proper adjustment.
LOW-HIGH-OFF/LOW COMBINATION GAS-OIL BURNER ADJUSTMENT
1. Turn the fuel selector switch to the “OIL” position.
2. Turn the burner switch to the “ON” position.
3. Proceed with startup and adjustments using the same procedures as explained above for oil burners.
4. After the system has been completely adjusted for oil firing, place the burner switch to “OFF” and position the fuel
selector switch to “GAS”.
5. Proceed with startup and adjustments using the same procedures as explained above for gas burners. Do not alter
the air settings set for oil. Correct the O2 levels by adjusting the butterfly valve for models V35-55, and the regula-
tors low and high pressures for models V13-34.
Summary of Contents for FLX 1000
Page 12: ...Chapter 1 General Description 1 6 750 177...
Page 68: ...Chapter 2 Profire V Burner 2 56 750 177...
Page 90: ...Chapter 4 Sequence of Operation 4 10 750 177...
Page 104: ...Chapter 5 Adjustment Procedures 5 14 750 177...
Page 110: ...Chapter 6 Troubleshooting 6 6 750 177...
Page 122: ...8 2 750 177 Figure 8 1 Typical Hot Water Flextube Casing...
Page 124: ...8 4 750 177 Figure 8 2 Typical Low Pressure Steam Flextube Casing...
Page 126: ...8 6 750 177 Figure 8 3 Typical High Pressure Steam Flextube Casing...
Page 128: ...Parts Chapter 8 8 8 750 177 Steam Pressure Controls...
Page 129: ...Chapter 8 Parts 750 177 8 9 Water Level Controls...
Page 130: ...Parts Chapter 8 8 10 750 177 Water Level Controls continued...
Page 131: ...Chapter 8 Parts 750 177 8 11 Water Column Main and Aux 15 Steam...
Page 132: ...Parts Chapter 8 8 12 750 177 Water Column Main and Aux 150 Steam...
Page 133: ...Chapter 8 Parts 750 177 8 13 Safety Valves...
Page 134: ...Parts Chapter 8 8 14 750 177...
Page 135: ......
Page 136: ...e mail info cleaverbrooks com Web Address http www cleaverbrooks com...