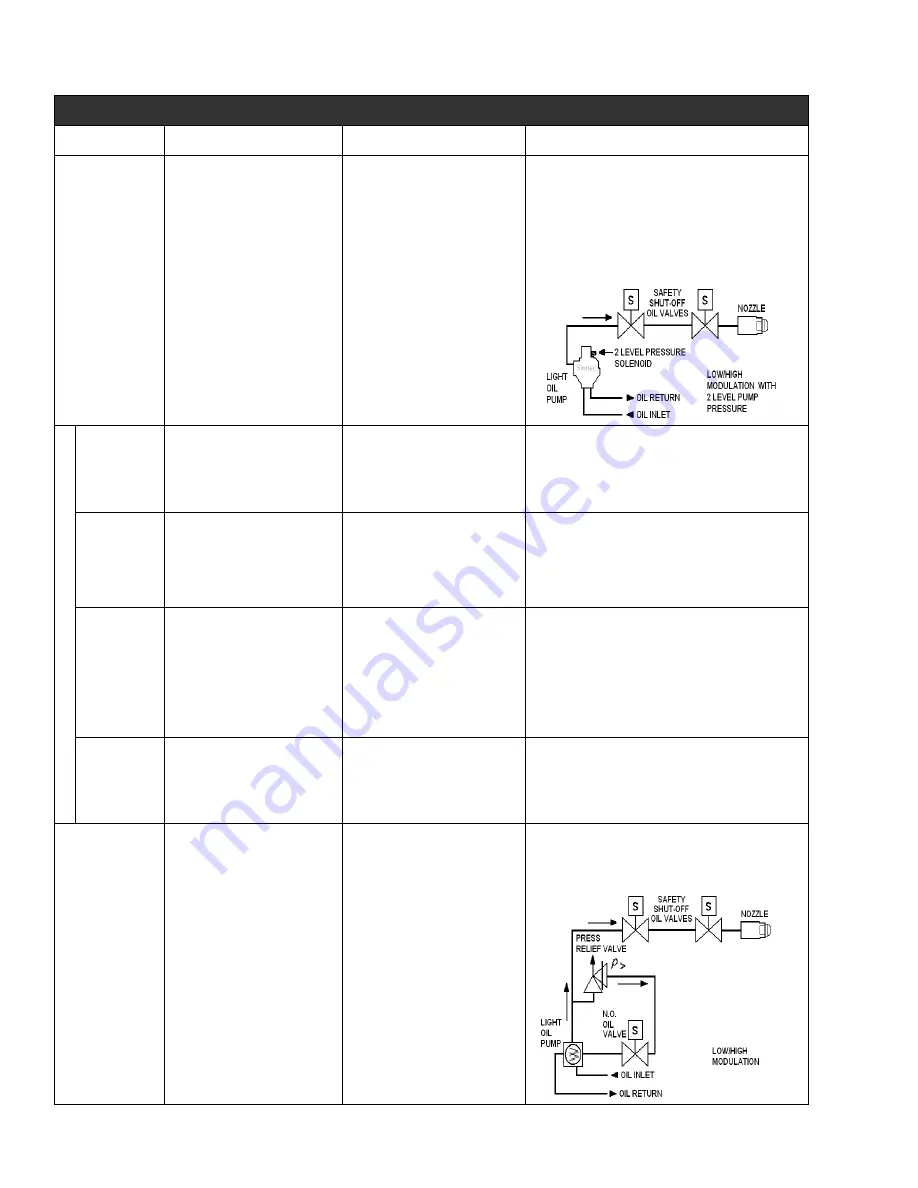
LOW-HIGH-LOW MOD - OPEN DAMPER PURGE
Combustion Air
Gas
Oil
COMPONENTS
DESCRIPTION
A two blade damper is
controlled by a two position,
spring return actuator with
mechanical linkage. Power to
drive the actuator is routed
through a low/auto switch and a
remote located modulating
control. The actuator also
contains a limit switch which is
used to actuate the second
stage of the oil supply system.
(see oil at right) A second
external switch ensures the
damper has returned to the low
fire position before ignition is
initiated.
Safety shut off valve(s) are
provided to initiate the flow of
gas. The primary is a diaphragm
or motorized type valve which
have delayed opening rates to
prevent an "in rush" of gas. A
butterfly type gas metering valve
is linked directly to the damper
actuator and provides gas flow
metering during the drive to the
high position. A manually
adjusted gas regulator limits
maximum firing rate.
Pressure Atomization:
Two solenoid type safety
shut off oil valves initiate the flow of oil from the high
pressure pump to the nozzle. The oil pump has a
built in solenoid controlled two level pressure
regulating system. Low and high flow rates are set
on the pump based on pressure and the nozzle's
flow rating.
Operating Sequence
PRE-PURGE
From its closed position the
damper is driven open by the
flame safeguard control where
it remains for the duration of the
pre-purge cycle.
Valves are closed.
The pump is operational but the valves are closed.
Oil is flowing through an internal relief valve and
returning to the supply system.
STARTUP,
IGNITION
Damper returns to the low fire
position which is proven
through the external switch.
The burner is now ready for
startup.
Valves open. To prevent a surge
the primary gas valve opens at a
slowed rate. Gas flow to the
manifold is metered based on
the butterfly valves low fire
setting.
Safety shut off valves open allowing oil to flow from
pump to nozzle. Oil pressure at the nozzle is based
on the pump's low pressure setting. Excess oil is
flowing through an internal relief valve and returning
to the supply system.
RUN,
MODULATE
Damper is driven open in 30
seconds by the two position
actuator. Low-High-Low
burners will modulate from low
to high rate positions based on
the signal from the modulating
control and the selection of the
low/auto switch.
The gas valves remain in their
open position. The actuator
begins its travel to the high fire
position opening the gas
metering valve. The burner will
modulate from low to high as
described in the combustion air
column.
The safety shut-off oil valves remain open. The
pump's solenoid is energized by the aux switch
within the damper actuator as it opens the air
damper. Oil pressure is then increased based the
pump’s high pressure setting. The actuator begins
its travel to the high fire position opening the gas
metering valve. The burner will modulate from low
to high as described in the combustion air column.
SHUT DOWN,
POST-PURGE
Damper returns to its start
position based on the 25
second closure speed of the
mechanical actuator.
On shut down all gas valves
close within 1 second. The
butterfly valve closes in 25
seconds with the two position
actuator.
All valves immediately return to their startup or de-
energized position. The oil pump is operating with
post-purge, but oil is flowing through an internal
relief valve and returning to the supply system.
VARIATIONS
None
None
For pumps without the internal dual pressure
solenoid an external pressure relief valve and
normally open solenoid valve are
used.
Chapter 2
Profire V Burner
2-16
750-177
Summary of Contents for FLX 1000
Page 12: ...Chapter 1 General Description 1 6 750 177...
Page 68: ...Chapter 2 Profire V Burner 2 56 750 177...
Page 90: ...Chapter 4 Sequence of Operation 4 10 750 177...
Page 104: ...Chapter 5 Adjustment Procedures 5 14 750 177...
Page 110: ...Chapter 6 Troubleshooting 6 6 750 177...
Page 122: ...8 2 750 177 Figure 8 1 Typical Hot Water Flextube Casing...
Page 124: ...8 4 750 177 Figure 8 2 Typical Low Pressure Steam Flextube Casing...
Page 126: ...8 6 750 177 Figure 8 3 Typical High Pressure Steam Flextube Casing...
Page 128: ...Parts Chapter 8 8 8 750 177 Steam Pressure Controls...
Page 129: ...Chapter 8 Parts 750 177 8 9 Water Level Controls...
Page 130: ...Parts Chapter 8 8 10 750 177 Water Level Controls continued...
Page 131: ...Chapter 8 Parts 750 177 8 11 Water Column Main and Aux 15 Steam...
Page 132: ...Parts Chapter 8 8 12 750 177 Water Column Main and Aux 150 Steam...
Page 133: ...Chapter 8 Parts 750 177 8 13 Safety Valves...
Page 134: ...Parts Chapter 8 8 14 750 177...
Page 135: ......
Page 136: ...e mail info cleaverbrooks com Web Address http www cleaverbrooks com...