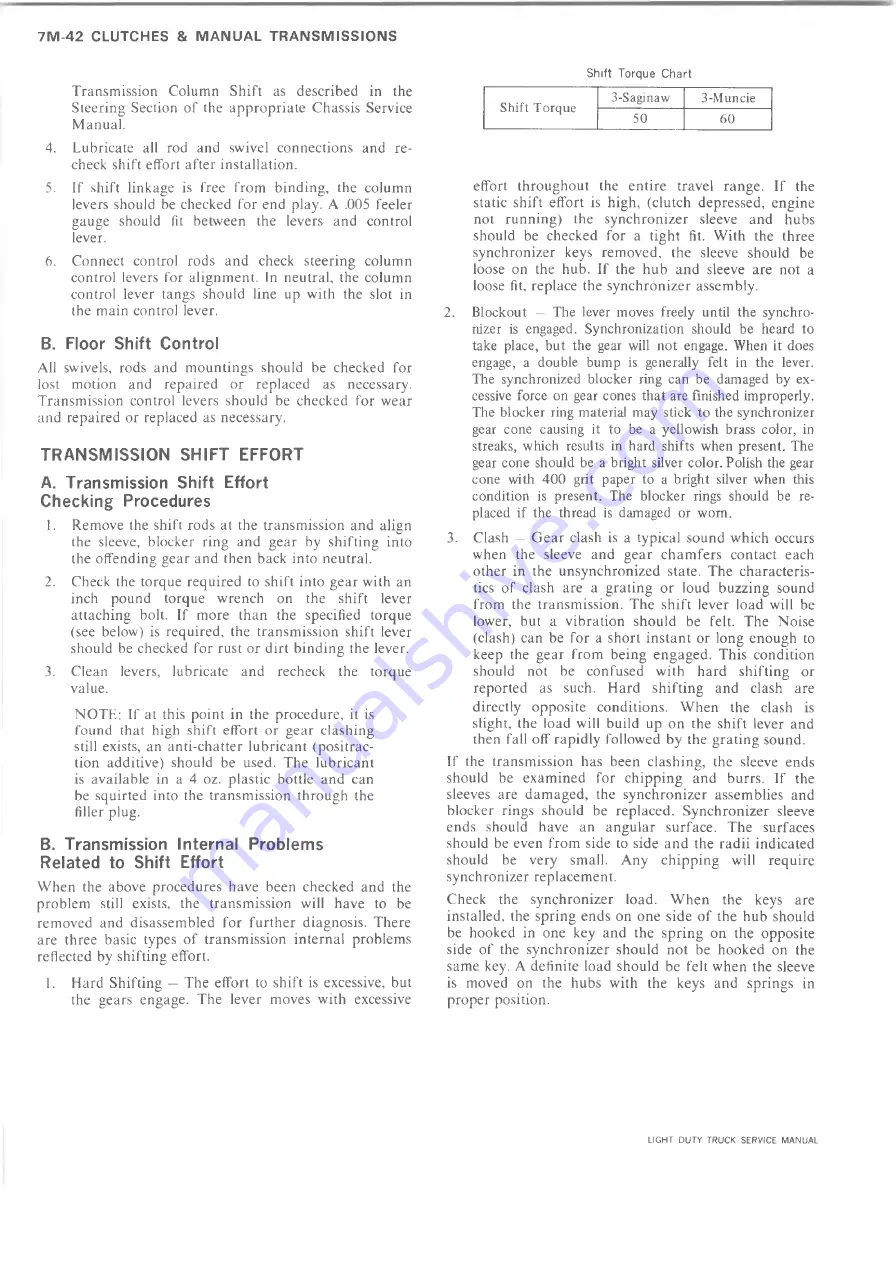
7 M - 4 2 C L U T C H E S & M A N U A L T R A N S M IS S IO N S
Shift Torque Chart
Transmission Column Shift as described in the
Steering Section of the appropriate Chassis Service
Manual.
4. Lubricate all rod and swivel connections and re
check shift effort after installation.
5. If shift linkage is free from binding, the column
levers should be checked for end play. A .005 feeler
gauge should fit between the levers and control
lever.
6. Connect control rods and check steering column
control levers for alignment. In neutral, the column
control lever tangs should line up with the slot in
the main control lever.
B. Floor Shift Control
All swivels, rods and mountings should be checked for
lost motion and repaired or replaced as necessary.
Transmission control levers should be checked for wear
and repaired or replaced as necessary.
TRANSMISSION SHIFT EFFORT
A. Transmission Shift Effort
Checking Procedures
1. Remove the shift rods at the transmission and align
the sleeve, blocker ring and gear by shifting into
the offending gear and then back into neutral.
2. Check the torque required to shift into gear with an
inch pound torque wrench on the shift lever
attaching bolt. If more than the specified torque
(see below) is required, the transmission shift lever
should be checked for rust or dirt binding the lever.
3. Clean levers, lubricate and recheck the torque
value.
NOTE: If at this point in the procedure, it is
found that high shift effort or gear clashing
still exists, an anti-chatter lubricant (positrac-
tion additive) should be used. The lubricant
is available in a 4 oz. plastic bottle and can
be squirted into the transmission through the
filler plug.
B. Transmission Internal Problems
Related to Shift Effort
When the above procedures have been checked and the
problem still exists, the transmission will have to be
removed and disassembled for further diagnosis. There
are three basic types of transmission internal problems
reflected by shifting effort.
1. Hard Shifting — The effort to shift is excessive, but
the gears engage. The lever moves with excessive
Shift Torque
3-Saginaw
3-Muncie
50
60
effort throughout the entire travel range. If the
static shift effort is high, (clutch depressed, engine
not running) the synchronizer sleeve and hubs
should be checked for a tight fit. With the three
synchronizer keys removed, the sleeve should be
loose on the hub. If the hub and sleeve are not a
loose fit, replace the synchronizer assembly.
2. Blockout — The lever moves freely until the synchro
nizer is engaged. Synchronization should be heard to
take place, but the gear will not engage. When it does
engage, a double bump is generally felt in the lever.
The synchronized blocker ring can be damaged by ex
cessive force on gear cones that are finished improperly.
The blocker ring material may stick to the synchronizer
gear cone causing it to be a yellowish brass color, in
streaks, which results in hard shifts when present. The
gear cone should be a bright silver color. Polish the gear
cone with 400 grit paper to a bright silver when this
condition is present. The blocker rings should be re
placed if the thread is damaged or worn.
3. Clash — Gear clash is a typical sound which occurs
when the sleeve and gear chamfers contact each
other in the unsynchronized state. The characteris
tics of clash are a grating or loud buzzing sound
from the transmission. The shift lever load will be
lower, but a vibration should be felt. The Noise
(clash) can be for a short instant or long enough to
keep the gear from being engaged. This condition
should not be confused with hard shifting or
reported as such. Hard shifting and clash are
directly opposite conditions. When the clash is
slight, the load will build up on the shift lever and
then fall off rapidly followed by the grating sound.
If the transmission has been clashing, the sleeve ends
should be examined for chipping and burrs. If the
sleeves are damaged, the synchronizer assemblies and
blocker rings should be replaced. Synchronizer sleeve
ends should have an angular surface. The surfaces
should be even from side to side and the radii indicated
should be very small. Any chipping will require
synchronizer replacement.
Check the synchronizer load. When the keys are
installed, the spring ends on one side of the hub should
be hooked in one key and the spring on the opposite
side of the synchronizer should not be hooked on the
same key. A definite load should be felt when the sleeve
is moved on the hubs with the keys and springs in
proper position.
LIGHT DUTY TRUCK SERVICE MANUAL
Summary of Contents for Light Duty Truck 1973
Page 1: ......
Page 4: ......
Page 6: ......
Page 53: ...HEATER AND AIR CONDITIONING 1A 27 LIGHT DUTY TRUCK SERVICE MANUAL...
Page 115: ...LIGHT DUTY TRUCK SERVICE M A N U A L HEATER AND AIR CONDITIONING 1A 89...
Page 123: ...BODY 1B 3 Fig 6 Typical 06 Van LIGHT DUTY TRUCK SERVICE MANUAL...
Page 149: ...BODY 1B 29 Fig 84 Body Mounting 06 Fig 85 Body Mounting 14 LIGHT DUTY TRUCK SERVICE MANUAL...
Page 171: ...LIGHT DUTY TRUCK SERVICE M A N U A L Fig 2 Frame Horizontal Checking Typical FRAME 2 3...
Page 173: ...LIGHT DUTY TRUCK SERVICE M A N U A L Fig 4 10 30 Series Truck Frame FRAME 2 5...
Page 174: ...2 6 FRAME LIGHT DUTY TRUCK SERVICE MANUAL Fig 5 Underbody Reference Points G Van...
Page 185: ...FRONT SUSPENSION 3 11 Fig 16 Toe out on Turns LIGHT DUTY TRUCK SERVICE MANUAL...
Page 224: ......
Page 266: ......
Page 351: ...ENGINE 6 15 Fig ID Sectional View of Eight Cylinder Engine LIGHT DUTY TRUCK SERVICE MANUAL...
Page 375: ...EN G IN E 6 39 LIGHT DUTY TRUCK SERVICE MANUAL...
Page 376: ...6 4 0 ENGINE LIGHT DUTY TRUCK SERVICE MANUAL...
Page 377: ...ENG IN E 6 41 LIGHT DUTY TRUCK SERVICE MANUAL...
Page 378: ...LIGHT DUTY TRUCK SERVICE MANUAL Fig 37L K Series Engine Front Mount 6 42 ENG INE...
Page 400: ...6 6 4 ENG INE LIGHT DUTY TRUCK SERVICE MANUAL...
Page 401: ...ENG IN E 6 65 LIGHT DUTY TRUCK SERVICE MANUAL...
Page 402: ...6 6 6 ENGINE LIGHT DUTY TRUCK SERVICE MANUAL...
Page 403: ...E NG IN E 6 67 Fig 36V C Series Engine Mounts LIGHT DUTY TRUCK SERVICE MANUAL...
Page 410: ......
Page 423: ...EN G IN E C OOLING 6K 13 Fig 16 Overheating Chart LIGHT DUTY TRUCK SERVICE MANUAL...
Page 424: ...6 K 1 4 ENG INE COOLING Fig 17 Coolant Loss Chart LIGHT DUTY TRUCK SERVICE MANUAL...
Page 456: ...6M 32 ENGINE FUEL Fig K15 Accelerator Controls G Van L 6 LIGHT DUTY TRUCK SERVICE MANUAL...
Page 492: ......
Page 512: ...Fig 18e Vacuum Advance Diagram V8 Engine...
Page 516: ...6 T 2 4 E M IS S IO N CONTROL SYSTEMS LIGHT DUTY TRUCK SERVICE MANUAL...
Page 528: ......
Page 590: ......
Page 593: ...CLUTCHES MANUAL TRANSMISSIONS 7M 3 LIGHT DUTY TRUCK SERVICE MANUAL...
Page 598: ...7M 8 CLUTCHES MANUAL TRANSMISSIONS LIGHT DUTY TRUCK SERVICE MANUAL...
Page 642: ......
Page 654: ......
Page 743: ...FUEL TANKS AND EXHAUST 8 13 LIGHT DUTY TRUCK SERVICE MANUAL...
Page 744: ...8 14 FUEL TANKS AND EXHAUST LIGHT DUTY TRUCK SERVICE MANUAL...
Page 760: ...8 30 FUEL TANKS AND EXHAUST Fig 40 Exhaust Pipe P Models LIGHT DUTY TRUCK SERVICE MANUAL...
Page 761: ...FUEL TANKS AND EXHAUST 8 31 LIGHT DUTY TRUCK SERVICE MANUAL...
Page 763: ...FUEL TANKS AND EXHAUST 8 33 LIGHT DUTY TRUCK SERVICE MANUAL...
Page 766: ......
Page 832: ...LIGHT DUTY TRUCK SERVICE MANUAL Fig 106 Power Steering Pump Mounting Typical 9 66 STEERING...
Page 833: ...PUMP ASSEMBLY STEERING GEAR TYPICAL SMALL V8 TYPICAL LARGE V8 STEERING 9 67...
Page 861: ...STEERING 9 95 Fig 134 Power Steering Pump Leakage LIGHT DUTY TRUCK SERVICE MANUAL...
Page 864: ......
Page 876: ......
Page 886: ...11 10 CHASSIS SHEET METAL LIGHT DUTY TRUCK SERVICE MANUAL...
Page 891: ...ELECTRICAL BODY AND CHASSIS 12 5 LIGHT DUTY TRUCK SERVICE MANUAL...
Page 934: ......
Page 942: ......
Page 970: ......
Page 972: ......
Page 974: ......
Page 976: ...V...
Page 978: ......
Page 979: ......