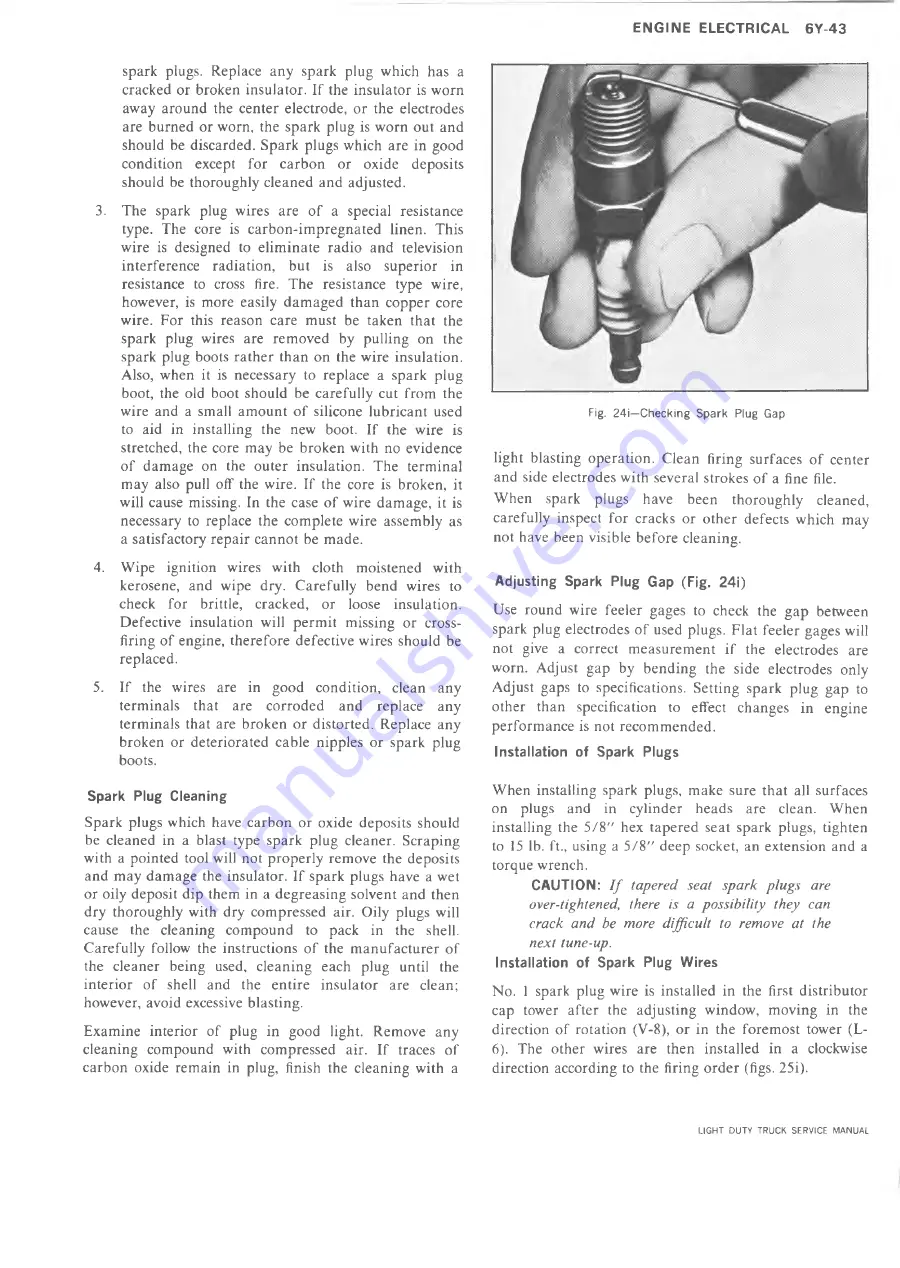
E N G IN E ELECTRICAL
6Y -43
spark plugs. Replace any spark plug which has a
cracked or broken insulator. If the insulator is worn
away around the center electrode, or the electrodes
are burned or worn, the spark plug is worn out and
should be discarded. Spark plugs which are in good
condition except for carbon or oxide deposits
should be thoroughly cleaned and adjusted.
3. The spark plug wires are of a special resistance
type. The core is carbon-impregnated linen. This
wire is designed to eliminate radio and television
interference radiation, but is also superior in
resistance to cross fire. The resistance type wire,
however, is more easily damaged than copper core
wire. For this reason care must be taken that the
spark plug wires are removed by pulling on the
spark plug boots rather than on the wire insulation.
Also, when it is necessary to replace a spark plug
boot, the old boot should be carefully cut from the
wire and a small amount of silicone lubricant used
to aid in installing the new boot. If the wire is
stretched, the core may be broken with no evidence
of damage on the outer insulation. The terminal
may also pull off the wire. If the core is broken, it
will cause missing. In the case of wire damage, it is
necessary to replace the complete wire assembly as
a satisfactory repair cannot be made.
4. Wipe ignition wires with cloth moistened with
kerosene, and wipe dry. Carefully bend wires to
check for brittle, cracked, or loose insulation.
Defective insulation will permit missing or cross
firing of engine, therefore defective wires should be
replaced.
5. If the wires are in good condition, clean any
terminals that are corroded and replace any
terminals that are broken or distorted. Replace any
broken or deteriorated cable nipples or spark plug
boots.
Spark Plug Cleaning
Spark plugs which have carbon or oxide deposits should
be cleaned in a blast type spark plug cleaner. Scraping
with a pointed tool will not properly remove the deposits
and may damage the insulator. If spark plugs have a wet
or oily deposit dip them in a degreasing solvent and then
dry thoroughly with dry compressed air. Oily plugs will
cause the cleaning compound to pack in the shell.
Carefully follow the instructions of the manufacturer of
the cleaner being used, cleaning each plug until the
interior of shell and the entire insulator are clean;
however, avoid excessive blasting.
Examine interior of plug in good light. Remove any
cleaning compound with compressed air. If traces of
carbon oxide remain in plug, finish the cleaning with a
Fig. 2 4 i— C h e c k in g S p a r k Plug G a p
light blasting operation. Clean firing surfaces of center
and side electrodes with several strokes of a fine file.
When spark plugs have been thoroughly cleaned,
carefully inspect for cracks or other defects which may
not have been visible before cleaning.
Adjusting Spark Plug Gap (Fig. 24i)
Use round wire feeler gages to check the gap between
spark plug electrodes of used plugs. Flat feeler gages will
not give a correct measurement if the electrodes are
worn. Adjust gap by bending the side electrodes only
Adjust gaps to specifications. Setting spark plug gap to
other than specification to effect changes in engine
performance is not recommended.
Installation of Spark Plugs
When installing spark plugs, make sure that all surfaces
on plugs and in cylinder heads are clean. When
installing the 5/8" hex tapered seat spark plugs, tighten
to 15 lb. ft., using a 5/8" deep socket, an extension and a
torque wrench.
CAUTION:
I f tapered seat spark plugs are
over-tightened, there is a possibility they can
crack and be more difficult to remove at the
next tune-up.
Installation of Spark Plug Wires
No. 1 spark plug wire is installed in the first distributor
cap tower after the adjusting window, moving in the
direction of rotation (V-8), or in the foremost tower (L-
6). The other wires are then installed in a clockwise
direction according to the firing order (figs. 25i).
LIGHT DUTY TRUCK SERVICE MANUAL
Summary of Contents for Light Duty Truck 1973
Page 1: ......
Page 4: ......
Page 6: ......
Page 53: ...HEATER AND AIR CONDITIONING 1A 27 LIGHT DUTY TRUCK SERVICE MANUAL...
Page 115: ...LIGHT DUTY TRUCK SERVICE M A N U A L HEATER AND AIR CONDITIONING 1A 89...
Page 123: ...BODY 1B 3 Fig 6 Typical 06 Van LIGHT DUTY TRUCK SERVICE MANUAL...
Page 149: ...BODY 1B 29 Fig 84 Body Mounting 06 Fig 85 Body Mounting 14 LIGHT DUTY TRUCK SERVICE MANUAL...
Page 171: ...LIGHT DUTY TRUCK SERVICE M A N U A L Fig 2 Frame Horizontal Checking Typical FRAME 2 3...
Page 173: ...LIGHT DUTY TRUCK SERVICE M A N U A L Fig 4 10 30 Series Truck Frame FRAME 2 5...
Page 174: ...2 6 FRAME LIGHT DUTY TRUCK SERVICE MANUAL Fig 5 Underbody Reference Points G Van...
Page 185: ...FRONT SUSPENSION 3 11 Fig 16 Toe out on Turns LIGHT DUTY TRUCK SERVICE MANUAL...
Page 224: ......
Page 266: ......
Page 351: ...ENGINE 6 15 Fig ID Sectional View of Eight Cylinder Engine LIGHT DUTY TRUCK SERVICE MANUAL...
Page 375: ...EN G IN E 6 39 LIGHT DUTY TRUCK SERVICE MANUAL...
Page 376: ...6 4 0 ENGINE LIGHT DUTY TRUCK SERVICE MANUAL...
Page 377: ...ENG IN E 6 41 LIGHT DUTY TRUCK SERVICE MANUAL...
Page 378: ...LIGHT DUTY TRUCK SERVICE MANUAL Fig 37L K Series Engine Front Mount 6 42 ENG INE...
Page 400: ...6 6 4 ENG INE LIGHT DUTY TRUCK SERVICE MANUAL...
Page 401: ...ENG IN E 6 65 LIGHT DUTY TRUCK SERVICE MANUAL...
Page 402: ...6 6 6 ENGINE LIGHT DUTY TRUCK SERVICE MANUAL...
Page 403: ...E NG IN E 6 67 Fig 36V C Series Engine Mounts LIGHT DUTY TRUCK SERVICE MANUAL...
Page 410: ......
Page 423: ...EN G IN E C OOLING 6K 13 Fig 16 Overheating Chart LIGHT DUTY TRUCK SERVICE MANUAL...
Page 424: ...6 K 1 4 ENG INE COOLING Fig 17 Coolant Loss Chart LIGHT DUTY TRUCK SERVICE MANUAL...
Page 456: ...6M 32 ENGINE FUEL Fig K15 Accelerator Controls G Van L 6 LIGHT DUTY TRUCK SERVICE MANUAL...
Page 492: ......
Page 512: ...Fig 18e Vacuum Advance Diagram V8 Engine...
Page 516: ...6 T 2 4 E M IS S IO N CONTROL SYSTEMS LIGHT DUTY TRUCK SERVICE MANUAL...
Page 528: ......
Page 590: ......
Page 593: ...CLUTCHES MANUAL TRANSMISSIONS 7M 3 LIGHT DUTY TRUCK SERVICE MANUAL...
Page 598: ...7M 8 CLUTCHES MANUAL TRANSMISSIONS LIGHT DUTY TRUCK SERVICE MANUAL...
Page 642: ......
Page 654: ......
Page 743: ...FUEL TANKS AND EXHAUST 8 13 LIGHT DUTY TRUCK SERVICE MANUAL...
Page 744: ...8 14 FUEL TANKS AND EXHAUST LIGHT DUTY TRUCK SERVICE MANUAL...
Page 760: ...8 30 FUEL TANKS AND EXHAUST Fig 40 Exhaust Pipe P Models LIGHT DUTY TRUCK SERVICE MANUAL...
Page 761: ...FUEL TANKS AND EXHAUST 8 31 LIGHT DUTY TRUCK SERVICE MANUAL...
Page 763: ...FUEL TANKS AND EXHAUST 8 33 LIGHT DUTY TRUCK SERVICE MANUAL...
Page 766: ......
Page 832: ...LIGHT DUTY TRUCK SERVICE MANUAL Fig 106 Power Steering Pump Mounting Typical 9 66 STEERING...
Page 833: ...PUMP ASSEMBLY STEERING GEAR TYPICAL SMALL V8 TYPICAL LARGE V8 STEERING 9 67...
Page 861: ...STEERING 9 95 Fig 134 Power Steering Pump Leakage LIGHT DUTY TRUCK SERVICE MANUAL...
Page 864: ......
Page 876: ......
Page 886: ...11 10 CHASSIS SHEET METAL LIGHT DUTY TRUCK SERVICE MANUAL...
Page 891: ...ELECTRICAL BODY AND CHASSIS 12 5 LIGHT DUTY TRUCK SERVICE MANUAL...
Page 934: ......
Page 942: ......
Page 970: ......
Page 972: ......
Page 974: ......
Page 976: ...V...
Page 978: ......
Page 979: ......