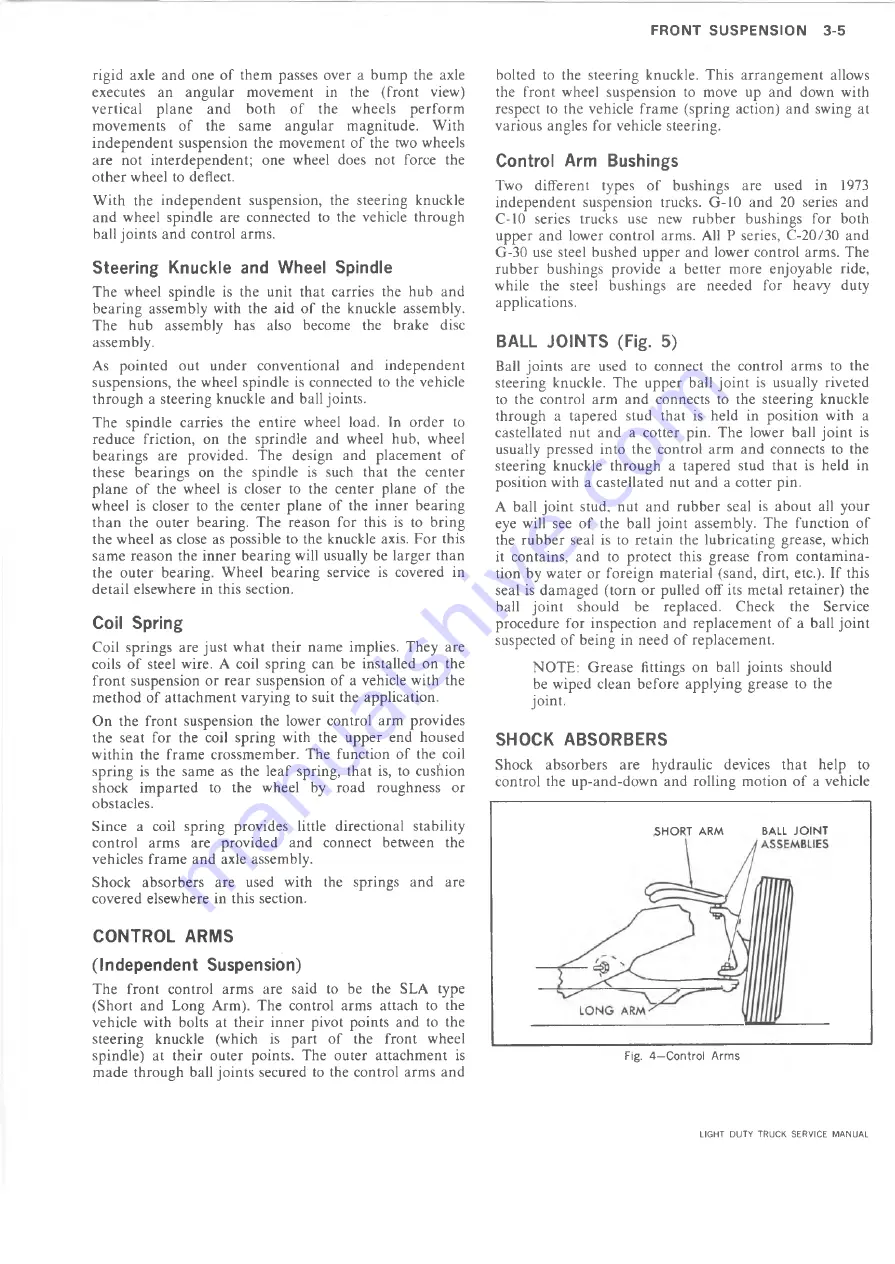
FRO NT S U S P E N S IO N
3-5
rigid axle and one of them passes over a bump the axle
executes an angular movement in the (front view)
vertical plane and both of the wheels perform
movements of the same angular magnitude. With
independent suspension the movement of the two wheels
are not interdependent; one wheel does not force the
other wheel to deflect.
With the independent suspension, the steering knuckle
and wheel spindle are connected to the vehicle through
ball joints and control arms.
Steering Knuckle and Wheel Spindle
The wheel spindle is the unit that carries the hub and
bearing assembly with the aid of the knuckle assembly.
The hub assembly has also become the brake disc
assembly.
As pointed out under conventional and independent
suspensions, the wheel spindle is connected to the vehicle
through a steering knuckle and ball joints.
The spindle carries the entire wheel load. In order to
reduce friction, on the sprindle and wheel hub, wheel
bearings are provided. The design and placement of
these bearings on the spindle is such that the center
plane of the wheel is closer to the center plane of the
wheel is closer to the center plane of the inner bearing
than the outer bearing. The reason for this is to bring
the wheel as close as possible to the knuckle axis. For this
same reason the inner bearing will usually be larger than
the outer bearing. Wheel bearing service is covered in
detail elsewhere in this section.
Coil Spring
Coil springs are just what their name implies. They are
coils of steel wire. A coil spring can be installed on the
front suspension or rear suspension of a vehicle with the
method of attachment varying to suit the application.
On the front suspension the lower control arm provides
the seat for the coil spring with the upper end housed
within the frame crossmember. The function of the coil
spring is the same as the leaf spring, that is, to cushion
shock imparted to the wheel by road roughness or
obstacles.
Since a coil spring provides little directional stability
control arms are provided and connect between the
vehicles frame and axle assembly.
Shock absorbers are used with the springs and are
covered elsewhere in this section.
CONTROL ARMS
(Independent Suspension)
The front control arms are said to be the SLA type
(Short and Long Arm). The control arms attach to the
vehicle with bolts at their inner pivot points and to the
steering knuckle (which is part of the front wheel
spindle) at their outer points. The outer attachment is
made through ball joints secured to the control arms and
bolted to the steering knuckle. This arrangement allows
the front wheel suspension to move up and down with
respect to the vehicle frame (spring action) and swing at
various angles for vehicle steering.
Control Arm Bushings
Two different types of bushings are used in 1973
independent suspension trucks. G-10 and 20 series and
C-10 series trucks use new rubber bushings for both
upper and lower control arms. All P series, C-20/30 and
G-30 use steel bushed upper and lower control arms. The
rubber bushings provide a better more enjoyable ride,
while the steel bushings are needed for heavy duty
applications.
BALL JOINTS (Fig. 5)
Ball joints are used to connect the control arms to the
steering knuckle. The upper ball joint is usually riveted
to the control arm and connects to the steering knuckle
through a tapered stud that is held in position with a
castellated nut and a cotter pin. The lower ball joint is
usually pressed into the control arm and connects to the
steering knuckle through a tapered stud that is held in
position with a castellated nut and a cotter pin.
A ball joint stud, nut and rubber seal is about all your
eye will see of the ball joint assembly. The function of
the rubber seal is to retain the lubricating grease, which
it contains, and to protect this grease from contamina
tion by water or foreign material (sand, dirt, etc.). If this
seal is damaged (torn or pulled off its metal retainer) the
ball joint should be replaced. Check the Service
procedure for inspection and replacement of a ball joint
suspected of being in need of replacement.
NOTE: Grease fittings on ball joints should
be wiped clean before applying grease to the
joint.
SHOCK ABSORBERS
Shock absorbers are hydraulic devices that help to
control the up-and-down and rolling motion of a vehicle
SHORT ARM
BALL JOINT
Fig. 4—Control Arms
LIGHT DUTY TRUCK SERVICE MANUAL
Summary of Contents for Light Duty Truck 1973
Page 1: ......
Page 4: ......
Page 6: ......
Page 53: ...HEATER AND AIR CONDITIONING 1A 27 LIGHT DUTY TRUCK SERVICE MANUAL...
Page 115: ...LIGHT DUTY TRUCK SERVICE M A N U A L HEATER AND AIR CONDITIONING 1A 89...
Page 123: ...BODY 1B 3 Fig 6 Typical 06 Van LIGHT DUTY TRUCK SERVICE MANUAL...
Page 149: ...BODY 1B 29 Fig 84 Body Mounting 06 Fig 85 Body Mounting 14 LIGHT DUTY TRUCK SERVICE MANUAL...
Page 171: ...LIGHT DUTY TRUCK SERVICE M A N U A L Fig 2 Frame Horizontal Checking Typical FRAME 2 3...
Page 173: ...LIGHT DUTY TRUCK SERVICE M A N U A L Fig 4 10 30 Series Truck Frame FRAME 2 5...
Page 174: ...2 6 FRAME LIGHT DUTY TRUCK SERVICE MANUAL Fig 5 Underbody Reference Points G Van...
Page 185: ...FRONT SUSPENSION 3 11 Fig 16 Toe out on Turns LIGHT DUTY TRUCK SERVICE MANUAL...
Page 224: ......
Page 266: ......
Page 351: ...ENGINE 6 15 Fig ID Sectional View of Eight Cylinder Engine LIGHT DUTY TRUCK SERVICE MANUAL...
Page 375: ...EN G IN E 6 39 LIGHT DUTY TRUCK SERVICE MANUAL...
Page 376: ...6 4 0 ENGINE LIGHT DUTY TRUCK SERVICE MANUAL...
Page 377: ...ENG IN E 6 41 LIGHT DUTY TRUCK SERVICE MANUAL...
Page 378: ...LIGHT DUTY TRUCK SERVICE MANUAL Fig 37L K Series Engine Front Mount 6 42 ENG INE...
Page 400: ...6 6 4 ENG INE LIGHT DUTY TRUCK SERVICE MANUAL...
Page 401: ...ENG IN E 6 65 LIGHT DUTY TRUCK SERVICE MANUAL...
Page 402: ...6 6 6 ENGINE LIGHT DUTY TRUCK SERVICE MANUAL...
Page 403: ...E NG IN E 6 67 Fig 36V C Series Engine Mounts LIGHT DUTY TRUCK SERVICE MANUAL...
Page 410: ......
Page 423: ...EN G IN E C OOLING 6K 13 Fig 16 Overheating Chart LIGHT DUTY TRUCK SERVICE MANUAL...
Page 424: ...6 K 1 4 ENG INE COOLING Fig 17 Coolant Loss Chart LIGHT DUTY TRUCK SERVICE MANUAL...
Page 456: ...6M 32 ENGINE FUEL Fig K15 Accelerator Controls G Van L 6 LIGHT DUTY TRUCK SERVICE MANUAL...
Page 492: ......
Page 512: ...Fig 18e Vacuum Advance Diagram V8 Engine...
Page 516: ...6 T 2 4 E M IS S IO N CONTROL SYSTEMS LIGHT DUTY TRUCK SERVICE MANUAL...
Page 528: ......
Page 590: ......
Page 593: ...CLUTCHES MANUAL TRANSMISSIONS 7M 3 LIGHT DUTY TRUCK SERVICE MANUAL...
Page 598: ...7M 8 CLUTCHES MANUAL TRANSMISSIONS LIGHT DUTY TRUCK SERVICE MANUAL...
Page 642: ......
Page 654: ......
Page 743: ...FUEL TANKS AND EXHAUST 8 13 LIGHT DUTY TRUCK SERVICE MANUAL...
Page 744: ...8 14 FUEL TANKS AND EXHAUST LIGHT DUTY TRUCK SERVICE MANUAL...
Page 760: ...8 30 FUEL TANKS AND EXHAUST Fig 40 Exhaust Pipe P Models LIGHT DUTY TRUCK SERVICE MANUAL...
Page 761: ...FUEL TANKS AND EXHAUST 8 31 LIGHT DUTY TRUCK SERVICE MANUAL...
Page 763: ...FUEL TANKS AND EXHAUST 8 33 LIGHT DUTY TRUCK SERVICE MANUAL...
Page 766: ......
Page 832: ...LIGHT DUTY TRUCK SERVICE MANUAL Fig 106 Power Steering Pump Mounting Typical 9 66 STEERING...
Page 833: ...PUMP ASSEMBLY STEERING GEAR TYPICAL SMALL V8 TYPICAL LARGE V8 STEERING 9 67...
Page 861: ...STEERING 9 95 Fig 134 Power Steering Pump Leakage LIGHT DUTY TRUCK SERVICE MANUAL...
Page 864: ......
Page 876: ......
Page 886: ...11 10 CHASSIS SHEET METAL LIGHT DUTY TRUCK SERVICE MANUAL...
Page 891: ...ELECTRICAL BODY AND CHASSIS 12 5 LIGHT DUTY TRUCK SERVICE MANUAL...
Page 934: ......
Page 942: ......
Page 970: ......
Page 972: ......
Page 974: ......
Page 976: ...V...
Page 978: ......
Page 979: ......