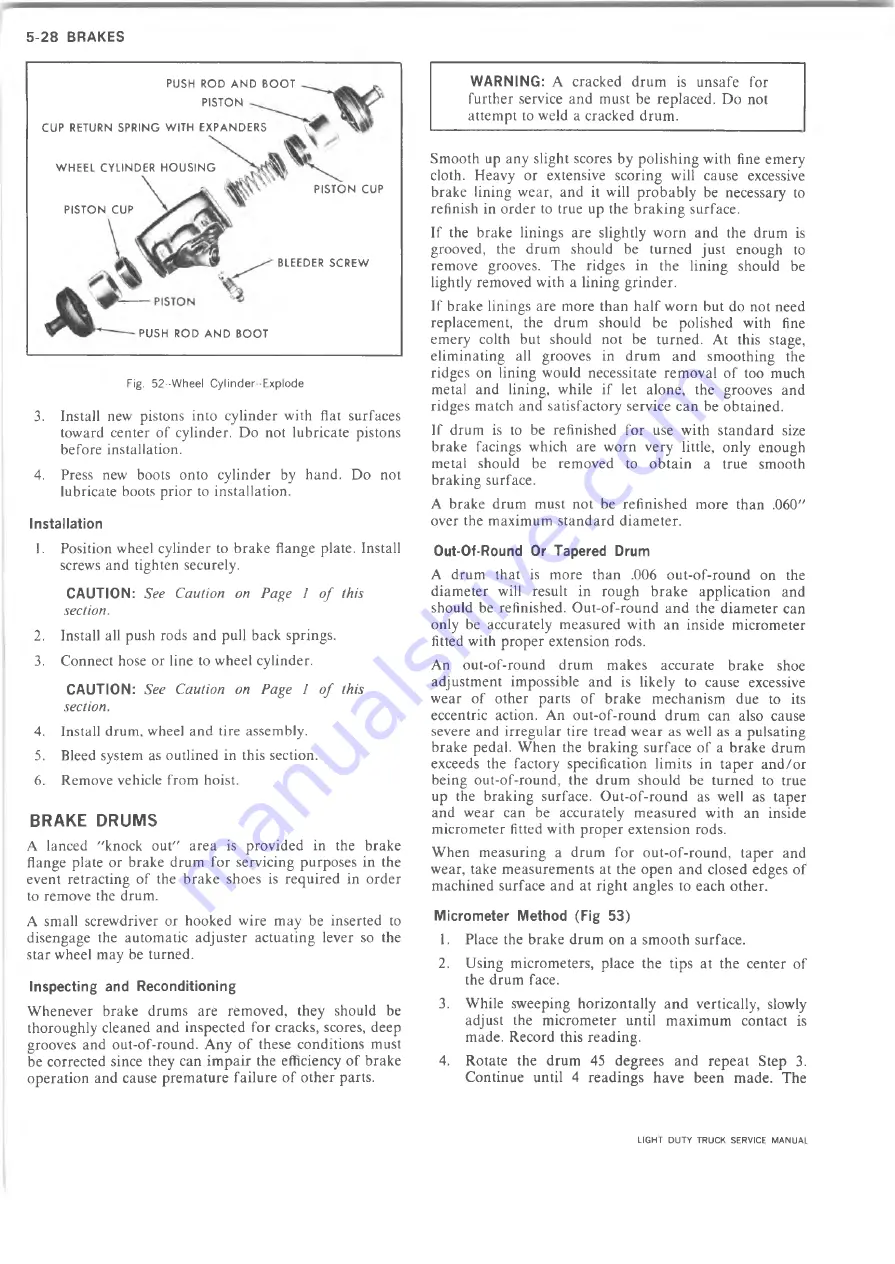
5 - 2 8 BRAKES
WARNING:
A cracked drum is unsafe for
further service and must be replaced. Do not
attempt to weld a cracked drum.
PUSH ROD A N D BOOT
PISTON
CUP RETURN SPRING WITH EXPANDERS
WHEEL CYLINDER HOUSING
PISTON CUP
PISTON CUP
BLEEDER SCREW
PUSH ROD A N D BOOT
Fig. 52 -Wheel Cylinder-Explode
3. Install new pistons into cylinder with flat surfaces
toward center of cylinder. Do not lubricate pistons
before installation.
4. Press new boots onto cylinder by hand. Do not
lubricate boots prior to installation.
Installation
1. Position wheel cylinder to brake flange plate. Install
screws and tighten securely.
CAUTION:
See Caution on Page 1 of this
section.
2. Install all push rods and pull back springs.
3. Connect hose or line to wheel cylinder.
CAUTION:
See Caution on Page 1 of this
section.
4.
Install drum, wheel and tire assembly.
5. Bleed system as outlined in this section.
6
. Remove vehicle from hoist.
BRAKE DRUMS
A lanced "knock out" area is provided in the brake
flange plate or brake drum for servicing purposes in the
event retracting of the brake shoes is required in order
to remove the drum.
A small screwdriver or hooked wire may be inserted to
disengage the automatic adjuster actuating lever so the
star wheel may be turned.
Inspecting and Reconditioning
Whenever brake drums are removed, they should be
thoroughly cleaned and inspected for cracks, scores, deep
grooves and out-of-round. Any of these conditions must
be corrected since they can impair the efficiency of brake
operation and cause premature failure of other parts.
Smooth up any slight scores by polishing with fine emery
cloth. Heavy or extensive scoring will cause excessive
brake lining wear, and it will probably be necessary to
refinish in order to true up the braking surface.
If the brake linings are slightly worn and the drum is
grooved, the drum should be turned just enough to
remove grooves. The ridges in the lining should be
lightly removed with a lining grinder.
If brake linings are more than half worn but do not need
replacement, the drum should be polished with fine
emery colth but should not be turned. At this stage,
eliminating all grooves in drum and smoothing the
ridges on lining would necessitate removal of too much
metal and lining, while if let alone, the grooves and
ridges match and satisfactory service can be obtained.
If drum is to be refinished for use with standard size
brake facings which are worn very little, only enough
metal should be removed to obtain a true smooth
braking surface.
A brake drum must not be refinished more than .060"
over the maximum standard diameter.
Out-Of-Round Or Tapered Drum
A drum that is more than .006 out-of-round on the
diameter will result in rough brake application and
should be refinished. Out-of-round and the diameter can
only be accurately measured with an inside micrometer
fitted with proper extension rods.
An out-of-round drum makes accurate brake shoe
adjustment impossible and is likely to cause excessive
wear of other parts of brake mechanism due to its
eccentric action. An out-of-round drum can also cause
severe and irregular tire tread wear as well as a pulsating
brake pedal. When the braking surface of a brake drum
exceeds the factory specification limits in taper and/or
being out-of-round, the drum should be turned to true
up the braking surface. Out-of-round as well as taper
and wear can be accurately measured with an inside
micrometer fitted with proper extension rods.
When measuring a drum for out-of-round, taper and
wear, take measurements at the open and closed edges of
machined surface and at right angles to each other.
Micrometer Method (Fig 53)
1. Place the brake drum on a smooth surface.
2. Using micrometers, place the tips at the center of
the drum face.
3. While sweeping horizontally and vertically, slowly
adjust the micrometer until maximum contact is
made. Record this reading.
4. Rotate the drum 45 degrees and repeat Step 3.
Continue until 4 readings have been made. The
LIGHT DUTY TRUCK SERVICE MANUAL
Summary of Contents for Light Duty Truck 1973
Page 1: ......
Page 4: ......
Page 6: ......
Page 53: ...HEATER AND AIR CONDITIONING 1A 27 LIGHT DUTY TRUCK SERVICE MANUAL...
Page 115: ...LIGHT DUTY TRUCK SERVICE M A N U A L HEATER AND AIR CONDITIONING 1A 89...
Page 123: ...BODY 1B 3 Fig 6 Typical 06 Van LIGHT DUTY TRUCK SERVICE MANUAL...
Page 149: ...BODY 1B 29 Fig 84 Body Mounting 06 Fig 85 Body Mounting 14 LIGHT DUTY TRUCK SERVICE MANUAL...
Page 171: ...LIGHT DUTY TRUCK SERVICE M A N U A L Fig 2 Frame Horizontal Checking Typical FRAME 2 3...
Page 173: ...LIGHT DUTY TRUCK SERVICE M A N U A L Fig 4 10 30 Series Truck Frame FRAME 2 5...
Page 174: ...2 6 FRAME LIGHT DUTY TRUCK SERVICE MANUAL Fig 5 Underbody Reference Points G Van...
Page 185: ...FRONT SUSPENSION 3 11 Fig 16 Toe out on Turns LIGHT DUTY TRUCK SERVICE MANUAL...
Page 224: ......
Page 266: ......
Page 351: ...ENGINE 6 15 Fig ID Sectional View of Eight Cylinder Engine LIGHT DUTY TRUCK SERVICE MANUAL...
Page 375: ...EN G IN E 6 39 LIGHT DUTY TRUCK SERVICE MANUAL...
Page 376: ...6 4 0 ENGINE LIGHT DUTY TRUCK SERVICE MANUAL...
Page 377: ...ENG IN E 6 41 LIGHT DUTY TRUCK SERVICE MANUAL...
Page 378: ...LIGHT DUTY TRUCK SERVICE MANUAL Fig 37L K Series Engine Front Mount 6 42 ENG INE...
Page 400: ...6 6 4 ENG INE LIGHT DUTY TRUCK SERVICE MANUAL...
Page 401: ...ENG IN E 6 65 LIGHT DUTY TRUCK SERVICE MANUAL...
Page 402: ...6 6 6 ENGINE LIGHT DUTY TRUCK SERVICE MANUAL...
Page 403: ...E NG IN E 6 67 Fig 36V C Series Engine Mounts LIGHT DUTY TRUCK SERVICE MANUAL...
Page 410: ......
Page 423: ...EN G IN E C OOLING 6K 13 Fig 16 Overheating Chart LIGHT DUTY TRUCK SERVICE MANUAL...
Page 424: ...6 K 1 4 ENG INE COOLING Fig 17 Coolant Loss Chart LIGHT DUTY TRUCK SERVICE MANUAL...
Page 456: ...6M 32 ENGINE FUEL Fig K15 Accelerator Controls G Van L 6 LIGHT DUTY TRUCK SERVICE MANUAL...
Page 492: ......
Page 512: ...Fig 18e Vacuum Advance Diagram V8 Engine...
Page 516: ...6 T 2 4 E M IS S IO N CONTROL SYSTEMS LIGHT DUTY TRUCK SERVICE MANUAL...
Page 528: ......
Page 590: ......
Page 593: ...CLUTCHES MANUAL TRANSMISSIONS 7M 3 LIGHT DUTY TRUCK SERVICE MANUAL...
Page 598: ...7M 8 CLUTCHES MANUAL TRANSMISSIONS LIGHT DUTY TRUCK SERVICE MANUAL...
Page 642: ......
Page 654: ......
Page 743: ...FUEL TANKS AND EXHAUST 8 13 LIGHT DUTY TRUCK SERVICE MANUAL...
Page 744: ...8 14 FUEL TANKS AND EXHAUST LIGHT DUTY TRUCK SERVICE MANUAL...
Page 760: ...8 30 FUEL TANKS AND EXHAUST Fig 40 Exhaust Pipe P Models LIGHT DUTY TRUCK SERVICE MANUAL...
Page 761: ...FUEL TANKS AND EXHAUST 8 31 LIGHT DUTY TRUCK SERVICE MANUAL...
Page 763: ...FUEL TANKS AND EXHAUST 8 33 LIGHT DUTY TRUCK SERVICE MANUAL...
Page 766: ......
Page 832: ...LIGHT DUTY TRUCK SERVICE MANUAL Fig 106 Power Steering Pump Mounting Typical 9 66 STEERING...
Page 833: ...PUMP ASSEMBLY STEERING GEAR TYPICAL SMALL V8 TYPICAL LARGE V8 STEERING 9 67...
Page 861: ...STEERING 9 95 Fig 134 Power Steering Pump Leakage LIGHT DUTY TRUCK SERVICE MANUAL...
Page 864: ......
Page 876: ......
Page 886: ...11 10 CHASSIS SHEET METAL LIGHT DUTY TRUCK SERVICE MANUAL...
Page 891: ...ELECTRICAL BODY AND CHASSIS 12 5 LIGHT DUTY TRUCK SERVICE MANUAL...
Page 934: ......
Page 942: ......
Page 970: ......
Page 972: ......
Page 974: ......
Page 976: ...V...
Page 978: ......
Page 979: ......