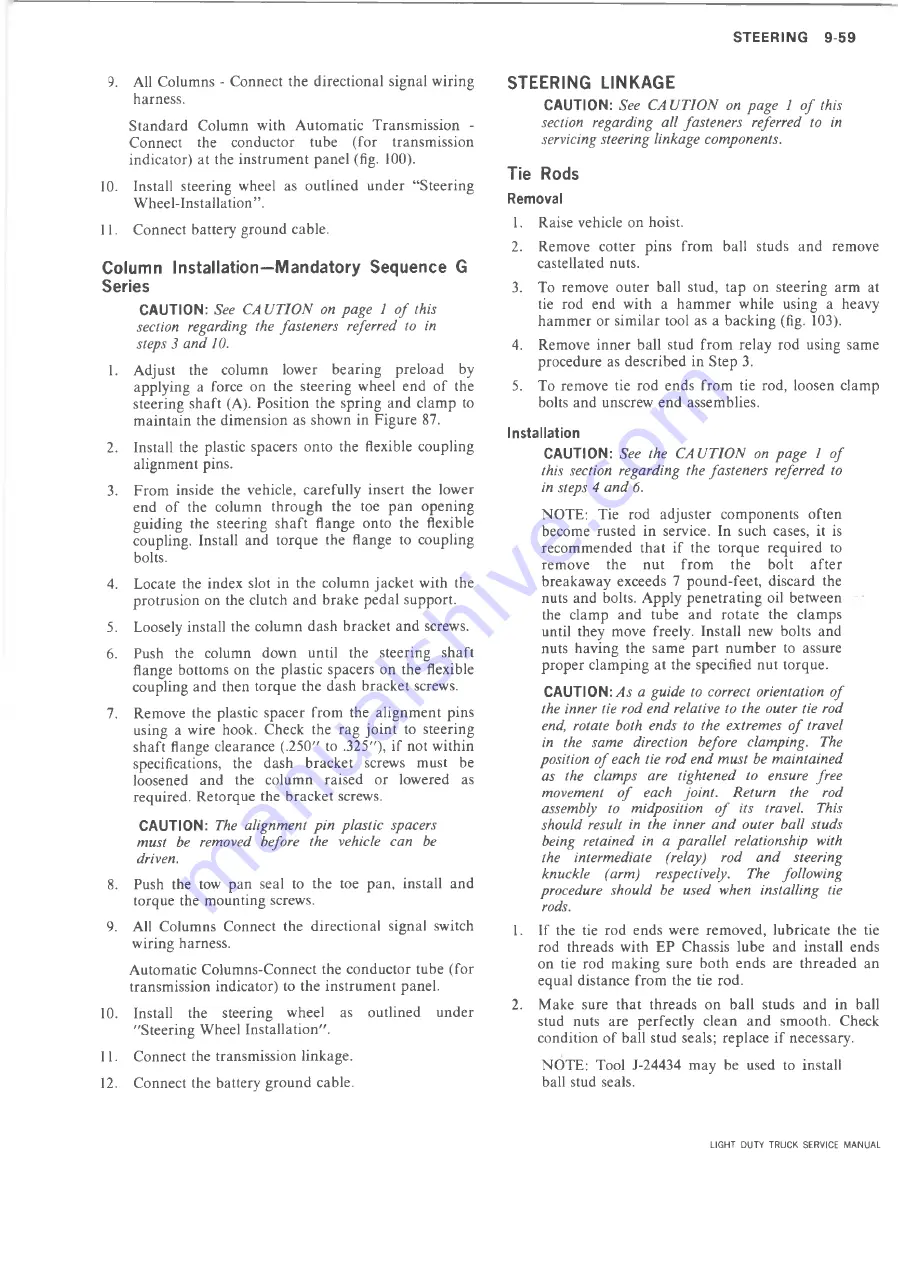
STEER IN G
9 -5 9
9. All Columns - Connect the directional signal wiring
harness.
Standard Column with Automatic Transmission -
Connect the conductor tube (for transmission
indicator) at the instrument panel (fig. 100).
10. Install steering wheel as outlined under “Steering
Wheel-Installation”.
11. Connect battery ground cable.
Column Installation—Mandatory Sequence G
Series
CAUTION:
See CAUTION on page 1 of this
section regarding the fasteners referred to in
steps 3 and 10.
1. Adjust the column lower bearing preload by
applying a force on the steering wheel end of the
steering shaft (A). Position the spring and clamp to
maintain the dimension as shown in Figure 87.
2. Install the plastic spacers onto the flexible coupling
alignment pins.
3. From inside the vehicle, carefully insert the lower
end of the column through the toe pan opening
guiding the steering shaft flange onto the flexible
coupling. Install and torque the flange to coupling
bolts.
4. Locate the index slot in the column jacket with the
protrusion on the clutch and brake pedal support.
5. Loosely install the column dash bracket and screws.
6. Push the column down until the steering shaft
flange bottoms on the plastic spacers on the flexible
coupling and then torque the dash bracket screws.
7. Remove the plastic spacer from the alignment pins
using a wire hook. Check the rag joint to steering
shaft flange clearance (.250" to .325"), if not within
specifications, the dash bracket screws must be
loosened and the column raised or lowered as
required. Retorque the bracket screws.
CAUTION:
The alignment pin plastic spacers
must be removed before the vehicle can be
driven.
8. Push the tow pan seal to the toe pan, install and
torque the mounting screws.
9. All Columns Connect the directional signal switch
wiring harness.
Automatic Columns-Connect the conductor tube (for
transmission indicator) to the instrument panel.
10. Install the steering wheel as outlined under
"Steering Wheel Installation".
11. Connect the transmission linkage.
12. Connect the battery ground cable.
CAUTION:
See CAUTION on page 1 of this
section regarding all fasteners referred to in
servicing steering linkage components.
Tie Rods
Removal
1. Raise vehicle on hoist.
2. Remove cotter pins from ball studs and remove
castellated nuts.
3. To remove outer ball stud, tap on steering arm at
tie rod end with a hammer while using a heavy
hammer or similar tool as a backing (fig. 103).
4. Remove inner ball stud from relay rod using same
procedure as described in Step 3.
5. To remove tie rod ends from tie rod, loosen clamp
bolts and unscrew end assemblies.
Installation
CAUTION:
See the CAUTION on page 1 of
this section regarding the fasteners referred to
in steps 4 and 6.
NOTE: Tie rod adjuster components often
become rusted in service. In such cases, it is
recommended that if the torque required to
remove the nut from the bolt after
breakaway exceeds 7 pound-feet, discard the
nuts and bolts. Apply penetrating oil between
the clamp and tube and rotate the clamps
until they move freely. Install new bolts and
nuts having the same part number to assure
proper clamping at the specified nut torque.
CAUTION:
As a guide to correct orientation of
the inner tie rod end relative to the outer tie rod
end, rotate both ends to the extremes of travel
in the same direction before clamping. The
position of each tie rod end must be maintained
as the clamps are tightened to ensure free
movement of each joint. Return the rod
assembly to midposition of its travel. This
should result in the inner and outer ball studs
being retained in a parallel relationship with
the intermediate (relay) rod and steering
knuckle (arm) respectively. The following
procedure should be used when installing tie
rods.
1. If the tie rod ends were removed, lubricate the tie
rod threads with EP Chassis lube and install ends
on tie rod making sure both ends are threaded an
equal distance from the tie rod.
2. Make sure that threads on ball studs and in ball
stud nuts are perfectly clean and smooth. Check
condition of ball stud seals; replace if necessary.
NOTE: Tool J-24434 may be used to install
ball stud seals.
STEERING LINKAGE
LIGHT DUTY TRUCK SERVICE MANUAL
Summary of Contents for Light Duty Truck 1973
Page 1: ......
Page 4: ......
Page 6: ......
Page 53: ...HEATER AND AIR CONDITIONING 1A 27 LIGHT DUTY TRUCK SERVICE MANUAL...
Page 115: ...LIGHT DUTY TRUCK SERVICE M A N U A L HEATER AND AIR CONDITIONING 1A 89...
Page 123: ...BODY 1B 3 Fig 6 Typical 06 Van LIGHT DUTY TRUCK SERVICE MANUAL...
Page 149: ...BODY 1B 29 Fig 84 Body Mounting 06 Fig 85 Body Mounting 14 LIGHT DUTY TRUCK SERVICE MANUAL...
Page 171: ...LIGHT DUTY TRUCK SERVICE M A N U A L Fig 2 Frame Horizontal Checking Typical FRAME 2 3...
Page 173: ...LIGHT DUTY TRUCK SERVICE M A N U A L Fig 4 10 30 Series Truck Frame FRAME 2 5...
Page 174: ...2 6 FRAME LIGHT DUTY TRUCK SERVICE MANUAL Fig 5 Underbody Reference Points G Van...
Page 185: ...FRONT SUSPENSION 3 11 Fig 16 Toe out on Turns LIGHT DUTY TRUCK SERVICE MANUAL...
Page 224: ......
Page 266: ......
Page 351: ...ENGINE 6 15 Fig ID Sectional View of Eight Cylinder Engine LIGHT DUTY TRUCK SERVICE MANUAL...
Page 375: ...EN G IN E 6 39 LIGHT DUTY TRUCK SERVICE MANUAL...
Page 376: ...6 4 0 ENGINE LIGHT DUTY TRUCK SERVICE MANUAL...
Page 377: ...ENG IN E 6 41 LIGHT DUTY TRUCK SERVICE MANUAL...
Page 378: ...LIGHT DUTY TRUCK SERVICE MANUAL Fig 37L K Series Engine Front Mount 6 42 ENG INE...
Page 400: ...6 6 4 ENG INE LIGHT DUTY TRUCK SERVICE MANUAL...
Page 401: ...ENG IN E 6 65 LIGHT DUTY TRUCK SERVICE MANUAL...
Page 402: ...6 6 6 ENGINE LIGHT DUTY TRUCK SERVICE MANUAL...
Page 403: ...E NG IN E 6 67 Fig 36V C Series Engine Mounts LIGHT DUTY TRUCK SERVICE MANUAL...
Page 410: ......
Page 423: ...EN G IN E C OOLING 6K 13 Fig 16 Overheating Chart LIGHT DUTY TRUCK SERVICE MANUAL...
Page 424: ...6 K 1 4 ENG INE COOLING Fig 17 Coolant Loss Chart LIGHT DUTY TRUCK SERVICE MANUAL...
Page 456: ...6M 32 ENGINE FUEL Fig K15 Accelerator Controls G Van L 6 LIGHT DUTY TRUCK SERVICE MANUAL...
Page 492: ......
Page 512: ...Fig 18e Vacuum Advance Diagram V8 Engine...
Page 516: ...6 T 2 4 E M IS S IO N CONTROL SYSTEMS LIGHT DUTY TRUCK SERVICE MANUAL...
Page 528: ......
Page 590: ......
Page 593: ...CLUTCHES MANUAL TRANSMISSIONS 7M 3 LIGHT DUTY TRUCK SERVICE MANUAL...
Page 598: ...7M 8 CLUTCHES MANUAL TRANSMISSIONS LIGHT DUTY TRUCK SERVICE MANUAL...
Page 642: ......
Page 654: ......
Page 743: ...FUEL TANKS AND EXHAUST 8 13 LIGHT DUTY TRUCK SERVICE MANUAL...
Page 744: ...8 14 FUEL TANKS AND EXHAUST LIGHT DUTY TRUCK SERVICE MANUAL...
Page 760: ...8 30 FUEL TANKS AND EXHAUST Fig 40 Exhaust Pipe P Models LIGHT DUTY TRUCK SERVICE MANUAL...
Page 761: ...FUEL TANKS AND EXHAUST 8 31 LIGHT DUTY TRUCK SERVICE MANUAL...
Page 763: ...FUEL TANKS AND EXHAUST 8 33 LIGHT DUTY TRUCK SERVICE MANUAL...
Page 766: ......
Page 832: ...LIGHT DUTY TRUCK SERVICE MANUAL Fig 106 Power Steering Pump Mounting Typical 9 66 STEERING...
Page 833: ...PUMP ASSEMBLY STEERING GEAR TYPICAL SMALL V8 TYPICAL LARGE V8 STEERING 9 67...
Page 861: ...STEERING 9 95 Fig 134 Power Steering Pump Leakage LIGHT DUTY TRUCK SERVICE MANUAL...
Page 864: ......
Page 876: ......
Page 886: ...11 10 CHASSIS SHEET METAL LIGHT DUTY TRUCK SERVICE MANUAL...
Page 891: ...ELECTRICAL BODY AND CHASSIS 12 5 LIGHT DUTY TRUCK SERVICE MANUAL...
Page 934: ......
Page 942: ......
Page 970: ......
Page 972: ......
Page 974: ......
Page 976: ...V...
Page 978: ......
Page 979: ......