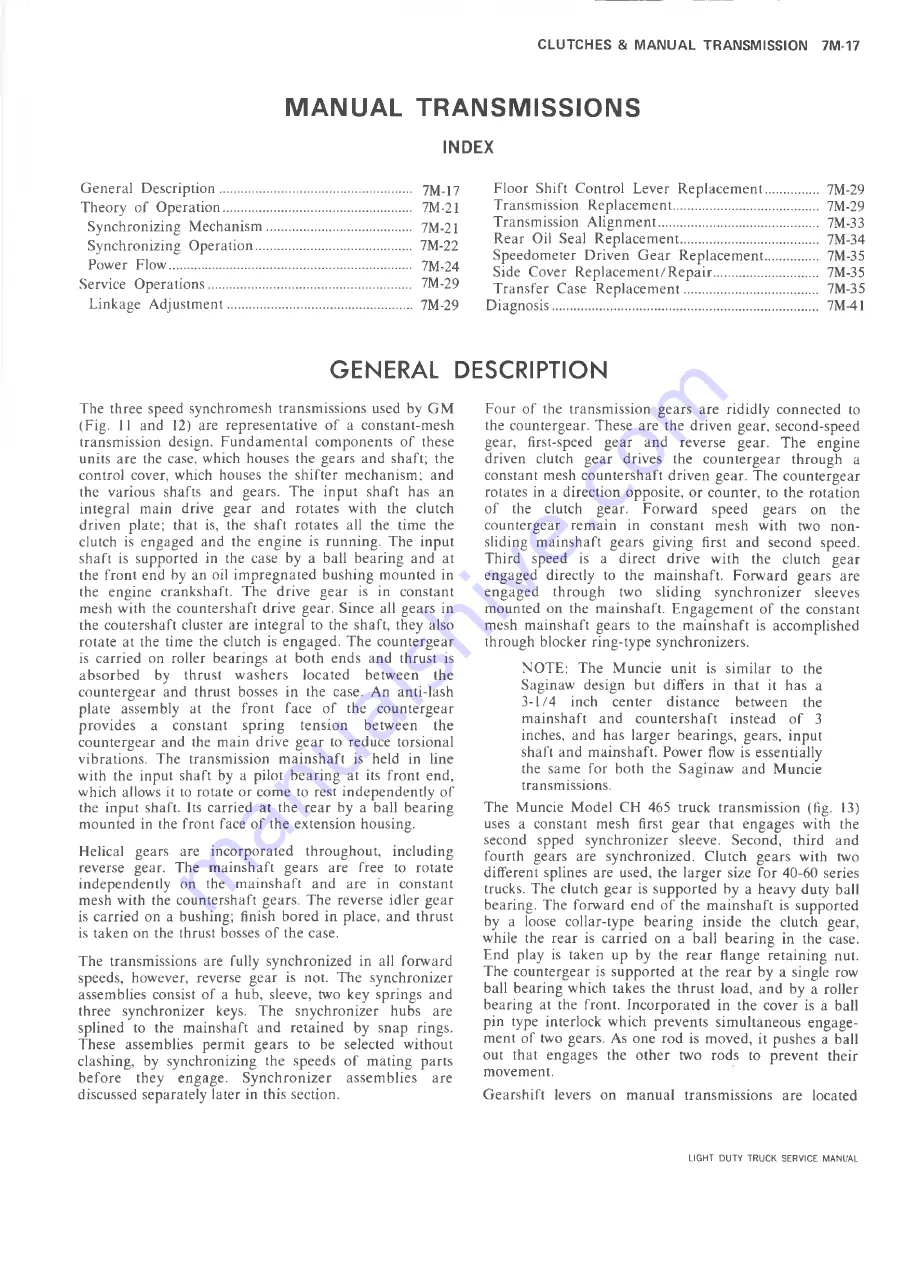
CLUTCHES & MANUAL TRANSMISSION 7M-17
MANUAL TRANSMISSIONS
INDEX
General Description....................................................... 7M-17
Theory of Operation...................................................... 7M-21
Synchronizing Mechanism......................................... 7M-21
Synchronizing Operation............................................. 7M-22
Power Flow...................................................................... 7M-24
Service Operations.......................................................... 7M-29
Linkage Adjustment..................................................... 7M-29
Floor Shift Control Lever Replacement............... 7M-29
Transmission Replacement.......................................... 7M-29
Transmission Alignment...............................................7M-33
Rear Oil Seal Replacement........................................ 7M-34
Speedometer Driven Gear Replacement................7M-35
Side Cover Replacement/Repair...............................7M-35
Transfer Case Replacement...................................... .7M-35
Diagnosis............................................................................ .7M-41
GENERAL DESCRIPTION
The three speed synchromesh transmissions used by GM
(Fig. II and 12) are representative of a constant-mesh
transmission design. Fundamental components of these
units are the case, which houses the gears and shaft; the
control cover, which houses the shifter mechanism; and
the various shafts and gears. The input shaft has an
integral main drive gear and rotates with the clutch
driven plate; that is, the shaft rotates all the time the
clutch is engaged and the engine is running. The input
shaft is supported in the case by a ball bearing and at
the front end by an oil impregnated bushing mounted in
the engine crankshaft. The drive gear is in constant
mesh with the countershaft drive gear. Since all gears in
the coutershaft cluster are integral to the shaft, they also
rotate at the time the clutch is engaged. The countergear
is carried on roller bearings at both ends and thrust is
absorbed by thrust washers located between the
countergear and thrust bosses in the case. An anti-lash
plate assembly at the front face of the countergear
provides a constant spring tension between the
countergear and the main drive gear to reduce torsional
vibrations. The transmission mainshaft is held in line
with the input shaft by a pilot bearing at its front end,
which allows it to rotate or come to rest independently of
the input shaft. Its carried at the rear by a ball bearing
mounted in the front face of the extension housing.
Helical gears are incorporated throughout, including
reverse gear. The mainshaft gears are free to rotate
independently on the mainshaft and are in constant
mesh with the countershaft gears. The reverse idler gear
is carried on a bushing; finish bored in place, and thrust
is taken on the thrust bosses of the case.
The transmissions are fully synchronized in all forward
speeds, however, reverse gear is not. The synchronizer
assemblies consist of a hub, sleeve, two key springs and
three synchronizer keys. The snychronizer hubs are
splined to the mainshaft and retained by snap rings.
These assemblies permit gears to be selected without
clashing, by synchronizing the speeds of mating parts
before they engage. Synchronizer assemblies are
discussed separately later in this section.
Four of the transmission gears are rididly connected to
the countergear. These are the driven gear, second-speed
gear, first-speed gear and reverse gear. The engine
driven clutch gear drives the countergear through a
constant mesh countershaft driven gear. The countergear
rotates in a direction opposite, or counter, to the rotation
of the clutch gear. Forward speed gears on the
countergear remain in constant mesh with two non
sliding mainshaft gears giving first and second speed.
Third speed is a direct drive with the clutch gear
engaged directly to the mainshaft. Forward gears are
engaged through two sliding synchronizer sleeves
mounted on the mainshaft. Engagement of the constant
mesh mainshaft gears to the mainshaft is accomplished
through blocker ring-type synchronizers.
NOTE: The Muncie unit is similar to the
Saginaw design but differs in that it has a
3-1/4 inch center distance between the
mainshaft and countershaft instead of 3
inches, and has larger bearings, gears, input
shaft and mainshaft. Power flow is essentially
the same for both the Saginaw and Muncie
transmissions.
The Muncie Model CH 465 truck transmission (fig. 13)
uses a constant mesh first gear that engages with the
second spped synchronizer sleeve. Second, third and
fourth gears are synchronized. Clutch gears with two
different splines are used, the larger size for 40-60 series
trucks. The clutch gear is supported by a heavy duty ball
bearing. The forward end of the mainshaft is supported
by a loose collar-type bearing inside the clutch gear,
while the rear is carried on a ball bearing in the case.
End play is taken up by the rear flange retaining nut.
The countergear is supported at the rear by a single row
ball bearing which takes the thrust load, and by a roller
bearing at the front. Incorporated in the cover is a ball
pin type interlock which prevents simultaneous engage
ment of two gears. As one rod is moved, it pushes a ball
out that engages the other two rods to prevent their
movement.
Gearshift levers on manual transmissions are located
LIGHT DUTY TRUCK SERVICE MANUAL
Summary of Contents for Light Duty Truck 1973
Page 1: ......
Page 4: ......
Page 6: ......
Page 53: ...HEATER AND AIR CONDITIONING 1A 27 LIGHT DUTY TRUCK SERVICE MANUAL...
Page 115: ...LIGHT DUTY TRUCK SERVICE M A N U A L HEATER AND AIR CONDITIONING 1A 89...
Page 123: ...BODY 1B 3 Fig 6 Typical 06 Van LIGHT DUTY TRUCK SERVICE MANUAL...
Page 149: ...BODY 1B 29 Fig 84 Body Mounting 06 Fig 85 Body Mounting 14 LIGHT DUTY TRUCK SERVICE MANUAL...
Page 171: ...LIGHT DUTY TRUCK SERVICE M A N U A L Fig 2 Frame Horizontal Checking Typical FRAME 2 3...
Page 173: ...LIGHT DUTY TRUCK SERVICE M A N U A L Fig 4 10 30 Series Truck Frame FRAME 2 5...
Page 174: ...2 6 FRAME LIGHT DUTY TRUCK SERVICE MANUAL Fig 5 Underbody Reference Points G Van...
Page 185: ...FRONT SUSPENSION 3 11 Fig 16 Toe out on Turns LIGHT DUTY TRUCK SERVICE MANUAL...
Page 224: ......
Page 266: ......
Page 351: ...ENGINE 6 15 Fig ID Sectional View of Eight Cylinder Engine LIGHT DUTY TRUCK SERVICE MANUAL...
Page 375: ...EN G IN E 6 39 LIGHT DUTY TRUCK SERVICE MANUAL...
Page 376: ...6 4 0 ENGINE LIGHT DUTY TRUCK SERVICE MANUAL...
Page 377: ...ENG IN E 6 41 LIGHT DUTY TRUCK SERVICE MANUAL...
Page 378: ...LIGHT DUTY TRUCK SERVICE MANUAL Fig 37L K Series Engine Front Mount 6 42 ENG INE...
Page 400: ...6 6 4 ENG INE LIGHT DUTY TRUCK SERVICE MANUAL...
Page 401: ...ENG IN E 6 65 LIGHT DUTY TRUCK SERVICE MANUAL...
Page 402: ...6 6 6 ENGINE LIGHT DUTY TRUCK SERVICE MANUAL...
Page 403: ...E NG IN E 6 67 Fig 36V C Series Engine Mounts LIGHT DUTY TRUCK SERVICE MANUAL...
Page 410: ......
Page 423: ...EN G IN E C OOLING 6K 13 Fig 16 Overheating Chart LIGHT DUTY TRUCK SERVICE MANUAL...
Page 424: ...6 K 1 4 ENG INE COOLING Fig 17 Coolant Loss Chart LIGHT DUTY TRUCK SERVICE MANUAL...
Page 456: ...6M 32 ENGINE FUEL Fig K15 Accelerator Controls G Van L 6 LIGHT DUTY TRUCK SERVICE MANUAL...
Page 492: ......
Page 512: ...Fig 18e Vacuum Advance Diagram V8 Engine...
Page 516: ...6 T 2 4 E M IS S IO N CONTROL SYSTEMS LIGHT DUTY TRUCK SERVICE MANUAL...
Page 528: ......
Page 590: ......
Page 593: ...CLUTCHES MANUAL TRANSMISSIONS 7M 3 LIGHT DUTY TRUCK SERVICE MANUAL...
Page 598: ...7M 8 CLUTCHES MANUAL TRANSMISSIONS LIGHT DUTY TRUCK SERVICE MANUAL...
Page 642: ......
Page 654: ......
Page 743: ...FUEL TANKS AND EXHAUST 8 13 LIGHT DUTY TRUCK SERVICE MANUAL...
Page 744: ...8 14 FUEL TANKS AND EXHAUST LIGHT DUTY TRUCK SERVICE MANUAL...
Page 760: ...8 30 FUEL TANKS AND EXHAUST Fig 40 Exhaust Pipe P Models LIGHT DUTY TRUCK SERVICE MANUAL...
Page 761: ...FUEL TANKS AND EXHAUST 8 31 LIGHT DUTY TRUCK SERVICE MANUAL...
Page 763: ...FUEL TANKS AND EXHAUST 8 33 LIGHT DUTY TRUCK SERVICE MANUAL...
Page 766: ......
Page 832: ...LIGHT DUTY TRUCK SERVICE MANUAL Fig 106 Power Steering Pump Mounting Typical 9 66 STEERING...
Page 833: ...PUMP ASSEMBLY STEERING GEAR TYPICAL SMALL V8 TYPICAL LARGE V8 STEERING 9 67...
Page 861: ...STEERING 9 95 Fig 134 Power Steering Pump Leakage LIGHT DUTY TRUCK SERVICE MANUAL...
Page 864: ......
Page 876: ......
Page 886: ...11 10 CHASSIS SHEET METAL LIGHT DUTY TRUCK SERVICE MANUAL...
Page 891: ...ELECTRICAL BODY AND CHASSIS 12 5 LIGHT DUTY TRUCK SERVICE MANUAL...
Page 934: ......
Page 942: ......
Page 970: ......
Page 972: ......
Page 974: ......
Page 976: ...V...
Page 978: ......
Page 979: ......