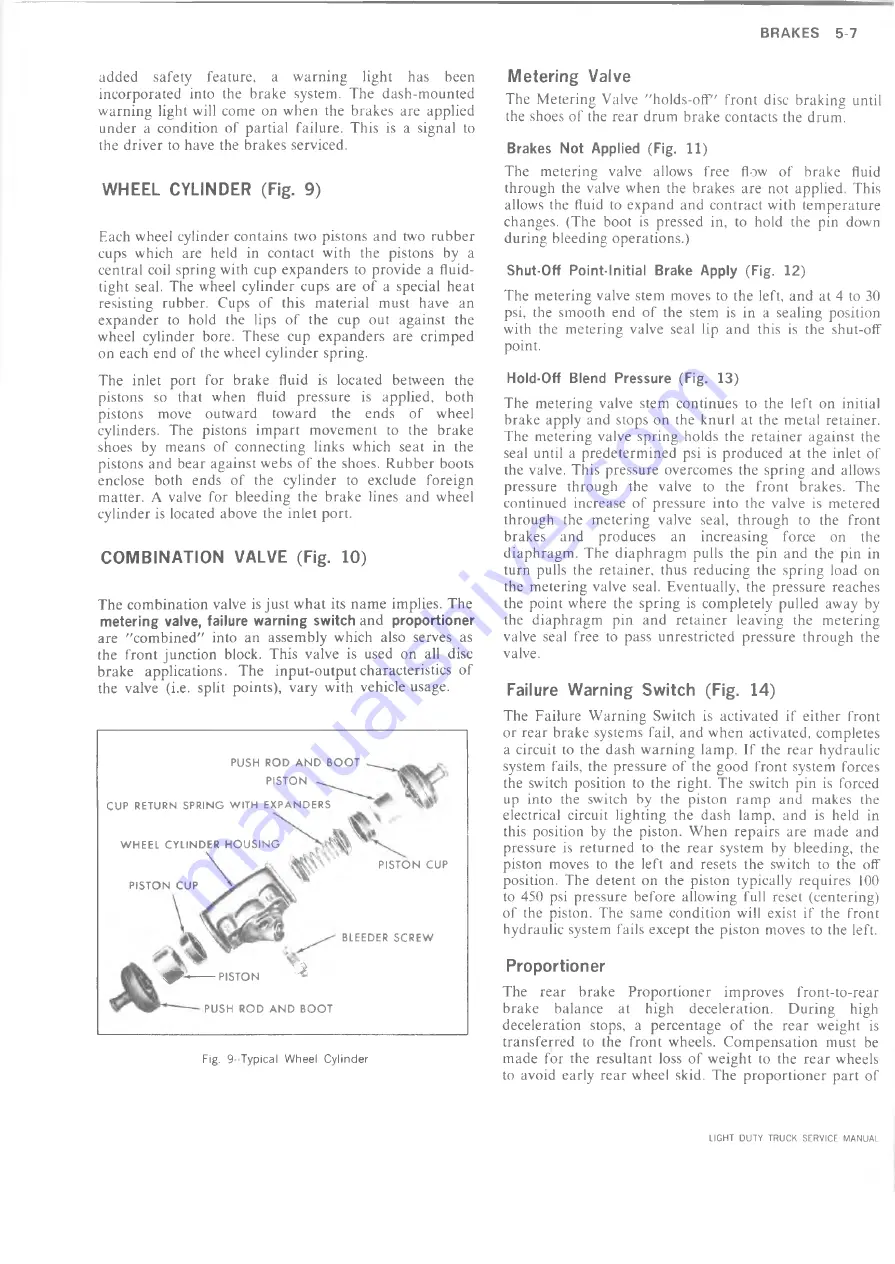
BRAKES
5-7
added safety feature, a warning light has been
incorporated into the brake system. The dash-mounted
warning light will come on when the brakes are applied
under a condition of partial failure. This is a signal to
the driver to have the brakes serviced.
WHEEL CYLINDER (Fig. 9)
Each wheel cylinder contains two pistons and two rubber
cups which are held in contact with the pistons by a
central coil spring with cup expanders to provide a fluid-
tight seal. The wheel cylinder cups are of a special heat
resisting rubber. Cups of this material must have an
expander to hold the lips of the cup out against the
wheel cylinder bore. These cup expanders are crimped
on each end of the wheel cylinder spring.
The inlet port for brake fluid is located between the
pistons so that when fluid pressure is applied, both
pistons move outward toward the ends of wheel
cylinders. The pistons impart movement to the brake
shoes by means of connecting links which seat in the
pistons and bear against webs of the shoes. Rubber boots
enclose both ends of the cylinder to exclude foreign
matter. A valve for bleeding the brake lines and wheel
cylinder is located above the inlet port.
COMBINATION VALVE (Fig. 10)
The combination valve is just what its name implies. The
metering valve, failure warning switch
and
proportioner
are "combined" into an assembly which also serves as
the front junction block. This valve is used on all disc
brake applications. The input-output characteristics of
the valve (i.e. split points), vary with vehicle usage.
Fig. 9- Typical Wheel Cylinder
Metering Valve
The Metering Valve "holds-off" front disc braking until
the shoes of the rear drum brake contacts the drum.
Brakes Not Applied (Fig. 11)
The metering valve allows free flow of brake fluid
through the valve when the brakes are not applied. This
allows the fluid to expand and contract with temperature
changes. (The boot is pressed in, to hold the pin down
during bleeding operations.)
Shut-Off Point-Initial Brake Apply (Fig. 12)
The metering valve stem moves to the left, and at 4 to 30
psi, the smooth end of the stem is in a sealing position
with the metering valve seal lip and this is the shut-off
point.
Hold-Off Blend Pressure (Fig. 13)
The metering valve stem continues to the left on initial
brake apply and stops on the knurl at the metal retainer.
The metering valve spring holds the retainer against the
seal until a predetermined psi is produced at the inlet of
the valve. This pressure overcomes the spring and allows
pressure through the valve to the front brakes. The
continued increase of pressure into the valve is metered
through the metering valve seal, through to the front
brakes and produces an increasing force on the
diaphragm. The diaphragm pulls the pin and the pin in
turn pulls the retainer, thus reducing the spring load on
the metering valve seal. Eventually, the pressure reaches
the point where the spring is completely pulled away by
the diaphragm pin and retainer leaving the metering
valve seal free to pass unrestricted pressure through the
valve.
Failure Warning Switch (Fig. 14)
The Failure Warning Switch is activated if either front
or rear brake systems fail, and when activated, completes
a circuit to the dash warning lamp. If the rear hydraulic
system fails, the pressure of the good front system forces
the switch position to the right. The switch pin is forced
up into the switch by the piston ramp and makes the
electrical circuit lighting the dash lamp, and is held in
this position by the piston. When repairs are made and
pressure is returned to the rear system by bleeding, the
piston moves to the left and resets the switch to the off
position. The detent on the piston typically requires 100
to 450 psi pressure before allowing full reset (centering)
of the piston. The same condition will exist if the front
hydraulic system fails except the piston moves to the left.
Proportioner
The rear brake Proportioner improves front-to-rear
brake balance at high deceleration. During high
deceleration stops, a percentage of the rear weight is
transferred to the front wheels. Compensation must be
made for the resultant loss of weight to the rear wheels
to avoid early rear wheel skid. The proportioner part of
PUSH ROD AN D BOOT
PISTON
CUP RETURN SPRING WITH EXPANDERS
WHEEL CYLINDER HOUSING
PISTON CUP
PISTON CUP
BLEEDER SCREW
'
&
ig F * ------- PISTON
PUSH ROD AND BOOT
LIGHT DUTY TRUCK SERVICE MANUAL
Summary of Contents for Light Duty Truck 1973
Page 1: ......
Page 4: ......
Page 6: ......
Page 53: ...HEATER AND AIR CONDITIONING 1A 27 LIGHT DUTY TRUCK SERVICE MANUAL...
Page 115: ...LIGHT DUTY TRUCK SERVICE M A N U A L HEATER AND AIR CONDITIONING 1A 89...
Page 123: ...BODY 1B 3 Fig 6 Typical 06 Van LIGHT DUTY TRUCK SERVICE MANUAL...
Page 149: ...BODY 1B 29 Fig 84 Body Mounting 06 Fig 85 Body Mounting 14 LIGHT DUTY TRUCK SERVICE MANUAL...
Page 171: ...LIGHT DUTY TRUCK SERVICE M A N U A L Fig 2 Frame Horizontal Checking Typical FRAME 2 3...
Page 173: ...LIGHT DUTY TRUCK SERVICE M A N U A L Fig 4 10 30 Series Truck Frame FRAME 2 5...
Page 174: ...2 6 FRAME LIGHT DUTY TRUCK SERVICE MANUAL Fig 5 Underbody Reference Points G Van...
Page 185: ...FRONT SUSPENSION 3 11 Fig 16 Toe out on Turns LIGHT DUTY TRUCK SERVICE MANUAL...
Page 224: ......
Page 266: ......
Page 351: ...ENGINE 6 15 Fig ID Sectional View of Eight Cylinder Engine LIGHT DUTY TRUCK SERVICE MANUAL...
Page 375: ...EN G IN E 6 39 LIGHT DUTY TRUCK SERVICE MANUAL...
Page 376: ...6 4 0 ENGINE LIGHT DUTY TRUCK SERVICE MANUAL...
Page 377: ...ENG IN E 6 41 LIGHT DUTY TRUCK SERVICE MANUAL...
Page 378: ...LIGHT DUTY TRUCK SERVICE MANUAL Fig 37L K Series Engine Front Mount 6 42 ENG INE...
Page 400: ...6 6 4 ENG INE LIGHT DUTY TRUCK SERVICE MANUAL...
Page 401: ...ENG IN E 6 65 LIGHT DUTY TRUCK SERVICE MANUAL...
Page 402: ...6 6 6 ENGINE LIGHT DUTY TRUCK SERVICE MANUAL...
Page 403: ...E NG IN E 6 67 Fig 36V C Series Engine Mounts LIGHT DUTY TRUCK SERVICE MANUAL...
Page 410: ......
Page 423: ...EN G IN E C OOLING 6K 13 Fig 16 Overheating Chart LIGHT DUTY TRUCK SERVICE MANUAL...
Page 424: ...6 K 1 4 ENG INE COOLING Fig 17 Coolant Loss Chart LIGHT DUTY TRUCK SERVICE MANUAL...
Page 456: ...6M 32 ENGINE FUEL Fig K15 Accelerator Controls G Van L 6 LIGHT DUTY TRUCK SERVICE MANUAL...
Page 492: ......
Page 512: ...Fig 18e Vacuum Advance Diagram V8 Engine...
Page 516: ...6 T 2 4 E M IS S IO N CONTROL SYSTEMS LIGHT DUTY TRUCK SERVICE MANUAL...
Page 528: ......
Page 590: ......
Page 593: ...CLUTCHES MANUAL TRANSMISSIONS 7M 3 LIGHT DUTY TRUCK SERVICE MANUAL...
Page 598: ...7M 8 CLUTCHES MANUAL TRANSMISSIONS LIGHT DUTY TRUCK SERVICE MANUAL...
Page 642: ......
Page 654: ......
Page 743: ...FUEL TANKS AND EXHAUST 8 13 LIGHT DUTY TRUCK SERVICE MANUAL...
Page 744: ...8 14 FUEL TANKS AND EXHAUST LIGHT DUTY TRUCK SERVICE MANUAL...
Page 760: ...8 30 FUEL TANKS AND EXHAUST Fig 40 Exhaust Pipe P Models LIGHT DUTY TRUCK SERVICE MANUAL...
Page 761: ...FUEL TANKS AND EXHAUST 8 31 LIGHT DUTY TRUCK SERVICE MANUAL...
Page 763: ...FUEL TANKS AND EXHAUST 8 33 LIGHT DUTY TRUCK SERVICE MANUAL...
Page 766: ......
Page 832: ...LIGHT DUTY TRUCK SERVICE MANUAL Fig 106 Power Steering Pump Mounting Typical 9 66 STEERING...
Page 833: ...PUMP ASSEMBLY STEERING GEAR TYPICAL SMALL V8 TYPICAL LARGE V8 STEERING 9 67...
Page 861: ...STEERING 9 95 Fig 134 Power Steering Pump Leakage LIGHT DUTY TRUCK SERVICE MANUAL...
Page 864: ......
Page 876: ......
Page 886: ...11 10 CHASSIS SHEET METAL LIGHT DUTY TRUCK SERVICE MANUAL...
Page 891: ...ELECTRICAL BODY AND CHASSIS 12 5 LIGHT DUTY TRUCK SERVICE MANUAL...
Page 934: ......
Page 942: ......
Page 970: ......
Page 972: ......
Page 974: ......
Page 976: ...V...
Page 978: ......
Page 979: ......