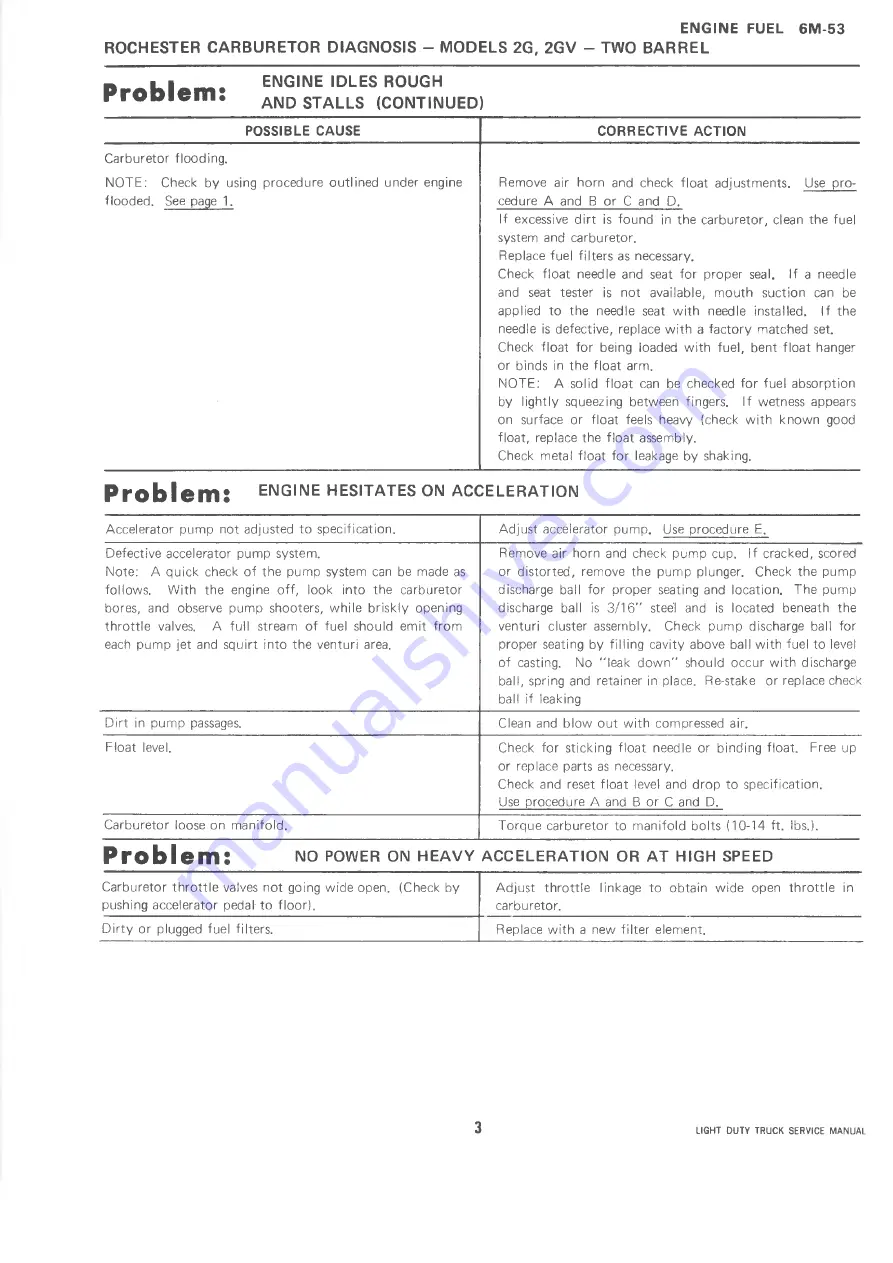
E N G IN E FUEL
6 M - 5 3
ROCHESTER CARBURETOR DIAGNOSIS - MODELS 2G, 2GV - TWO BARREL
Problem:
E N G I N E I D L E S R O U G H
A N D S T A L L S ( C O N T I N U E D )
POSSIBLE CAUSE
CORRECTIVE ACTION
Carburetor flooding.
NOTE: Check by using procedure outlined under engine
flooded. See page 1.
Remove air horn and check float adjustments. Use pro
cedure A and B or C and D.
If excessive d irt is found in the carburetor, clean the fuel
system and carburetor.
Replace fuel filters as necessary.
Check float needle and seat for proper seal.
If a needle
and seat tester is not available, mouth suction can be
applied to the needle seat w ith needle installed. If the
needle is defective, replace w ith a factory matched set.
Check float for being loaded w ith fuel, bent float hanger
or binds in the float arm.
NOTE: A solid float can be checked for fuel absorption
by lightly squeezing between fingers. If wetness appears
on surface or float feels heavy (check w ith known good
float, replace the float assembly.
Check metal float for leakage by shaking.
Problem :
e n g i n e
h e s i t a t e s
o n
a c c e l e r a t i o n
Accelerator pump not adjusted to specification.
Adjust accelerator pump. Use procedure E.
Defective accelerator pump system.
Note: A quick check of the pump system can be made as
follows.
With the engine o ff, look into the carburetor
bores, and observe pump shooters, while briskly opening
thro ttle valves.
A full stream of fuel should emit from
each pump jet and squirt into the venturi area.
Remove air horn and check pump cup. If cracked, scored
or distorted, remove the pump plunger. Check the pump
discharge ball for proper seating and location. The pump
discharge ball is 3/16” steel and is located beneath the
venturi cluster assembly. Check pump discharge ball for
proper seating by filling cavity above ball w ith fuel to level
of casting. No "leak down” should occur w ith discharge
ball, spring and retainer in place. Re-stake or replace check
ball if leaking
D irt in pump passages.
Clean and blow out w ith compressed air.
Float level.
Check for sticking float needle or binding float. Free up
or replace parts as necessary.
Check and reset float level and drop to specification.
Use procedure A and B or C and D.
Carburetor loose on manifold.
Torque carburetor to manifold bolts (10-14 ft. lbs.).
Problem :
N O PO W ER O N H E A V Y A C C E L E R A T I O N O R A T H I G H S P E E D
Carburetor th ro ttle valves not going wide open. (Check by
pushing accelerator pedal- to floor).
Adjust thro ttle linkage to obtain wide open thro ttle in
carburetor.
D irty or plugged fuel filters.
Replace w ith a new filte r element.
3
LIGHT DUTY TRUCK SERVICE MANUAL
Summary of Contents for Light Duty Truck 1973
Page 1: ......
Page 4: ......
Page 6: ......
Page 53: ...HEATER AND AIR CONDITIONING 1A 27 LIGHT DUTY TRUCK SERVICE MANUAL...
Page 115: ...LIGHT DUTY TRUCK SERVICE M A N U A L HEATER AND AIR CONDITIONING 1A 89...
Page 123: ...BODY 1B 3 Fig 6 Typical 06 Van LIGHT DUTY TRUCK SERVICE MANUAL...
Page 149: ...BODY 1B 29 Fig 84 Body Mounting 06 Fig 85 Body Mounting 14 LIGHT DUTY TRUCK SERVICE MANUAL...
Page 171: ...LIGHT DUTY TRUCK SERVICE M A N U A L Fig 2 Frame Horizontal Checking Typical FRAME 2 3...
Page 173: ...LIGHT DUTY TRUCK SERVICE M A N U A L Fig 4 10 30 Series Truck Frame FRAME 2 5...
Page 174: ...2 6 FRAME LIGHT DUTY TRUCK SERVICE MANUAL Fig 5 Underbody Reference Points G Van...
Page 185: ...FRONT SUSPENSION 3 11 Fig 16 Toe out on Turns LIGHT DUTY TRUCK SERVICE MANUAL...
Page 224: ......
Page 266: ......
Page 351: ...ENGINE 6 15 Fig ID Sectional View of Eight Cylinder Engine LIGHT DUTY TRUCK SERVICE MANUAL...
Page 375: ...EN G IN E 6 39 LIGHT DUTY TRUCK SERVICE MANUAL...
Page 376: ...6 4 0 ENGINE LIGHT DUTY TRUCK SERVICE MANUAL...
Page 377: ...ENG IN E 6 41 LIGHT DUTY TRUCK SERVICE MANUAL...
Page 378: ...LIGHT DUTY TRUCK SERVICE MANUAL Fig 37L K Series Engine Front Mount 6 42 ENG INE...
Page 400: ...6 6 4 ENG INE LIGHT DUTY TRUCK SERVICE MANUAL...
Page 401: ...ENG IN E 6 65 LIGHT DUTY TRUCK SERVICE MANUAL...
Page 402: ...6 6 6 ENGINE LIGHT DUTY TRUCK SERVICE MANUAL...
Page 403: ...E NG IN E 6 67 Fig 36V C Series Engine Mounts LIGHT DUTY TRUCK SERVICE MANUAL...
Page 410: ......
Page 423: ...EN G IN E C OOLING 6K 13 Fig 16 Overheating Chart LIGHT DUTY TRUCK SERVICE MANUAL...
Page 424: ...6 K 1 4 ENG INE COOLING Fig 17 Coolant Loss Chart LIGHT DUTY TRUCK SERVICE MANUAL...
Page 456: ...6M 32 ENGINE FUEL Fig K15 Accelerator Controls G Van L 6 LIGHT DUTY TRUCK SERVICE MANUAL...
Page 492: ......
Page 512: ...Fig 18e Vacuum Advance Diagram V8 Engine...
Page 516: ...6 T 2 4 E M IS S IO N CONTROL SYSTEMS LIGHT DUTY TRUCK SERVICE MANUAL...
Page 528: ......
Page 590: ......
Page 593: ...CLUTCHES MANUAL TRANSMISSIONS 7M 3 LIGHT DUTY TRUCK SERVICE MANUAL...
Page 598: ...7M 8 CLUTCHES MANUAL TRANSMISSIONS LIGHT DUTY TRUCK SERVICE MANUAL...
Page 642: ......
Page 654: ......
Page 743: ...FUEL TANKS AND EXHAUST 8 13 LIGHT DUTY TRUCK SERVICE MANUAL...
Page 744: ...8 14 FUEL TANKS AND EXHAUST LIGHT DUTY TRUCK SERVICE MANUAL...
Page 760: ...8 30 FUEL TANKS AND EXHAUST Fig 40 Exhaust Pipe P Models LIGHT DUTY TRUCK SERVICE MANUAL...
Page 761: ...FUEL TANKS AND EXHAUST 8 31 LIGHT DUTY TRUCK SERVICE MANUAL...
Page 763: ...FUEL TANKS AND EXHAUST 8 33 LIGHT DUTY TRUCK SERVICE MANUAL...
Page 766: ......
Page 832: ...LIGHT DUTY TRUCK SERVICE MANUAL Fig 106 Power Steering Pump Mounting Typical 9 66 STEERING...
Page 833: ...PUMP ASSEMBLY STEERING GEAR TYPICAL SMALL V8 TYPICAL LARGE V8 STEERING 9 67...
Page 861: ...STEERING 9 95 Fig 134 Power Steering Pump Leakage LIGHT DUTY TRUCK SERVICE MANUAL...
Page 864: ......
Page 876: ......
Page 886: ...11 10 CHASSIS SHEET METAL LIGHT DUTY TRUCK SERVICE MANUAL...
Page 891: ...ELECTRICAL BODY AND CHASSIS 12 5 LIGHT DUTY TRUCK SERVICE MANUAL...
Page 934: ......
Page 942: ......
Page 970: ......
Page 972: ......
Page 974: ......
Page 976: ...V...
Page 978: ......
Page 979: ......