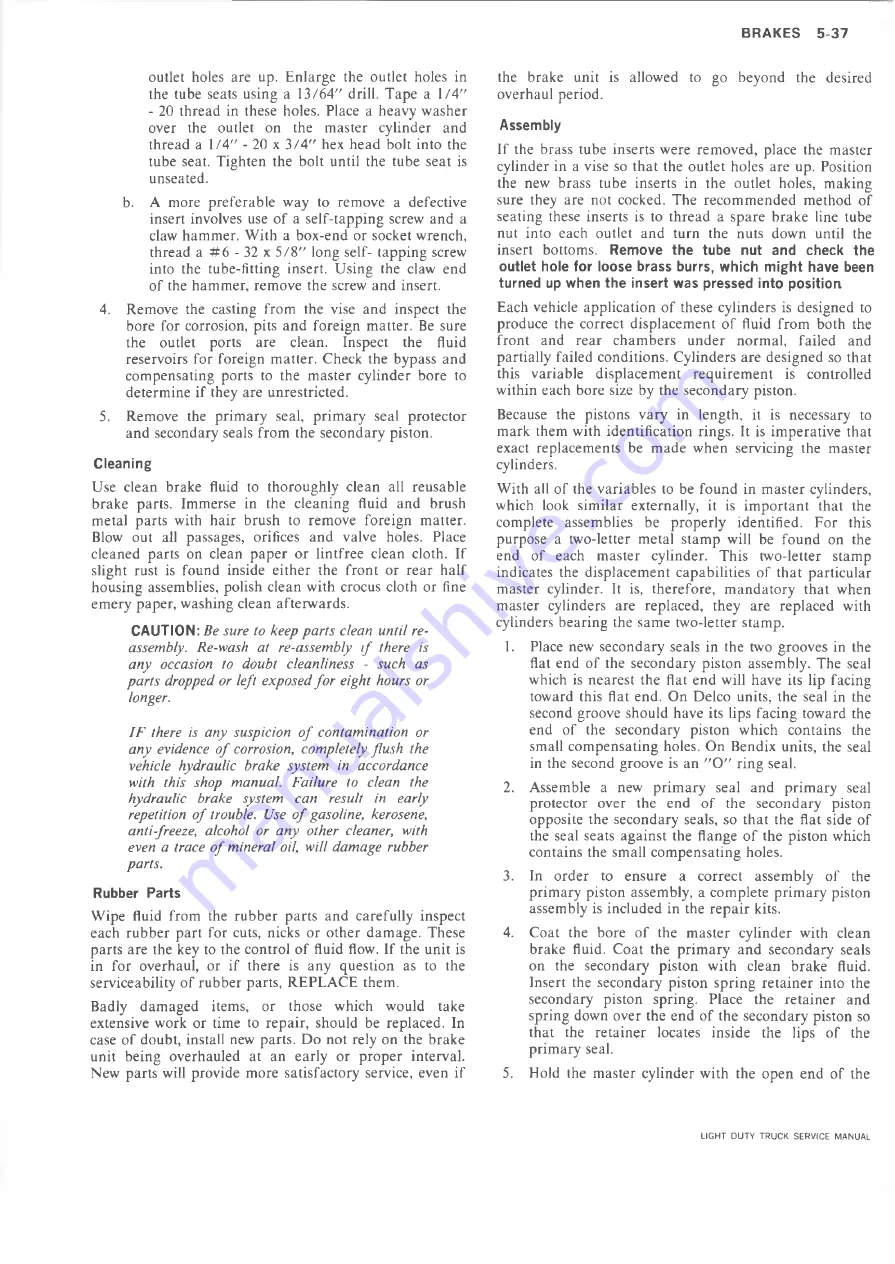
BRAKES
5 -3 7
outlet holes are up. Enlarge the outlet holes in
the tube seats using a 13/64" drill. Tape a 1/4"
- 20 thread in these holes. Place a heavy washer
over the outlet on the master cylinder and
thread a 1/4" - 20 x 3/4" hex head bolt into the
tube seat. Tighten the bolt until the tube seat is
unseated.
b. A more preferable way to remove a defective
insert involves use of a self-tapping screw and a
claw hammer. With a box-end or socket wrench,
thread a
# 6
- 32 x 5/8" long self- tapping screw
into the tube-fitting insert. Using the claw end
of the hammer, remove the screw and insert.
4. Remove the casting from the vise and inspect the
bore for corrosion, pits and foreign matter. Be sure
the outlet ports are clean. Inspect the fluid
reservoirs for foreign matter. Check the bypass and
compensating ports to the master cylinder bore to
determine if they are unrestricted.
5. Remove the primary seal, primary seal protector
and secondary seals from the secondary piston.
Cleaning
Use clean brake fluid to thoroughly clean all reusable
brake parts. Immerse in the cleaning fluid and brush
metal parts with hair brush to remove foreign matter.
Blow out all passages, orifices and valve holes. Place
cleaned parts on clean paper or lintfree clean cloth. If
slight rust is found inside either the front or rear half
housing assemblies, polish clean with crocus cloth or fine
emery paper, washing clean afterwards.
CAUTION:
Be sure to keep parts clean until re
assembly. Re-wash at re-assembly if there is
any occasion to doubt cleanliness - such as
parts dropped or left exposed for eight hours or
longer.
IF there is any suspicion of contamination or
any evidence of corrosion, completely flush the
vehicle hydraulic brake system in accordance
with this shop manual. Failure to clean the
hydraulic brake system can result in early
repetition of trouble. Use of gasoline, kerosene,
anti-freeze, alcohol or any other cleaner, with
even a trace of mineral oil, will damage rubber
parts.
Rubber Parts
Wipe fluid from the rubber parts and carefully inspect
each rubber part for cuts, nicks or other damage. These
parts are the key to the control of fluid flow. If the unit is
in for overhaul, or if there is any question as to the
serviceability of rubber parts, REPLACE them.
Badly damaged items, or those which would take
extensive work or time to repair, should be replaced. In
case of doubt, install new parts. Do not rely on the brake
unit being overhauled at an early or proper interval.
New parts will provide more satisfactory service, even if
the brake unit is allowed to go beyond the desired
overhaul period.
Assembly
If the brass tube inserts were removed, place the master
cylinder in a vise so that the outlet holes are up. Position
the new brass tube inserts in the outlet holes, making
sure they are not cocked. The recommended method of
seating these inserts is to thread a spare brake line tube
nut into each outlet and turn the nuts down until the
insert bottoms.
Remove the tube nut and check the
outlet hole for loose brass burrs, which might have been
turned up when the insert was pressed into position
Each vehicle application of these cylinders is designed to
produce the correct displacement of fluid from both the
front and rear chambers under normal, failed and
partially failed conditions. Cylinders are designed so that
this variable displacement requirement is controlled
within each bore size by the secondary piston.
Because the pistons vary in length, it is necessary to
mark them with identification rings. It is imperative that
exact replacements be made when servicing the master
cylinders.
With all of the variables to be found in master cylinders,
which look similar externally, it is important that the
complete assemblies be properly identified. For this
purpose a two-letter metal stamp will be found on the
end of each master cylinder. This two-letter stamp
indicates the displacement capabilities of that particular
master cylinder. It is, therefore, mandatory that when
master cylinders are replaced, they are replaced with
cylinders bearing the same two-letter stamp.
1. Place new secondary seals in the two grooves in the
flat end of the secondary piston assembly. The seal
which is nearest the flat end will have its lip facing
toward this flat end. On Delco units, the seal in the
second groove should have its lips facing toward the
end of the secondary piston which contains the
small compensating holes. On Bendix units, the seal
in the second groove is an "O" ring seal.
2. Assemble a new primary seal and primary seal
protector over the end of the secondary piston
opposite the secondary seals, so that the flat side of
the seal seats against the flange of the piston which
contains the small compensating holes.
3. In order to ensure a correct assembly of the
primary piston assembly, a complete primary piston
assembly is included in the repair kits.
4. Coat the bore of the master cylinder with clean
brake fluid. Coat the primary and secondary seals
on the secondary piston with clean brake fluid.
Insert the secondary piston spring retainer into the
secondary piston spring. Place the retainer and
spring down over the end of the secondary piston so
that the retainer locates inside the lips of the
primary seal.
5. Hold the master cylinder with the open end of the
LIGHT DUTY TRUCK SERVICE MANUAL
Summary of Contents for Light Duty Truck 1973
Page 1: ......
Page 4: ......
Page 6: ......
Page 53: ...HEATER AND AIR CONDITIONING 1A 27 LIGHT DUTY TRUCK SERVICE MANUAL...
Page 115: ...LIGHT DUTY TRUCK SERVICE M A N U A L HEATER AND AIR CONDITIONING 1A 89...
Page 123: ...BODY 1B 3 Fig 6 Typical 06 Van LIGHT DUTY TRUCK SERVICE MANUAL...
Page 149: ...BODY 1B 29 Fig 84 Body Mounting 06 Fig 85 Body Mounting 14 LIGHT DUTY TRUCK SERVICE MANUAL...
Page 171: ...LIGHT DUTY TRUCK SERVICE M A N U A L Fig 2 Frame Horizontal Checking Typical FRAME 2 3...
Page 173: ...LIGHT DUTY TRUCK SERVICE M A N U A L Fig 4 10 30 Series Truck Frame FRAME 2 5...
Page 174: ...2 6 FRAME LIGHT DUTY TRUCK SERVICE MANUAL Fig 5 Underbody Reference Points G Van...
Page 185: ...FRONT SUSPENSION 3 11 Fig 16 Toe out on Turns LIGHT DUTY TRUCK SERVICE MANUAL...
Page 224: ......
Page 266: ......
Page 351: ...ENGINE 6 15 Fig ID Sectional View of Eight Cylinder Engine LIGHT DUTY TRUCK SERVICE MANUAL...
Page 375: ...EN G IN E 6 39 LIGHT DUTY TRUCK SERVICE MANUAL...
Page 376: ...6 4 0 ENGINE LIGHT DUTY TRUCK SERVICE MANUAL...
Page 377: ...ENG IN E 6 41 LIGHT DUTY TRUCK SERVICE MANUAL...
Page 378: ...LIGHT DUTY TRUCK SERVICE MANUAL Fig 37L K Series Engine Front Mount 6 42 ENG INE...
Page 400: ...6 6 4 ENG INE LIGHT DUTY TRUCK SERVICE MANUAL...
Page 401: ...ENG IN E 6 65 LIGHT DUTY TRUCK SERVICE MANUAL...
Page 402: ...6 6 6 ENGINE LIGHT DUTY TRUCK SERVICE MANUAL...
Page 403: ...E NG IN E 6 67 Fig 36V C Series Engine Mounts LIGHT DUTY TRUCK SERVICE MANUAL...
Page 410: ......
Page 423: ...EN G IN E C OOLING 6K 13 Fig 16 Overheating Chart LIGHT DUTY TRUCK SERVICE MANUAL...
Page 424: ...6 K 1 4 ENG INE COOLING Fig 17 Coolant Loss Chart LIGHT DUTY TRUCK SERVICE MANUAL...
Page 456: ...6M 32 ENGINE FUEL Fig K15 Accelerator Controls G Van L 6 LIGHT DUTY TRUCK SERVICE MANUAL...
Page 492: ......
Page 512: ...Fig 18e Vacuum Advance Diagram V8 Engine...
Page 516: ...6 T 2 4 E M IS S IO N CONTROL SYSTEMS LIGHT DUTY TRUCK SERVICE MANUAL...
Page 528: ......
Page 590: ......
Page 593: ...CLUTCHES MANUAL TRANSMISSIONS 7M 3 LIGHT DUTY TRUCK SERVICE MANUAL...
Page 598: ...7M 8 CLUTCHES MANUAL TRANSMISSIONS LIGHT DUTY TRUCK SERVICE MANUAL...
Page 642: ......
Page 654: ......
Page 743: ...FUEL TANKS AND EXHAUST 8 13 LIGHT DUTY TRUCK SERVICE MANUAL...
Page 744: ...8 14 FUEL TANKS AND EXHAUST LIGHT DUTY TRUCK SERVICE MANUAL...
Page 760: ...8 30 FUEL TANKS AND EXHAUST Fig 40 Exhaust Pipe P Models LIGHT DUTY TRUCK SERVICE MANUAL...
Page 761: ...FUEL TANKS AND EXHAUST 8 31 LIGHT DUTY TRUCK SERVICE MANUAL...
Page 763: ...FUEL TANKS AND EXHAUST 8 33 LIGHT DUTY TRUCK SERVICE MANUAL...
Page 766: ......
Page 832: ...LIGHT DUTY TRUCK SERVICE MANUAL Fig 106 Power Steering Pump Mounting Typical 9 66 STEERING...
Page 833: ...PUMP ASSEMBLY STEERING GEAR TYPICAL SMALL V8 TYPICAL LARGE V8 STEERING 9 67...
Page 861: ...STEERING 9 95 Fig 134 Power Steering Pump Leakage LIGHT DUTY TRUCK SERVICE MANUAL...
Page 864: ......
Page 876: ......
Page 886: ...11 10 CHASSIS SHEET METAL LIGHT DUTY TRUCK SERVICE MANUAL...
Page 891: ...ELECTRICAL BODY AND CHASSIS 12 5 LIGHT DUTY TRUCK SERVICE MANUAL...
Page 934: ......
Page 942: ......
Page 970: ......
Page 972: ......
Page 974: ......
Page 976: ...V...
Page 978: ......
Page 979: ......