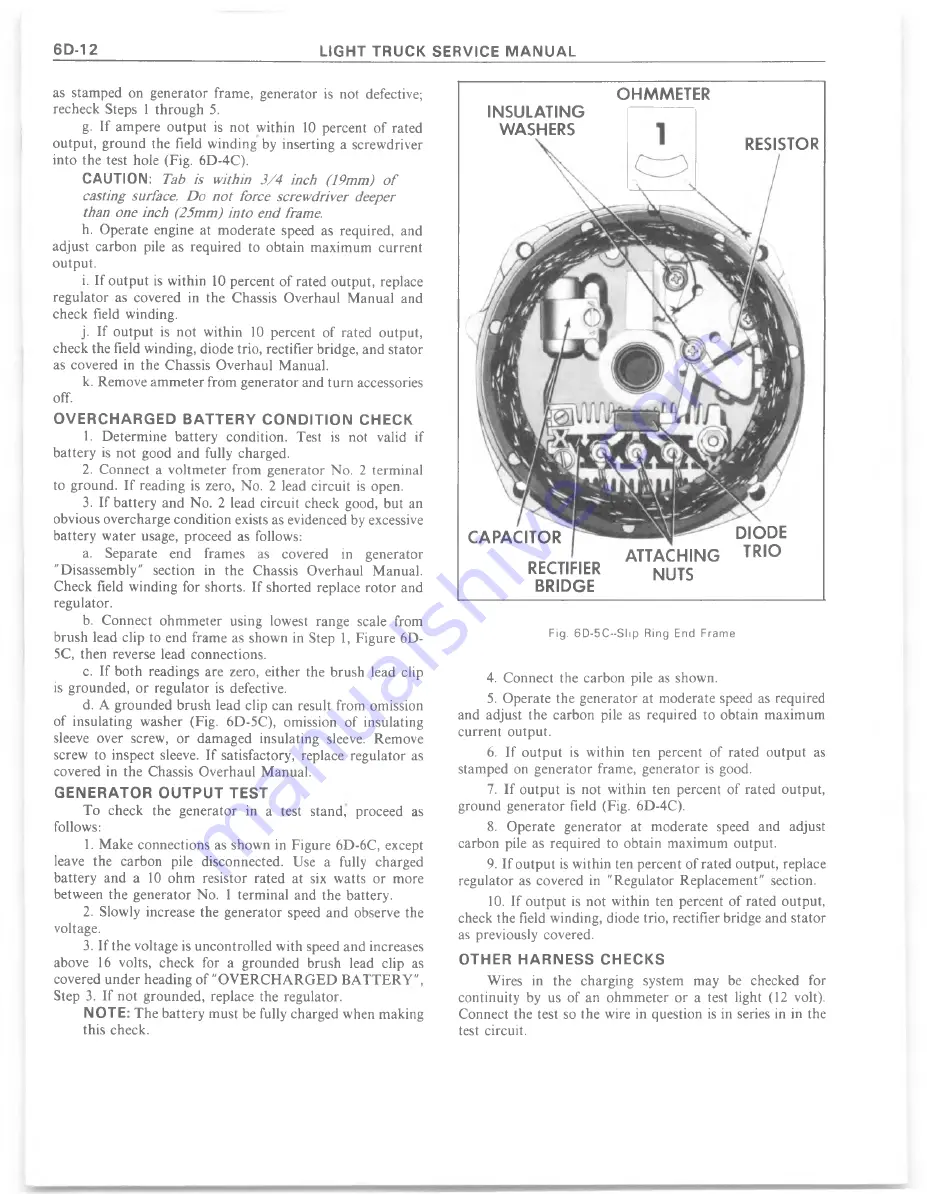
as stamped on generator frame, generator is not defective;
recheck Steps l through 5.
g. If ampere output is not within 10 percent of rated
output, ground the field winding by inserting a screwdriver
into the test hole (Fig. 6D-4C).
CAUTION:
Tab is within 3 /4 inch (19m m ) o f
casting surface. D o n o t force screwdriver deeper
than one inch (25m m ) into end frame.
h. O perate engine at m oderate speed as required, and
adjust carbon pile as required to obtain maximum current
output.
i. If output is within 10 percent of rated output, replace
regulator as covered in the Chassis Overhaul M anual and
check field winding.
j. If output is not within 10 percent of rated output,
check the field winding, diode trio, rectifier bridge, and stator
as covered in the Chassis Overhaul Manual.
k. Remove am m eter from generator and turn accessories
off.
O V E R C H A R G E D B A T T E R Y C O N D I T I O N C H E C K
1. Determ ine battery condition. Test is not valid if
battery is not good and fully charged.
2. Connect a voltm eter from generator No. 2 term inal
to ground. If reading is zero, No. 2 lead circuit is open.
3. If battery and No. 2 lead circuit check good, but an
obvious overcharge condition exists as evidenced by excessive
battery w ater usage, proceed as follows:
a. Separate end frames as covered in generator
"Disassembly" section in the Chassis Overhaul Manual.
Check field winding for shorts. If shorted replace rotor and
regulator.
b. Connect ohm m eter using lowest range scale from
brush lead clip to end frame as shown in Step 1, Figure 6D-
5C, then reverse lead connections.
c. If both readings are zero, either the brush lead clip
is grounded, or regulator is defective.
d. A grounded brush lead clip can result from omission
of insulating washer (Fig. 6D-5C), omission of insulating
sleeve over screw, or damaged insulating sleeve. Remove
screw to inspect sleeve. If satisfactory, replace regulator as
covered in the Chassis O verhaul Manual.
G E N E R A T O R O U T P U T T E S T
To check the generator in a test stand, proceed as
follows:
1. Make connections as shown in Figure 6D-6C, except
leave the carbon pile disconnected. Use a fully charged
battery and a 10 ohm resistor rated at six watts or more
between the generator No. 1 term inal and the battery.
2. Slowly increase the generator speed and observe the
voltage.
3. If the voltage is uncontrolled with speed and increases
above 16 volts, check for a grounded brush lead clip as
covered under heading of "O V E R C H A R G E D BA TTERY ",
Step 3. If not grounded, replace the regulator.
NO TE:
The battery must be fully charged when making
this check.
Fig. 6 D -5 C -S lip Ring End Frame
4. Connect the carbon pile as shown.
5. Operate the generator at moderate speed as required
and adjust the carbon pile as required to obtain maximum
current output.
6. If output is within ten percent of rated output as
stamped on generator frame, generator is good.
7. If output is not within ten percent of rated output,
ground generator field (Fig. 6D-4C).
8. O perate generator at m oderate speed and adjust
carbon pile as required to obtain maximum output.
9. If output is within ten percent of rated output, replace
regulator as covered in "Regulator Replacement" section.
10. If output is not within ten percent of rated output,
check the field winding, diode trio, rectifier bridge and stator
as previously covered.
O T H E R H A R N E S S C H E C K S
Wires in the charging system may be checked for
continuity by us of an ohm m eter or a test light (12 volt).
Connect the test so the wire in question is in series in in the
test circuit.
CAPACITOR
RECTIFIER
BRIDGE
DIODE
ATTACHING
TRI°
NUTS
INSULATING
WASHERS
OHMMETER
RESISTOR
Summary of Contents for 1977 light duty truck
Page 1: ......
Page 28: ......
Page 70: ...Fig IB 24 Four Season System Vacuum Diagram C K Models 1B 24 LIGHT TRUCK SERVICE M A N U A L...
Page 71: ...Fig lB 25 Overhead System Wiring Diagram C K Models AIR C O N D ITIO N IN G 1 B 2 5...
Page 72: ...Fig IB 26 C60 System Wiring Diagram G Models...
Page 74: ......
Page 75: ...Fig lB 29 Motor Home Chassis Wiring Diagram THERMOSTATIC SWITCH AIR C O N D ITIO N IN G IB 2 9...
Page 106: ......
Page 128: ......
Page 129: ...Fig 2D 5 Typical 05 and 0 6 Vans...
Page 136: ......
Page 148: ...Fig 2D 51 Rear Door Controls...
Page 158: ...Fig 2D 79 Folding Top Assembly...
Page 159: ...Fig 2D 80 Folding Top Side Moldings and Header...
Page 161: ...Fig 2D 85 Dnver s Bucket Seat 14 Fig 2D 86 Passenger s Bucket Seat 14...
Page 162: ...Fig 2D 89 Rear Folding Seat 06 Fig 2D 9 0 Rear Bench Seat 14...
Page 163: ......
Page 164: ......
Page 165: ......
Page 185: ......
Page 186: ......
Page 190: ......
Page 225: ......
Page 226: ......
Page 248: ...Fig 3B 77 Removing Bearing Housing Pivot Pins Fig 3B 79 Replacing Lock Bolt Spring...
Page 278: ...C 10 G 10 20 C 20 30 G 30 P 10 30 9 Fig 3C l Front Suspension C P Series...
Page 284: ...BALL JOINT DIAGNOSTIC PROCEDURE...
Page 316: ......
Page 321: ...Fig 3D 12 Rear Spring Installation G Models...
Page 322: ......
Page 325: ......
Page 326: ......
Page 336: ......
Page 352: ......
Page 378: ......
Page 395: ...Fig 5 2 Front Brake Pipes and Hoses C K Models...
Page 396: ......
Page 397: ...Fig 5 4 Front Brake Pipes and Hoses P Models BRAKES 5 1 3...
Page 400: ......
Page 401: ...V 8 N 4 0 L 6 N 4 0...
Page 402: ......
Page 404: ......
Page 405: ...P300 42 M40 JB9...
Page 438: ......
Page 448: ...Fig 6A 4 P Series Engine Rear Mount...
Page 451: ...Fig 6A 8 K Series Engine Rear Mount...
Page 452: ...ENGINE M O U N T BRACKET ALL K SERIES W ITH L 6 ENGINE 6A14 LIGHT TRUCK SERVICE M A N U A L...
Page 483: ...FUEL PUMP PUSH ROD OILING OIL F LTER AND BY PASS VALVE...
Page 484: ...FUEL PUMP PUSH ROD OILING CRANKCASE AND CRANKSHAFT OILING VALVE MECHANISM OILING...
Page 487: ......
Page 488: ...MOUNT VIEW A V AUTOMATIC TRANSMISSION FRONT MANUAL TRANSMISSION...
Page 489: ......
Page 490: ......
Page 568: ......
Page 602: ......
Page 605: ......
Page 612: ...Fig 6D 3i High Energy Ignition Basic W iring...
Page 644: ......
Page 648: ...DISTRIBUTOR VALVE Fig 6E 3 Vacuum Hose Schematic L6 292 CID Calif HD Emissions...
Page 649: ...V A LV E Fig 6E 5 Vacuum Hose Schematic V8 305 CID HD Emissions...
Page 650: ...Fig 6E 7 Vacuum Hose Schematic V8 350 CID High Altitude Calif LD Emissions...
Page 651: ...VALVE Fig 6E 9 Vacuum Hose Schematic V8 350 400 CID Except Calif HD Emissions...
Page 652: ...CANISTER...
Page 653: ...PCV V AL VE Fig 6E 13 Vacuum Hose Schematic V8 454 CID Except Calif HD Emissions...
Page 672: ...Fig 6E 29 Air Cleaner 305 350 400 V8 CK...
Page 682: ......
Page 692: ......
Page 700: ...Fig 7A 6B Detent Downshift Cable C K and P Series...
Page 709: ...Fig 7 A 12B CBC 350 Hydraulic Circuit A U TO M A T IC T R A N S M IS S IO N 7 A 1 7...
Page 743: ...VIEW B FLAT IvEwfDl l6 G tO 2 GAGE...
Page 744: ......
Page 755: ...V I E W B WITH AUTOMATIC TRANSMISSION WITH MANUAL TRANSMISSION V I E W A...
Page 760: ...r...
Page 766: ......
Page 767: ...V I E W D 1 6 ENGINE VIEW V 8 ENGINE...
Page 768: ......
Page 775: ......
Page 788: ......
Page 794: ...G A S G A U G E...
Page 805: ......
Page 836: ...Fig 8 58 Seat Belt Reminder System Schematic...
Page 844: ...C H E C K n...
Page 852: ......
Page 853: ...SPECIAL TOOLS J 2 3 5 2 0...