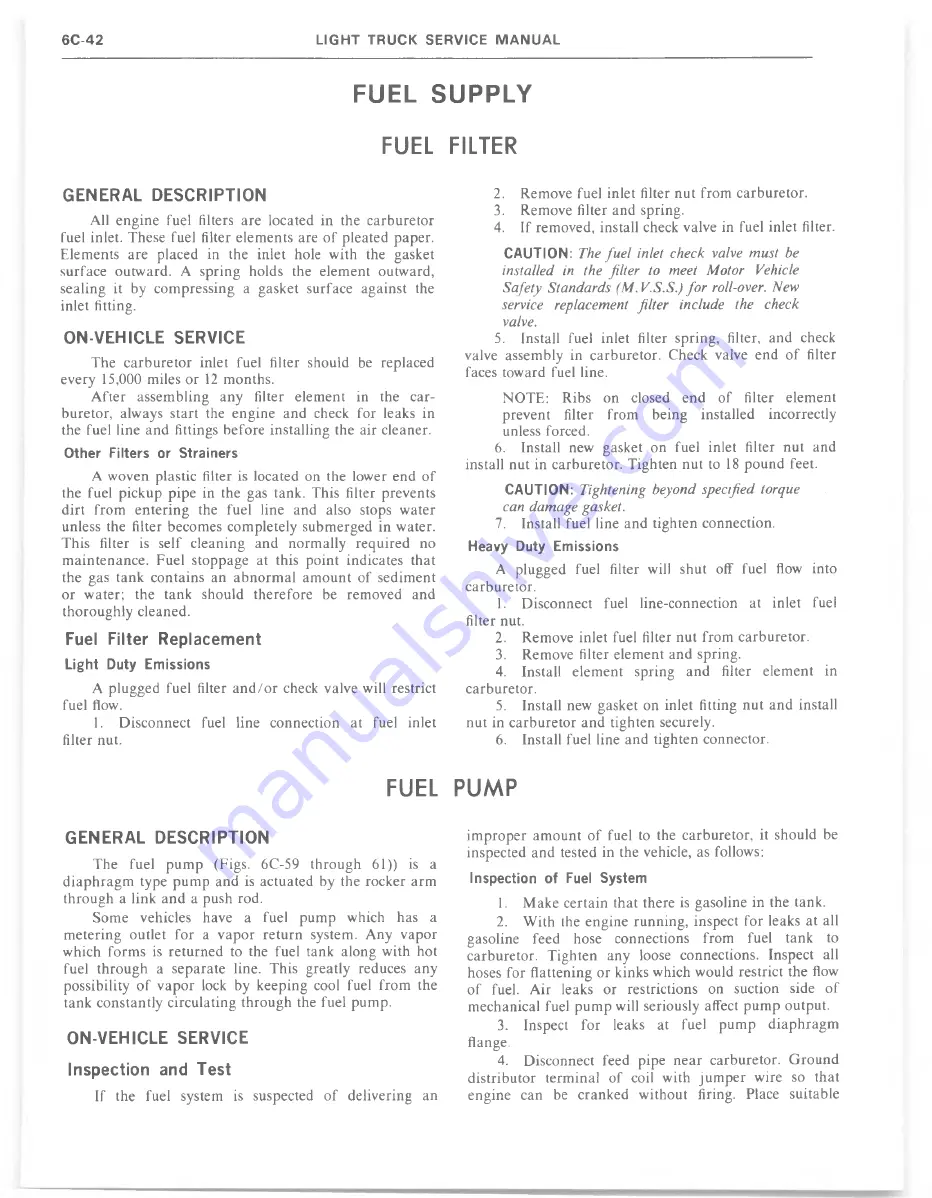
FUEL S U P P LY
FUEL FILTER
GEN ER A L D E S C R IP T IO N
All en g in e fuel filters are located in the carburetor
fuel inlet. These fuel filter elem ents are o f pleated paper.
Elements are placed in the inlet hole with the gasket
surface outw ard. A spring holds the elem ent outward,
sealing it by com pressing a gasket surface against the
inlet fitting.
O N-VEHICLE SERVICE
The ca rb u re to r inlet fuel filter should be replaced
every 15,000 miles or 12 months.
A fter assem bling any filter ele m ent in the car
buretor, always start the engine and check for leaks in
the fuel line and fittings before installing the air cleaner.
Other Filters or Strainers
A woven plastic filter is located on the lower end o f
the fuel pickup pipe in the gas tank. This filter prevents
dirt from e n te rin g the fuel line and also stops water
unless the filter becomes completely subm erged in water.
This filter is self cleaning and norm ally required no
m ain ten an ce. Fuel stoppage at this point indicates that
the gas tan k contains an a b n o rm a l a m o u n t o f sedim ent
or water; the tank should therefore be removed and
thoroughly cleaned.
Fuel Filter R eplacem ent
Light Duty Emissions
A plugged fuel filter a n d / o r check valve will restrict
fuel flow.
1.
Disconnect fuel line connection at fuel inlet
filter nut.
2.
Remove fuel inlet filter nut from carburetor.
3.
Remove filter and spring.
4.
If removed, install check valve in fuel inlet filter.
CAUTION:
The fu e l inlet check valve m ust be
installed in the filter to meet M otor Vehicle
S a fety Standards (M. V.S.S.) f o r roll-over. New
service replacement filte r include the check
valve.
5.
Install fuel inlet filter spring, filter, and check
valve assembly in carburetor. Check valve end o f filter
faces toward fuel line.
N OTE: Ribs on closed end o f filter element
prevent filter from being installed incorrectly
unless forced.
6.
Install new gasket on fuel inlet filter nut and
install nut in carburetor. Tighten nut to 18 pound feet.
CAUTION:
Tightening beyond specified torque
can dam age gasket.
7.
Install fuel line and tighten connection.
Heavy Duty Emissions
A plugged fuel filter will shut off fuel flow into
carburetor.
1.
Disconnect fuel line-connection at inlet fuel
filter nut.
2.
Remove inlet fuel filter nut from carburetor.
3.
Remove filter element and spring.
4.
Install elem ent spring an d filter elem ent in
carburetor.
5.
Install new gasket on inlet fitting nut and install
nut in c arburetor and tighten securely.
6.
Install fuel line and tighten connector.
FUEL
G E N ER A L D E S C R IP T IO N
T he fuel p u m p (Figs. 6C-59 through 61)) is a
d i a p h r a g m type p u m p and is actuated by the rocker arm
through a link an d a push rod.
Som e vehicles have a fuel pu m p which has a
m etering outlet for a vap o r retu rn system. A ny vapor
which form s is returned to the fuel tank along with hot
fuel th ro u g h a separate line. This greatly reduces any
possibility o f v a p o r lock by keeping cool fuel from the
tank constantly circulating thro u g h the fuel pump.
O N -VEH IC LE SERVICE
Inspection and Test
If the fuel system is suspected o f delivering an
PUMP
im p ro p e r a m o u n t o f fuel to the carburetor, it should be
inspected and tested in the vehicle, as follows:
Inspection of Fuel System
1.
M ake certain that there is gasoline in the tank.
2.
W ith the engine running, inspect for leaks at all
gasoline feed hose connections from fuel tank to
carburetor. Tighten any loose connections. Inspect all
hoses for flattening or kinks which would restrict the flow
o f fuel. A ir leaks or restrictions on suction side o f
mechanical fuel p u m p will seriously affect p u m p output.
3.
Inspect for leaks at fuel p u m p d ia p h ra g m
flange.
4.
Disconnect feed pipe n e a r carburetor. G ro u n d
d istributor te rm inal o f coil with ju m p e r wire so that
engine can be cranked without firing. Place suitable
Summary of Contents for 1977 light duty truck
Page 1: ......
Page 28: ......
Page 70: ...Fig IB 24 Four Season System Vacuum Diagram C K Models 1B 24 LIGHT TRUCK SERVICE M A N U A L...
Page 71: ...Fig lB 25 Overhead System Wiring Diagram C K Models AIR C O N D ITIO N IN G 1 B 2 5...
Page 72: ...Fig IB 26 C60 System Wiring Diagram G Models...
Page 74: ......
Page 75: ...Fig lB 29 Motor Home Chassis Wiring Diagram THERMOSTATIC SWITCH AIR C O N D ITIO N IN G IB 2 9...
Page 106: ......
Page 128: ......
Page 129: ...Fig 2D 5 Typical 05 and 0 6 Vans...
Page 136: ......
Page 148: ...Fig 2D 51 Rear Door Controls...
Page 158: ...Fig 2D 79 Folding Top Assembly...
Page 159: ...Fig 2D 80 Folding Top Side Moldings and Header...
Page 161: ...Fig 2D 85 Dnver s Bucket Seat 14 Fig 2D 86 Passenger s Bucket Seat 14...
Page 162: ...Fig 2D 89 Rear Folding Seat 06 Fig 2D 9 0 Rear Bench Seat 14...
Page 163: ......
Page 164: ......
Page 165: ......
Page 185: ......
Page 186: ......
Page 190: ......
Page 225: ......
Page 226: ......
Page 248: ...Fig 3B 77 Removing Bearing Housing Pivot Pins Fig 3B 79 Replacing Lock Bolt Spring...
Page 278: ...C 10 G 10 20 C 20 30 G 30 P 10 30 9 Fig 3C l Front Suspension C P Series...
Page 284: ...BALL JOINT DIAGNOSTIC PROCEDURE...
Page 316: ......
Page 321: ...Fig 3D 12 Rear Spring Installation G Models...
Page 322: ......
Page 325: ......
Page 326: ......
Page 336: ......
Page 352: ......
Page 378: ......
Page 395: ...Fig 5 2 Front Brake Pipes and Hoses C K Models...
Page 396: ......
Page 397: ...Fig 5 4 Front Brake Pipes and Hoses P Models BRAKES 5 1 3...
Page 400: ......
Page 401: ...V 8 N 4 0 L 6 N 4 0...
Page 402: ......
Page 404: ......
Page 405: ...P300 42 M40 JB9...
Page 438: ......
Page 448: ...Fig 6A 4 P Series Engine Rear Mount...
Page 451: ...Fig 6A 8 K Series Engine Rear Mount...
Page 452: ...ENGINE M O U N T BRACKET ALL K SERIES W ITH L 6 ENGINE 6A14 LIGHT TRUCK SERVICE M A N U A L...
Page 483: ...FUEL PUMP PUSH ROD OILING OIL F LTER AND BY PASS VALVE...
Page 484: ...FUEL PUMP PUSH ROD OILING CRANKCASE AND CRANKSHAFT OILING VALVE MECHANISM OILING...
Page 487: ......
Page 488: ...MOUNT VIEW A V AUTOMATIC TRANSMISSION FRONT MANUAL TRANSMISSION...
Page 489: ......
Page 490: ......
Page 568: ......
Page 602: ......
Page 605: ......
Page 612: ...Fig 6D 3i High Energy Ignition Basic W iring...
Page 644: ......
Page 648: ...DISTRIBUTOR VALVE Fig 6E 3 Vacuum Hose Schematic L6 292 CID Calif HD Emissions...
Page 649: ...V A LV E Fig 6E 5 Vacuum Hose Schematic V8 305 CID HD Emissions...
Page 650: ...Fig 6E 7 Vacuum Hose Schematic V8 350 CID High Altitude Calif LD Emissions...
Page 651: ...VALVE Fig 6E 9 Vacuum Hose Schematic V8 350 400 CID Except Calif HD Emissions...
Page 652: ...CANISTER...
Page 653: ...PCV V AL VE Fig 6E 13 Vacuum Hose Schematic V8 454 CID Except Calif HD Emissions...
Page 672: ...Fig 6E 29 Air Cleaner 305 350 400 V8 CK...
Page 682: ......
Page 692: ......
Page 700: ...Fig 7A 6B Detent Downshift Cable C K and P Series...
Page 709: ...Fig 7 A 12B CBC 350 Hydraulic Circuit A U TO M A T IC T R A N S M IS S IO N 7 A 1 7...
Page 743: ...VIEW B FLAT IvEwfDl l6 G tO 2 GAGE...
Page 744: ......
Page 755: ...V I E W B WITH AUTOMATIC TRANSMISSION WITH MANUAL TRANSMISSION V I E W A...
Page 760: ...r...
Page 766: ......
Page 767: ...V I E W D 1 6 ENGINE VIEW V 8 ENGINE...
Page 768: ......
Page 775: ......
Page 788: ......
Page 794: ...G A S G A U G E...
Page 805: ......
Page 836: ...Fig 8 58 Seat Belt Reminder System Schematic...
Page 844: ...C H E C K n...
Page 852: ......
Page 853: ...SPECIAL TOOLS J 2 3 5 2 0...