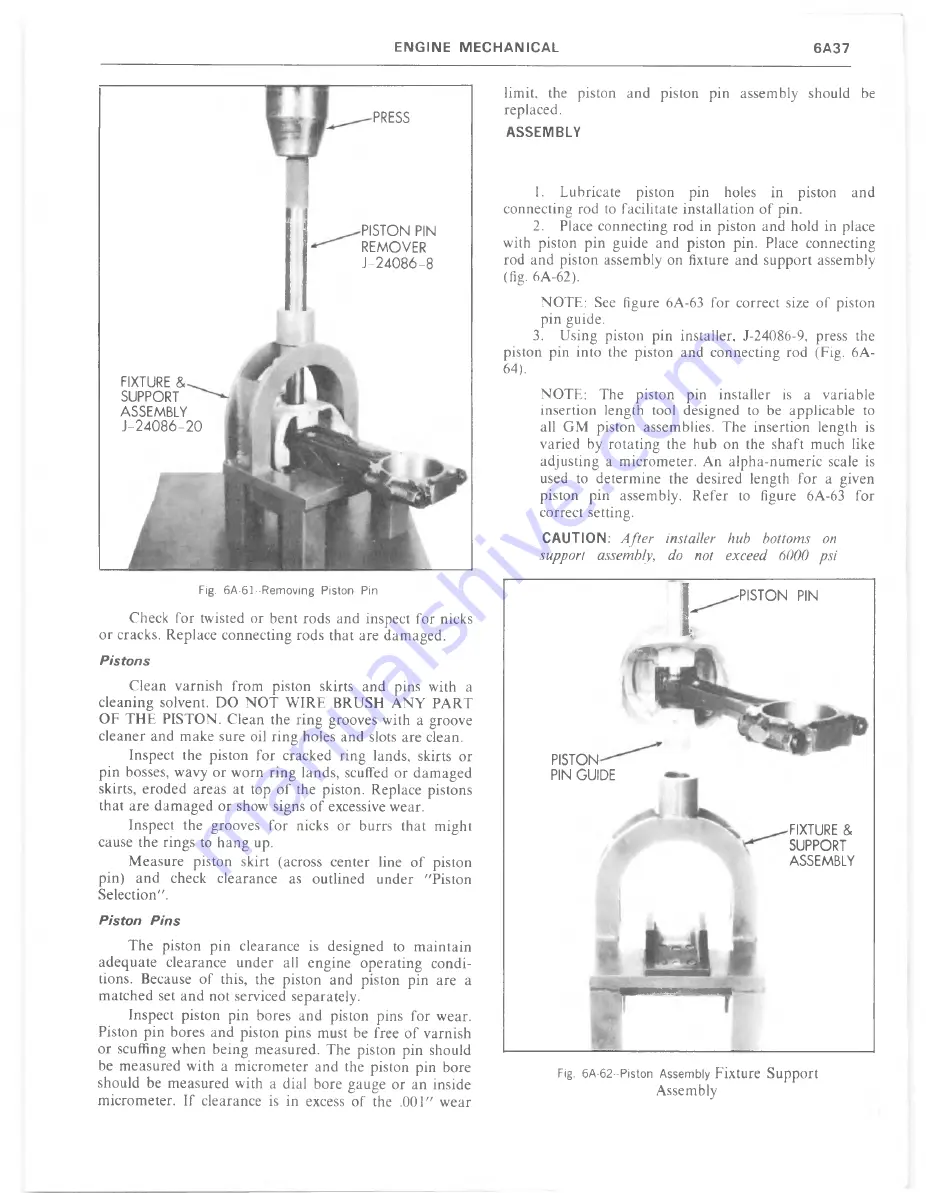
PRESS
PISTON PIN
REMOVER
J - 2 4 0 8 6 - 8
Fig. 6A-61--F?emoving Piston Pin
Check for twisted or bent rods and inspect for nicks
o r cracks. Replace connecting rods that are dam aged.
Pistons
Clean varnish from piston skirts and pins with a
cleaning solvent. DO N O T W IR E BRUSH A N Y P A R T
O F T H E PISTON. Clean the ring grooves with a groove
cleaner and m ake sure oil ring holes and slots are clean.
Inspect the piston for cracked ring lands, skirts or
pin bosses, wavy or w orn ring lands, scuffed or dam ag ed
skirts, eroded areas at top o f the piston. Replace pistons
th at are d a m a g e d o r show signs o f excessive wear.
Inspect the grooves for nicks or burrs that might
cause the rings to h an g up.
M easure piston skirt (across center line o f piston
pin) and check clearance as outlined u nder "Piston
Selection".
Piston Pins
T h e piston pin clearance is designed to m aintain
a d e q u a te clearance u n d e r all engine operatin g condi
tions. Because o f this, the piston and piston p in are a
m atched set and not serviced separately.
Inspect piston pin bores and piston pins for wear.
Piston p in bores an d piston pins must be free o f varnish
o r scuffing w h en being m easured. The piston pin should
be m easured with a m icrom eter and the piston pin bore
should be m easured with a dial bore gauge or an inside
m icrom eter. If clearance is in excess o f the .001" w ear
limit, the piston an d piston pin assembly should be
replaced.
ASSEMBLY
1.
Lubricate
piston pin
holes in piston
and
connecting rod to facilitate installation o f pin.
2.
Place connecting rod in piston and hold in place
with piston pin guide and piston pin. Place connecting
rod and piston assembly on fixture and support assembly
(fig. 6A-62).
N O TE: See figure 6A-63 for correct size o f piston
pin guide.
3.
Using piston pin installer, J-24086-9, press the
piston pin into the piston and connecting rod (Fig. 6A-
64).
N O TE: The piston pin installer is a variable
insertion length tool designed to be applicable to
all G M piston assemblies. The insertion length is
varied by rotatin g the hub on the shaft much like
adjusting a micrometer. An alpha-num eric scale is
used to d eterm ine the desired length for a given
piston pin assembly. R efer to figure 6A-63 for
correct setting.
CAUTION.
A fte r installer hub bottoms on
support assembly, do not exceed 6000 psi
I-
-PISTON PIN
4fI
PISTON
PIN GUIDE
FIXTURE &
SUPPORT
ASSEMBLY
FIXTURE &
SUPPORT
ASSEMBLY
J - 2 4 0 8 6 - 2 0
Summary of Contents for 1977 light duty truck
Page 1: ......
Page 28: ......
Page 70: ...Fig IB 24 Four Season System Vacuum Diagram C K Models 1B 24 LIGHT TRUCK SERVICE M A N U A L...
Page 71: ...Fig lB 25 Overhead System Wiring Diagram C K Models AIR C O N D ITIO N IN G 1 B 2 5...
Page 72: ...Fig IB 26 C60 System Wiring Diagram G Models...
Page 74: ......
Page 75: ...Fig lB 29 Motor Home Chassis Wiring Diagram THERMOSTATIC SWITCH AIR C O N D ITIO N IN G IB 2 9...
Page 106: ......
Page 128: ......
Page 129: ...Fig 2D 5 Typical 05 and 0 6 Vans...
Page 136: ......
Page 148: ...Fig 2D 51 Rear Door Controls...
Page 158: ...Fig 2D 79 Folding Top Assembly...
Page 159: ...Fig 2D 80 Folding Top Side Moldings and Header...
Page 161: ...Fig 2D 85 Dnver s Bucket Seat 14 Fig 2D 86 Passenger s Bucket Seat 14...
Page 162: ...Fig 2D 89 Rear Folding Seat 06 Fig 2D 9 0 Rear Bench Seat 14...
Page 163: ......
Page 164: ......
Page 165: ......
Page 185: ......
Page 186: ......
Page 190: ......
Page 225: ......
Page 226: ......
Page 248: ...Fig 3B 77 Removing Bearing Housing Pivot Pins Fig 3B 79 Replacing Lock Bolt Spring...
Page 278: ...C 10 G 10 20 C 20 30 G 30 P 10 30 9 Fig 3C l Front Suspension C P Series...
Page 284: ...BALL JOINT DIAGNOSTIC PROCEDURE...
Page 316: ......
Page 321: ...Fig 3D 12 Rear Spring Installation G Models...
Page 322: ......
Page 325: ......
Page 326: ......
Page 336: ......
Page 352: ......
Page 378: ......
Page 395: ...Fig 5 2 Front Brake Pipes and Hoses C K Models...
Page 396: ......
Page 397: ...Fig 5 4 Front Brake Pipes and Hoses P Models BRAKES 5 1 3...
Page 400: ......
Page 401: ...V 8 N 4 0 L 6 N 4 0...
Page 402: ......
Page 404: ......
Page 405: ...P300 42 M40 JB9...
Page 438: ......
Page 448: ...Fig 6A 4 P Series Engine Rear Mount...
Page 451: ...Fig 6A 8 K Series Engine Rear Mount...
Page 452: ...ENGINE M O U N T BRACKET ALL K SERIES W ITH L 6 ENGINE 6A14 LIGHT TRUCK SERVICE M A N U A L...
Page 483: ...FUEL PUMP PUSH ROD OILING OIL F LTER AND BY PASS VALVE...
Page 484: ...FUEL PUMP PUSH ROD OILING CRANKCASE AND CRANKSHAFT OILING VALVE MECHANISM OILING...
Page 487: ......
Page 488: ...MOUNT VIEW A V AUTOMATIC TRANSMISSION FRONT MANUAL TRANSMISSION...
Page 489: ......
Page 490: ......
Page 568: ......
Page 602: ......
Page 605: ......
Page 612: ...Fig 6D 3i High Energy Ignition Basic W iring...
Page 644: ......
Page 648: ...DISTRIBUTOR VALVE Fig 6E 3 Vacuum Hose Schematic L6 292 CID Calif HD Emissions...
Page 649: ...V A LV E Fig 6E 5 Vacuum Hose Schematic V8 305 CID HD Emissions...
Page 650: ...Fig 6E 7 Vacuum Hose Schematic V8 350 CID High Altitude Calif LD Emissions...
Page 651: ...VALVE Fig 6E 9 Vacuum Hose Schematic V8 350 400 CID Except Calif HD Emissions...
Page 652: ...CANISTER...
Page 653: ...PCV V AL VE Fig 6E 13 Vacuum Hose Schematic V8 454 CID Except Calif HD Emissions...
Page 672: ...Fig 6E 29 Air Cleaner 305 350 400 V8 CK...
Page 682: ......
Page 692: ......
Page 700: ...Fig 7A 6B Detent Downshift Cable C K and P Series...
Page 709: ...Fig 7 A 12B CBC 350 Hydraulic Circuit A U TO M A T IC T R A N S M IS S IO N 7 A 1 7...
Page 743: ...VIEW B FLAT IvEwfDl l6 G tO 2 GAGE...
Page 744: ......
Page 755: ...V I E W B WITH AUTOMATIC TRANSMISSION WITH MANUAL TRANSMISSION V I E W A...
Page 760: ...r...
Page 766: ......
Page 767: ...V I E W D 1 6 ENGINE VIEW V 8 ENGINE...
Page 768: ......
Page 775: ......
Page 788: ......
Page 794: ...G A S G A U G E...
Page 805: ......
Page 836: ...Fig 8 58 Seat Belt Reminder System Schematic...
Page 844: ...C H E C K n...
Page 852: ......
Page 853: ...SPECIAL TOOLS J 2 3 5 2 0...