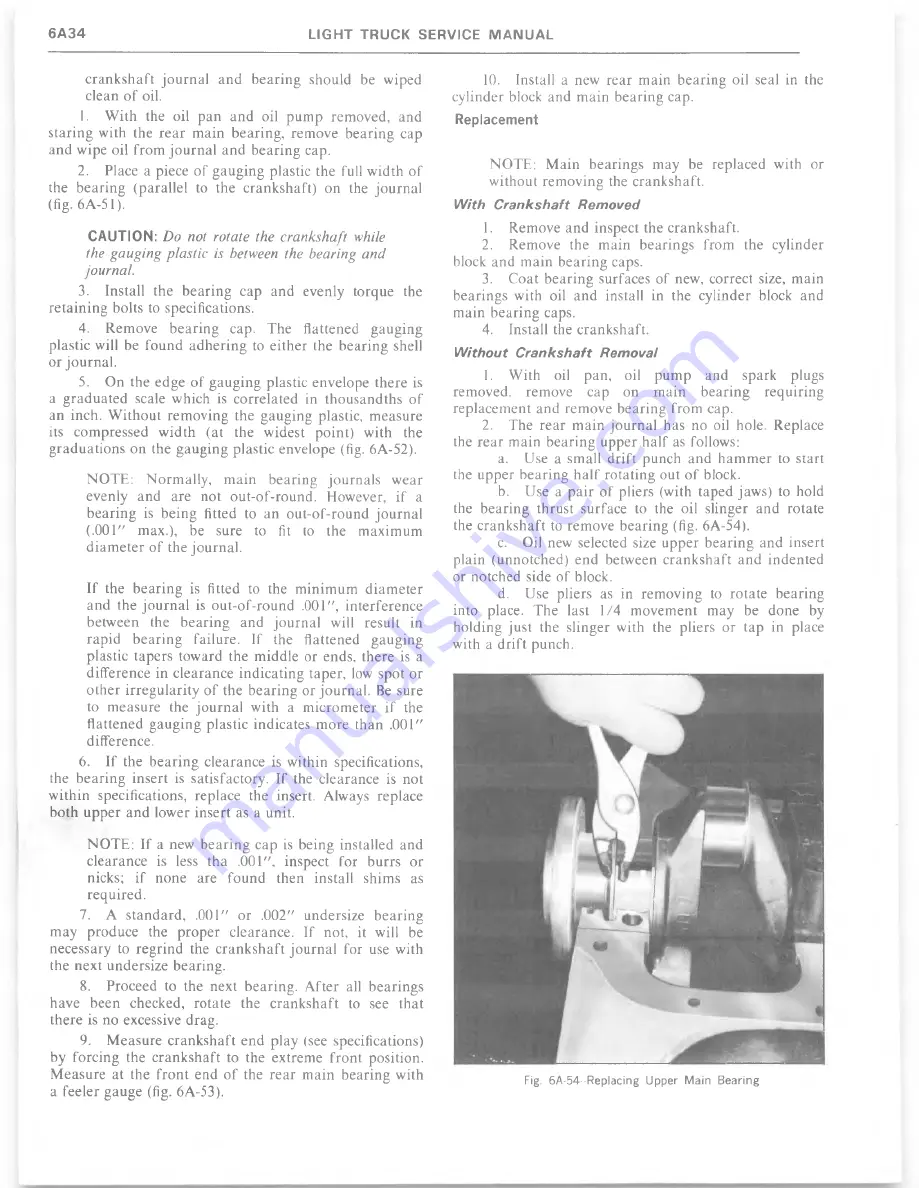
c ra n k sh a ft jo u rn a l and bearing should be wiped
clean o f oil.
1.
W ith the oil pan an d oil p u m p removed, and
staring with the re a r m ain bearing, remove bearing cap
and wipe oil from jo u r n a l and bearing cap.
2.
Place a piece o f g auging plastic the full w idth o f
the b earin g (parallel to the crankshaft) on the jo u rn al
(fig. 6A-51).
CAUTION:
Do not rotate the crankshaft while
the gauging plastic is between the bearing and
journal.
3.
Install the bearing cap and evenly torque the
retaining bolts to specifications.
4.
Remove b earin g cap. The flattened gauging
plastic will be fo und a d h e rin g to either the bearing shell
or jou rn al.
5.
On the edge o f gauging plastic envelope there is
a grad u ated scale which is correlated in thousandths o f
an inch. W ithout rem oving the gauging plastic, measure
its compressed w id th (at the widest point) with the
g rad u atio n s on the g auging plastic envelope (fig. 6A-52).
N O T E : N ormally, m ain bearing journals w ear
evenly and are not out-of-round. However, if a
b earin g is being fitted to an out-of-round jo u rn a l
(.001" max.), be sure to fit to the m axim um
d ia m e te r o f the journal.
If the b earin g is fitted to the m in im u m d iam eter
and the jo u rn a l is out-of-round .001", interference
between the bearing and jo u rn a l will result in
rapid bearing failure. If the flattened gauging
plastic tapers toward the middle or ends, there is a
difference in clearance indicating taper, low spot or
o ther irregularity o f the bearing or jou rn al. Be sure
to m easure the jo u rn a l with a m icrom eter if the
flattened gauging plastic indicates m ore than .001"
difference.
6.
If the b earin g clearance is within specifications,
the b earin g insert is satisfactory. If the clearance is not
within specifications, replace the insert. Always replace
b oth upp er and lower insert as a unit.
N O T E : If a new b earin g cap is being installed and
clearance is less tha .001", inspect for burrs or
nicks; if none are found then install shim s as
required.
7.
A standard, .001" or .002" undersize bearing
may produce the p ro p er clearance. If not, it will be
necessary to regrind the cra n k sh a ft jo u rn a l for use with
the next undersize bearing.
8.
Proceed to the next bearing. A fter all bearings
have been checked, rotate the c ra n k sh a ft to see that
there is no excessive drag.
9.
M easure crankshaft end play (see specifications)
by forcing the crankshaft to the extreme front position.
M easure at the fro n t end o f the re a r m ain bearing with
a feeler gauge (fig. 6A-53).
10.
Install a new rear main bearing oil seal in the
cylinder block and m ain bearing cap.
Replacement
N O TE: M ain bearings may be replaced with or
without rem oving the crankshaft.
W ith C rankshaft Removed
1.
Remove and inspect the crankshaft.
2.
Remove the m ain bearings from the cylinder
block and main bearing caps.
3.
Coat bearing surfaces of new, correct size, main
bearings with oil and install in the cylinder block and
m ain bearing caps.
4.
Install the crankshaft.
W ithout C ran ksh aft Removal
1.
With oil pan, oil p u m p and spark plugs
removed, remove cap on m ain bearing requiring
replacem ent and remove bearing from cap.
2.
The rear m ain journal has no oil hole. Replace
the rear main bearing upper half as follows:
a.
Use a small drift punch and h a m m e r to start
the upper bearing h a lf rotating out o f block.
b.
Use a pair o f pliers (with taped jaws) to hold
the bearing thrust surface to the oil slinger and rotate
the crankshaft to remove bearing (fig. 6A-54).
c.
Oil new selected size upper bearing and insert
plain (unnotched) end between crankshaft and indented
or notched side o f block.
d.
Use pliers as in rem oving to rotate bearing
into place. The last 1/4 movem ent may be done by
holding just the slinger with the pliers or tap in place
with a drift punch.
Summary of Contents for 1977 light duty truck
Page 1: ......
Page 28: ......
Page 70: ...Fig IB 24 Four Season System Vacuum Diagram C K Models 1B 24 LIGHT TRUCK SERVICE M A N U A L...
Page 71: ...Fig lB 25 Overhead System Wiring Diagram C K Models AIR C O N D ITIO N IN G 1 B 2 5...
Page 72: ...Fig IB 26 C60 System Wiring Diagram G Models...
Page 74: ......
Page 75: ...Fig lB 29 Motor Home Chassis Wiring Diagram THERMOSTATIC SWITCH AIR C O N D ITIO N IN G IB 2 9...
Page 106: ......
Page 128: ......
Page 129: ...Fig 2D 5 Typical 05 and 0 6 Vans...
Page 136: ......
Page 148: ...Fig 2D 51 Rear Door Controls...
Page 158: ...Fig 2D 79 Folding Top Assembly...
Page 159: ...Fig 2D 80 Folding Top Side Moldings and Header...
Page 161: ...Fig 2D 85 Dnver s Bucket Seat 14 Fig 2D 86 Passenger s Bucket Seat 14...
Page 162: ...Fig 2D 89 Rear Folding Seat 06 Fig 2D 9 0 Rear Bench Seat 14...
Page 163: ......
Page 164: ......
Page 165: ......
Page 185: ......
Page 186: ......
Page 190: ......
Page 225: ......
Page 226: ......
Page 248: ...Fig 3B 77 Removing Bearing Housing Pivot Pins Fig 3B 79 Replacing Lock Bolt Spring...
Page 278: ...C 10 G 10 20 C 20 30 G 30 P 10 30 9 Fig 3C l Front Suspension C P Series...
Page 284: ...BALL JOINT DIAGNOSTIC PROCEDURE...
Page 316: ......
Page 321: ...Fig 3D 12 Rear Spring Installation G Models...
Page 322: ......
Page 325: ......
Page 326: ......
Page 336: ......
Page 352: ......
Page 378: ......
Page 395: ...Fig 5 2 Front Brake Pipes and Hoses C K Models...
Page 396: ......
Page 397: ...Fig 5 4 Front Brake Pipes and Hoses P Models BRAKES 5 1 3...
Page 400: ......
Page 401: ...V 8 N 4 0 L 6 N 4 0...
Page 402: ......
Page 404: ......
Page 405: ...P300 42 M40 JB9...
Page 438: ......
Page 448: ...Fig 6A 4 P Series Engine Rear Mount...
Page 451: ...Fig 6A 8 K Series Engine Rear Mount...
Page 452: ...ENGINE M O U N T BRACKET ALL K SERIES W ITH L 6 ENGINE 6A14 LIGHT TRUCK SERVICE M A N U A L...
Page 483: ...FUEL PUMP PUSH ROD OILING OIL F LTER AND BY PASS VALVE...
Page 484: ...FUEL PUMP PUSH ROD OILING CRANKCASE AND CRANKSHAFT OILING VALVE MECHANISM OILING...
Page 487: ......
Page 488: ...MOUNT VIEW A V AUTOMATIC TRANSMISSION FRONT MANUAL TRANSMISSION...
Page 489: ......
Page 490: ......
Page 568: ......
Page 602: ......
Page 605: ......
Page 612: ...Fig 6D 3i High Energy Ignition Basic W iring...
Page 644: ......
Page 648: ...DISTRIBUTOR VALVE Fig 6E 3 Vacuum Hose Schematic L6 292 CID Calif HD Emissions...
Page 649: ...V A LV E Fig 6E 5 Vacuum Hose Schematic V8 305 CID HD Emissions...
Page 650: ...Fig 6E 7 Vacuum Hose Schematic V8 350 CID High Altitude Calif LD Emissions...
Page 651: ...VALVE Fig 6E 9 Vacuum Hose Schematic V8 350 400 CID Except Calif HD Emissions...
Page 652: ...CANISTER...
Page 653: ...PCV V AL VE Fig 6E 13 Vacuum Hose Schematic V8 454 CID Except Calif HD Emissions...
Page 672: ...Fig 6E 29 Air Cleaner 305 350 400 V8 CK...
Page 682: ......
Page 692: ......
Page 700: ...Fig 7A 6B Detent Downshift Cable C K and P Series...
Page 709: ...Fig 7 A 12B CBC 350 Hydraulic Circuit A U TO M A T IC T R A N S M IS S IO N 7 A 1 7...
Page 743: ...VIEW B FLAT IvEwfDl l6 G tO 2 GAGE...
Page 744: ......
Page 755: ...V I E W B WITH AUTOMATIC TRANSMISSION WITH MANUAL TRANSMISSION V I E W A...
Page 760: ...r...
Page 766: ......
Page 767: ...V I E W D 1 6 ENGINE VIEW V 8 ENGINE...
Page 768: ......
Page 775: ......
Page 788: ......
Page 794: ...G A S G A U G E...
Page 805: ......
Page 836: ...Fig 8 58 Seat Belt Reminder System Schematic...
Page 844: ...C H E C K n...
Page 852: ......
Page 853: ...SPECIAL TOOLS J 2 3 5 2 0...