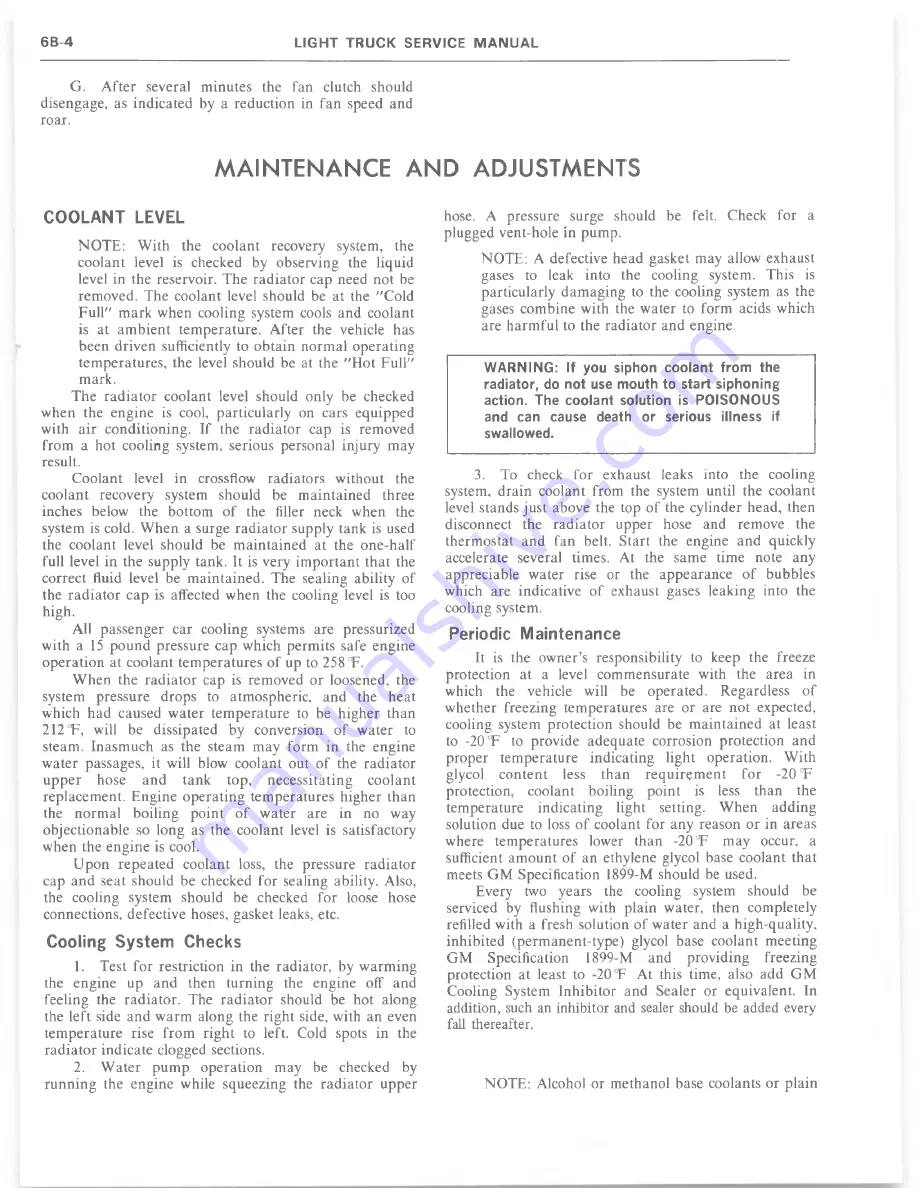
G.
A fter several m inutes the fan clutch should
disengage, as indicated by a reduction in fa n speed and
roar.
MAINTENANCE AND ADJUSTMENTS
C O O L A N T LEVEL
N O T E : W ith the coolant recovery system, the
coolant level is checked by observing the liquid
level in the reservoir. T h e ra d ia to r cap need not be
rem oved. The coolant level should be at the "C old
Full" m ark w hen cooling system cools and coolant
is at am b ie n t tem perature. A fter the vehicle has
been driven sufficiently to obtain n o rm al operating
te m peratures, the level should be at the "H o t Full"
mark.
T h e ra d ia to r coolant level should only be checked
w hen the engine is cool, particularly on cars equipped
with air conditioning. If the ra d ia to r cap is removed
from a hot cooling system, serious personal injury m ay
result.
Coolant level in crossflow radiators without the
coolant recovery system should be m ain tain ed three
inches below the bottom o f the filler neck w hen the
system is cold. W h e n a surge ra d ia to r supply tank is used
the coolant level should be m a in ta in e d at the one-half
full level in the supply tank. It is very im p o rtan t that the
correct fluid level be m aintained. T he sealing ability of
the ra d ia to r cap is affected w hen the cooling level is too
high.
All passenger car cooling systems are pressurized
with a 15 p o u n d pressure cap which perm its safe engine
o p e ra tio n at coolant tem p eratu res o f up to 258 °F.
W h e n the ra d ia to r cap is removed or loosened, the
system pressure drops to atmospheric, an d the heat
which had caused w ater tem p eratu re to be higher than
212°F, will be dissipated by conversion o f w ater to
steam. Inasm uch as the steam m ay form in the engine
w ater passages, it will blow coolant out o f the ra d iato r
u p p e r
hose
an d
ta n k
top,
n ecessitatin g coolant
replacem ent. Engine operatin g tem peratures higher than
the norm al boiling point o f w ater are in no way
objectionable so long as the coolant level is satisfactory
w hen the engine is cool.
Upon re p eated coolant loss, the pressure ra d iato r
cap an d seat should be checked for sealing ability. Also,
the cooling system should be checked for loose hose
connections, defective hoses, gasket leaks, etc.
Cooling System Checks
1.
Test for restriction in the radiator, by w arm in g
the engine up an d then turning the engine off and
feeling the radiator. The ra d ia to r should be hot along
the left side and w a rm along the right side, with an even
tem perature rise fro m right to left. Cold spots in the
ra d ia to r indicate clogged sections.
2.
W a te r p u m p operatio n m ay be checked by
ru n n in g the engine while squeezing the ra d ia to r upper
hose. A pressure surge should be felt. Check for a
plugged vent-hole in pump.
NOTE: A defective head gasket may allow exhaust
gases to leak into the cooling system. This is
particularly d am a g in g to the cooling system as the
gases com bine with the w ater to form acids which
are harm fu l to the radiator and engine.
WARNING: If you siphon coolant from the
radiator, do not use mouth to start siphoning
action. The coolant solution is POISONOUS
and can cause death or serious illness if
swallowed.
3.
To check for exhaust leaks into the cooling
system, drain coolant from the system until the coolant
level stands ju st above the top o f the cylinder head, then
disconnect the ra d iato r upp er hose and remove the
therm ostat and fan belt. Start the engine and quickly
accelerate several times. At the same time note any
appreciable w ater rise or the ap p earance o f bubbles
which are indicative o f exhaust gases leaking into the
cooling system.
Periodic M aintenance
It is the o w ner’s responsibility to keep the freeze
protection at a level com m ensurate with the area in
which the vehicle will be operated. Regardless o f
w hether freezing tem peratures are or are not expected,
cooling system protection should be m ain ta in e d at least
to -20 °F to provide adequate corrosion protection and
p roper tem perature indicating light operation. With
glycol c o n ten t
less
th a n
re q u ir e m e n t
for -20 °F
protection, coolant boiling point is less than the
tem perature in dicating light setting. W h e n adding
solution due to loss o f coolant for any reason or in areas
where tem peratures lower than -20 °F m ay occur, a
sufficient am o u n t o f an ethylene glycol base coolant that
meets G M Specification 1899-M should be used.
Every two years the cooling system should be
serviced by flushing with plain water, then completely
refilled with a fresh solution o f w ater and a high-quality,
inhibited (perm anent-type) glycol base coolant meeting
G M
Specification
1899-M
and providing freezing
protection at least to -20 °F At this time, also add G M
Cooling System In hibitor and Sealer or equivalent. In
addition, such an inhibitor and sealer should be added every
fall thereafter.
N OTE: Alcohol or methanol base coolants or plain
Summary of Contents for 1977 light duty truck
Page 1: ......
Page 28: ......
Page 70: ...Fig IB 24 Four Season System Vacuum Diagram C K Models 1B 24 LIGHT TRUCK SERVICE M A N U A L...
Page 71: ...Fig lB 25 Overhead System Wiring Diagram C K Models AIR C O N D ITIO N IN G 1 B 2 5...
Page 72: ...Fig IB 26 C60 System Wiring Diagram G Models...
Page 74: ......
Page 75: ...Fig lB 29 Motor Home Chassis Wiring Diagram THERMOSTATIC SWITCH AIR C O N D ITIO N IN G IB 2 9...
Page 106: ......
Page 128: ......
Page 129: ...Fig 2D 5 Typical 05 and 0 6 Vans...
Page 136: ......
Page 148: ...Fig 2D 51 Rear Door Controls...
Page 158: ...Fig 2D 79 Folding Top Assembly...
Page 159: ...Fig 2D 80 Folding Top Side Moldings and Header...
Page 161: ...Fig 2D 85 Dnver s Bucket Seat 14 Fig 2D 86 Passenger s Bucket Seat 14...
Page 162: ...Fig 2D 89 Rear Folding Seat 06 Fig 2D 9 0 Rear Bench Seat 14...
Page 163: ......
Page 164: ......
Page 165: ......
Page 185: ......
Page 186: ......
Page 190: ......
Page 225: ......
Page 226: ......
Page 248: ...Fig 3B 77 Removing Bearing Housing Pivot Pins Fig 3B 79 Replacing Lock Bolt Spring...
Page 278: ...C 10 G 10 20 C 20 30 G 30 P 10 30 9 Fig 3C l Front Suspension C P Series...
Page 284: ...BALL JOINT DIAGNOSTIC PROCEDURE...
Page 316: ......
Page 321: ...Fig 3D 12 Rear Spring Installation G Models...
Page 322: ......
Page 325: ......
Page 326: ......
Page 336: ......
Page 352: ......
Page 378: ......
Page 395: ...Fig 5 2 Front Brake Pipes and Hoses C K Models...
Page 396: ......
Page 397: ...Fig 5 4 Front Brake Pipes and Hoses P Models BRAKES 5 1 3...
Page 400: ......
Page 401: ...V 8 N 4 0 L 6 N 4 0...
Page 402: ......
Page 404: ......
Page 405: ...P300 42 M40 JB9...
Page 438: ......
Page 448: ...Fig 6A 4 P Series Engine Rear Mount...
Page 451: ...Fig 6A 8 K Series Engine Rear Mount...
Page 452: ...ENGINE M O U N T BRACKET ALL K SERIES W ITH L 6 ENGINE 6A14 LIGHT TRUCK SERVICE M A N U A L...
Page 483: ...FUEL PUMP PUSH ROD OILING OIL F LTER AND BY PASS VALVE...
Page 484: ...FUEL PUMP PUSH ROD OILING CRANKCASE AND CRANKSHAFT OILING VALVE MECHANISM OILING...
Page 487: ......
Page 488: ...MOUNT VIEW A V AUTOMATIC TRANSMISSION FRONT MANUAL TRANSMISSION...
Page 489: ......
Page 490: ......
Page 568: ......
Page 602: ......
Page 605: ......
Page 612: ...Fig 6D 3i High Energy Ignition Basic W iring...
Page 644: ......
Page 648: ...DISTRIBUTOR VALVE Fig 6E 3 Vacuum Hose Schematic L6 292 CID Calif HD Emissions...
Page 649: ...V A LV E Fig 6E 5 Vacuum Hose Schematic V8 305 CID HD Emissions...
Page 650: ...Fig 6E 7 Vacuum Hose Schematic V8 350 CID High Altitude Calif LD Emissions...
Page 651: ...VALVE Fig 6E 9 Vacuum Hose Schematic V8 350 400 CID Except Calif HD Emissions...
Page 652: ...CANISTER...
Page 653: ...PCV V AL VE Fig 6E 13 Vacuum Hose Schematic V8 454 CID Except Calif HD Emissions...
Page 672: ...Fig 6E 29 Air Cleaner 305 350 400 V8 CK...
Page 682: ......
Page 692: ......
Page 700: ...Fig 7A 6B Detent Downshift Cable C K and P Series...
Page 709: ...Fig 7 A 12B CBC 350 Hydraulic Circuit A U TO M A T IC T R A N S M IS S IO N 7 A 1 7...
Page 743: ...VIEW B FLAT IvEwfDl l6 G tO 2 GAGE...
Page 744: ......
Page 755: ...V I E W B WITH AUTOMATIC TRANSMISSION WITH MANUAL TRANSMISSION V I E W A...
Page 760: ...r...
Page 766: ......
Page 767: ...V I E W D 1 6 ENGINE VIEW V 8 ENGINE...
Page 768: ......
Page 775: ......
Page 788: ......
Page 794: ...G A S G A U G E...
Page 805: ......
Page 836: ...Fig 8 58 Seat Belt Reminder System Schematic...
Page 844: ...C H E C K n...
Page 852: ......
Page 853: ...SPECIAL TOOLS J 2 3 5 2 0...