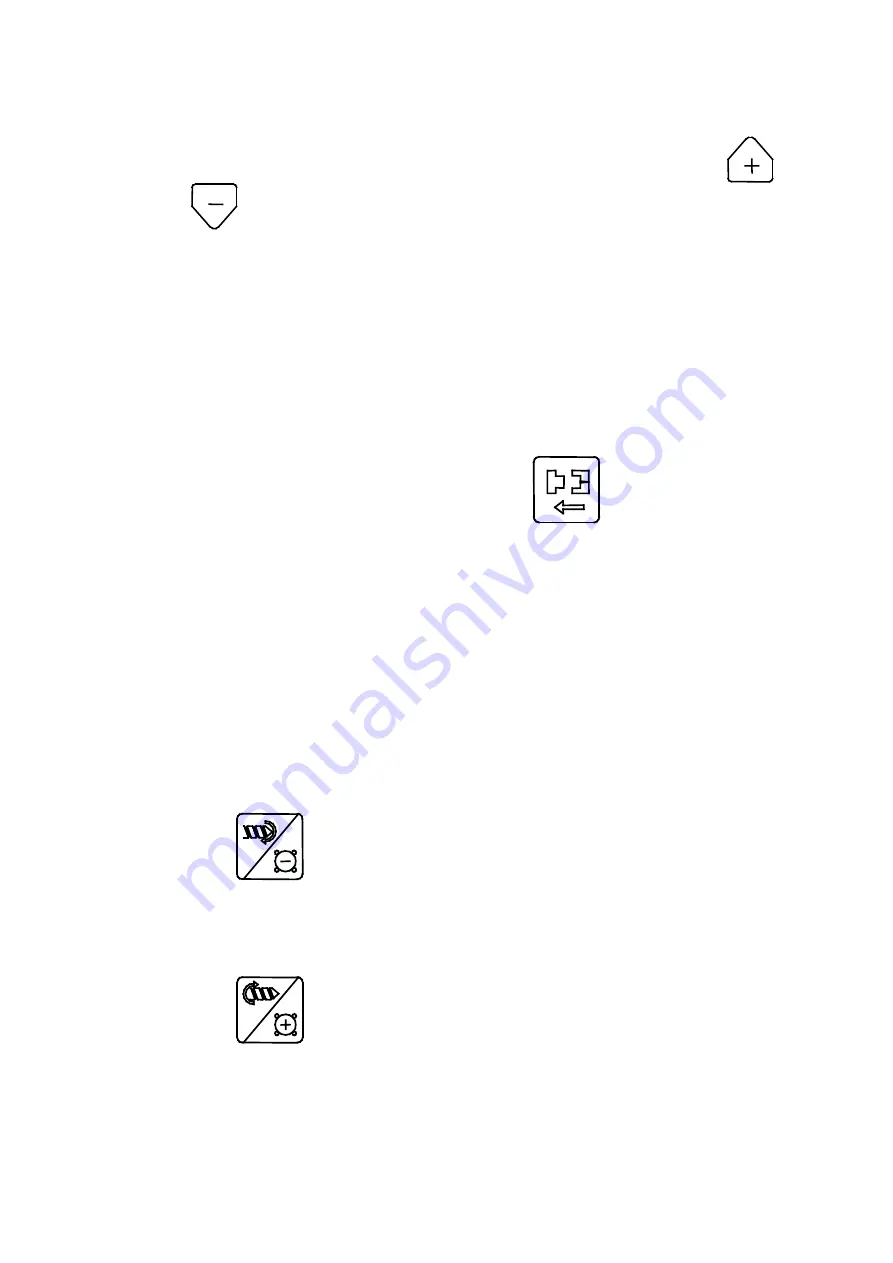
1 Operational Manual
H) KKKKK :Computers automatically calculate low-pressure closing end-position for
reference after the setup of clamping force 。
I) M :Function selection for clamping force auto adjustment. Press
to open
and
to close。
2.11.1.2 Operational Method for Mould Thickness Adjustment:
A) Note:
A.a) If safety doors one not closed, the warning message
“
019 safety doors is
not closed
”
will show on the monitor. At times that auxiliary signal detects
closed doors
“
061 safety door device abnormal
“
will appear. Check safety door
limits switch. If machine
’
s mold still open, the following message will
appear:
“
052 mold-open stroke not completed
”
,press
until
“
051 mold
–
open s
troke completed
“
takes over.
A.b) Go to Menu (55) to correct
“
mold thickness BBBB.Bmm
”
while the mold
thickness is not exact.
A.c) Turn off mold adjustment for
“
017 mold adjustment motor overload
”
to
check motor load and mechanism.
A.d) Turn off mold adjustment for
“
023 mold adjustment counter error
”
to
check counter switch (
Input 31
) and mechanism.
A.e) In mold adjustment, if general mold thickness adjustment distance is
wrong, then correct counter signal and counter teeth.
Caution: Do not change counter signal inspection time, otherwise mold
B) Manual operation for mold thickness adjustment:
B.a) Press
and the molds will adjust forward, leaving a reduced mold
height and strengthened clamping force. Let go of the key and the function
will stop. If mold adjustment forward goes beyond computer-set minimum
height,
“
021 mold adjustment beyond minimum distance
“ shows and mold
adjustment forward will stop.
B.b) Press
and the molds will adjust backward, leaving an increased
mold height and lessened clamping force. Let go of the key and function
will stop. When movement goes beyond limit switches,
“
022 mold adjustment e
xceed maximum size
“
will show and mold adjustment backward will stop.
C) Auto operation for mold thickness adjustment:
C.a) Measure the mold thickness, say 430.0mm, key in the measured figure to
04/08/13
51