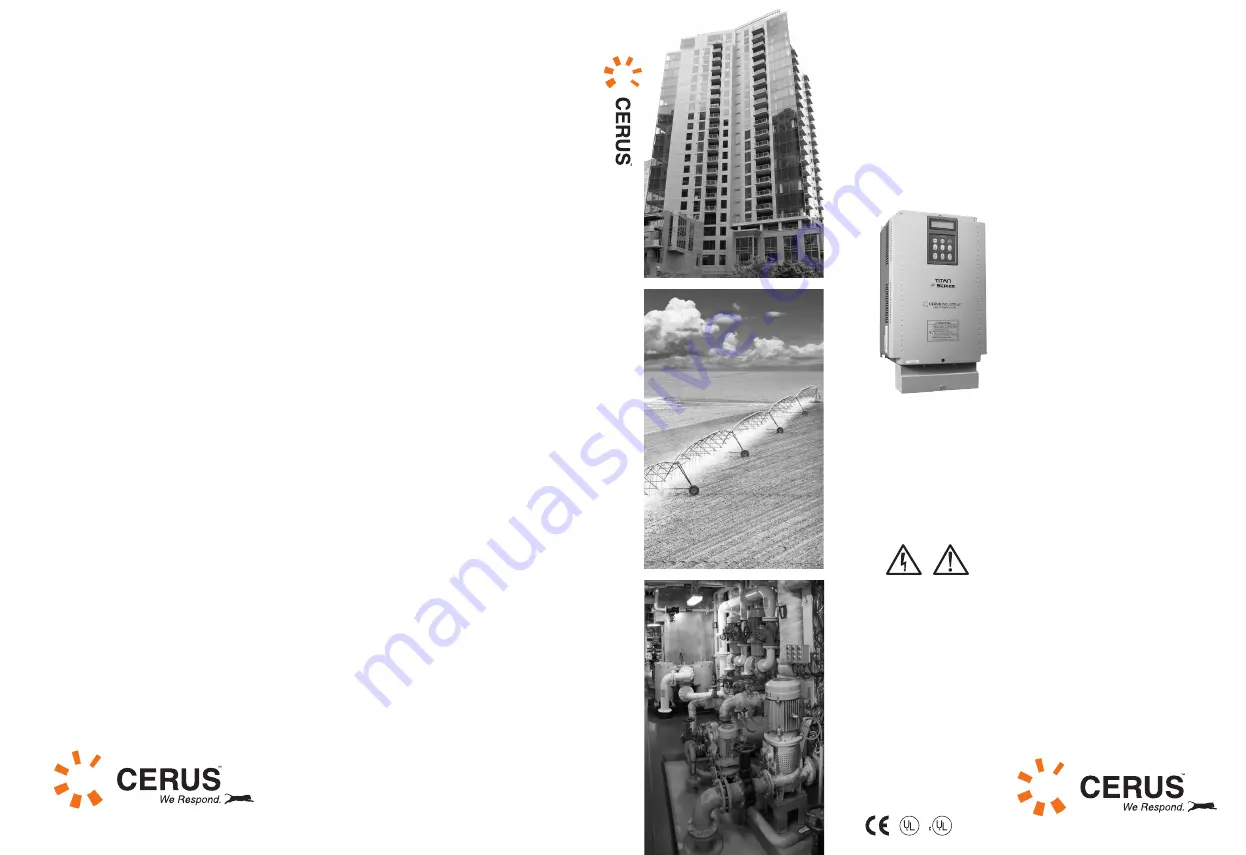
P Series
Fan & Pump Optimized
Variable Frequency Drive
0.5–40HP (200~230VAC) , 3Ø
0.5–700HP (380~480VAC), 3Ø
0.5-150HP (525~600VAC), 3Ø
Dual Rated for Constant & Variable Torque
Integrated PID Control
Application Based Commisioning
cerusind.com | 1.800.962.3787
Installation, Programming
Operation, & Maintenance
Manual
As with all electrical products, read manual thoroughly
before operating. Only qualified, expert personnel should
perform maintenance and installation. Contact the nearest
authorized service facility for examination, repair, or
adjustment. Do not disassemble or repair unit; death or
injury due to electrical shock or fire hazard may result.
Product improvement is a continual process at Cerus
Industrial. Specifications and manual data subject to
change.
Consult
factory
for
additional
information.
CAUTION, SAFETY WARNING
I n t e l l i g e n t M o t o r C o n t r o l s
P
Series
Man
ual
F
an
&
Pump
Optimiz
ed
V
ar
iab
le
F
requency
Dr
iv
e
cerusind.com | 1.800.962.3787
Summary of Contents for CI-007-P2
Page 23: ......
Page 107: ......
Page 110: ...Chapter 6 Parameter Description 7 4 PID control with Pipe Broken function diagram...
Page 111: ...Chapter 6 Parameter Description 7 4 7 5 PID control with Pre PID function diagram...
Page 112: ...Chapter 6 Parameter Description 7 5 7 6 PID Control Setting Notes...
Page 113: ......