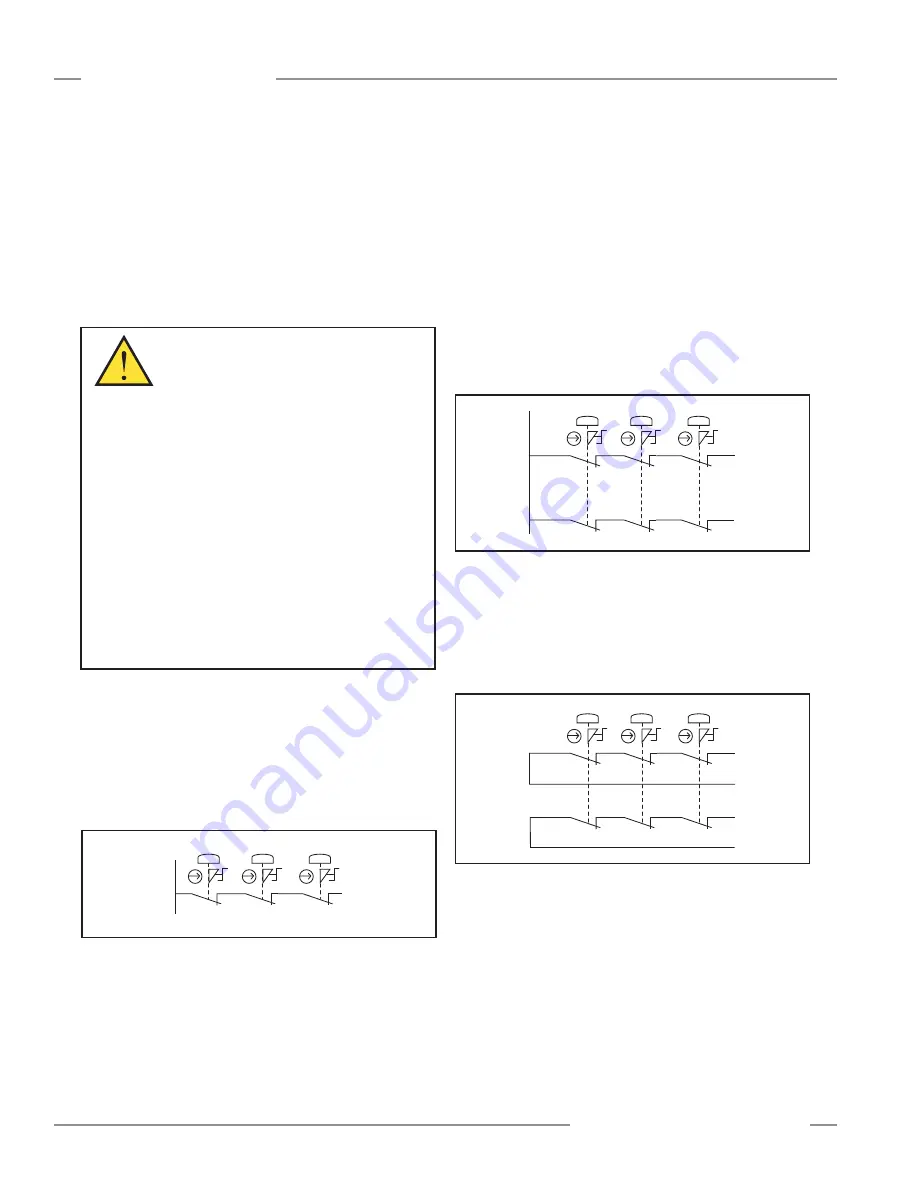
88
P/N 133487
Banner Engineering Corp.
•
Minneapolis, U .S .A .
www .bannerengineering .com • Tel: 763 .544 .3164
SC22-3 Safety Controller
Instruction Manual
Appendix A
In addition to the requirements stated above, the design and
the installation of the emergency stop device (e .g ., switch,
button, or rope-pull) must be such that the possibility of a
catastrophic failure of the device resulting in the loss of the
safety function must be excluded (designed out) . The device
must comply with ISO 13850 requirements such that the fault
exclusions of ISO 13849-2 are applicable . Electromechanical
devices that have contacts designed in accordance to IEC
60947-5-1 Annex K and that are installed per manufacturer’s
instructions are expected to open when the emergency stop
device is actuated .
WARNING . . .
Multiple E-Stop
Switches
Whenever two or more emergency stop switches
are connected to the same Controller:
• Contacts of the corresponding pole of each switch must be
connected together in series. Never connect the contacts
of multiple Emergency Stop switches in parallel to one
Controller. Such a parallel connection defeats the switch contact
monitoring ability of the Controller and creates an unsafe condition
which could result in serious injury or death .
•
Each switch must be individually actuated (engaged),
then re-armed and the Controller reset. This allows the
Controller to check each switch and its wiring to detect faults .
Failure to test each switch individually in this manner could
result in undetected faults and create an unsafe condition
which could result in serious injury or death. This check must
be performed during periodic checkouts .
Category 2: A single-channel emergency stop application
typically provides a Category 2 level of circuit performance,
because a short circuit could cause the loss of the safety
function . The principle of fault exclusion must be incorporated
into the design and installation to either eliminate, or reduce
to an acceptable (minimal) level of risk, the possibility of
undetected faults or failures that can result in the loss of the
safety function .
Figure A-6. Category 2 E-stop circuit
Category 3: A dual-channel hookup swi24V dc is
typically a Category 3 application, because a single failure does
not result in a loss of safety . Loss of the switching action in
one channel is detected by the actuation of the E-stop button,
the opening of the second channel, and the monitoring function
of the safety inputs . However, a short circuit between input
channels or safety outputs may not be detected . It should be
noted that an accumulation of faults may cause the loss of the
safety function .
The principle of fault exclusion must be incorporated into the
design and installation to either eliminate, or reduce to an
acceptable (minimal) level of risk, the possibility of undetected
faults or catastrophic failures that could result in the loss of the
safety function .
Figure A-7. Category 3 E-stop circuit
Category 4: The self-monitoring safety inputs can be interfaced
to achieve a Category 4 application . The principle of fault
exclusion must be incorporated into the design and installation
to either eliminate, or reduce to an acceptable (minimal) level
of risk, the possibility of catastrophic failures or faults that could
result in the loss of the safety function .
Figure A-8. Category 4 E-stop circuit