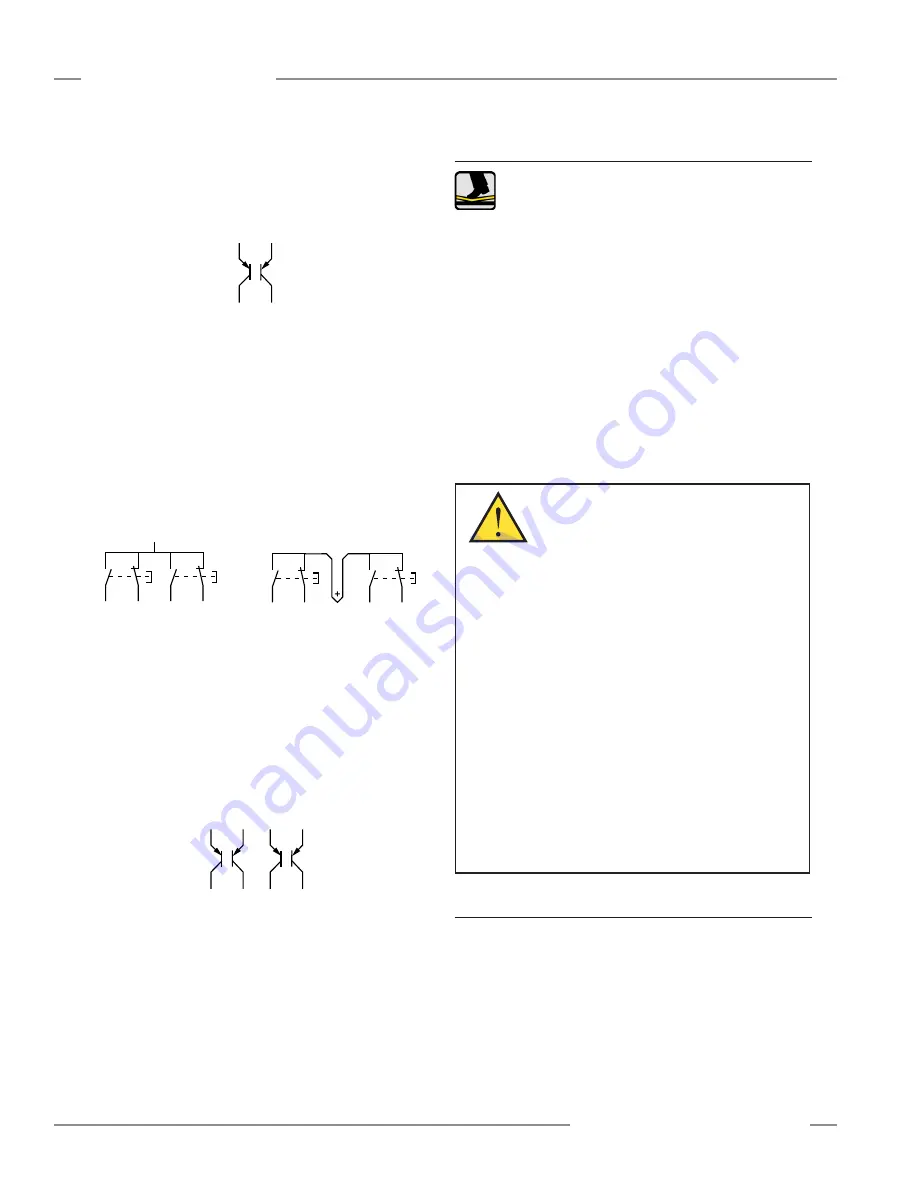
84
P/N 133487
Banner Engineering Corp.
•
Minneapolis, U .S .A .
www .bannerengineering .com • Tel: 763 .544 .3164
SC22-3 Safety Controller
Instruction Manual
Appendix A
A.6 Safety Mats
The Safety Controller may be used to monitor pressure-
sensitive safety mats and safety edges (sensors) .
The purpose of the safety mat input of the SC22-3 is to verify
the proper operation of 4-wire presence-sensing safety mats
(sensors) . Multiple mats may be switched in series to one
Controller (see Section A .6 .2) . NOTE: The Controller is not
designed to monitor 2-wire mats, bumpers, or edges (with or
without sensing resistors).
The function is to monitor the contacts (contact plates) and the
wiring of one or more safety mat(s) for failures and prevent the
machine from restarting if a failure is detected . A reset routine
after the operator steps off the safety mat can be provided by
the Safety Controller, or, if the Controller is used in auto-reset
mode, the reset/restart function must be provided by the machine
control system . This prevents the controlled machinery from
restarting automatically after the mat is cleared .
A.6.1 Safety Mat Requirements
The following are minimum requirements for the design,
construction, and installation of four-wire safety mat sensor(s)
to be interfaced with the Safety Controller . These requirements
are a summary of standards ISO 13856-1, ANSI/RIA R15 .06 and
ANSI B11 .19 . The user must review all relevant applicable
regulations and standards and apply the Controller and any
sensors in full compliance.
WARNING . . .
Application of Safety Mats
• Requirements vary widely for the level of control reliability or
ISO 13849-1 (EN954-1) Category in the application of safety
mats . It is the responsibility of the user to safely install,
operate, and maintain each safety mat (or safety edge) system
per the manufacturer’s recommendations and comply with all
relevant laws and regulations .
• Do not use a safety mat as a tripping device to initiate
machine motion (such as in a presence-sensing device initiation
application), due to the possibility of unexpected start or re-start of
the machine cycle resulting from failure(s) within the mat and the
interconnect cabling .
• Do not use a safety mat to enable or provide the means
to allow the machine control to start hazardous motion by
simply standing on the safety mat (e .g ., at a control station) .
This type of application uses reverse/negative logic and certain
failures (e .g ., loss of power to the Controller) can result in a “false”
enable signal .
Dual-Channel (PNP device): The figure below is a Type
IIIa Two-Hand Control circuit as described by ISO 13851,
and typically can meet ISO 13849-1 (EN 954-1) category
1 requirements . The SC22-3 does not provide short circuit
detection between channels in this configuration .
Two-Hand Operation
2-Ch, 2 Terminals
2-Ch, 3 Terminals
2-Ch, 4 Terminals
2-Ch, 2 Terminals
2 PNP
Two Hand Operation - 2x Dual Channel Complementary
2x Complementary,
4 Terminals
2x Complementary,
5 Terminals
2x Complementary,
4 Terminals, 4 PNP
Revision History
Rev C - Corrected “OFF” and “ON” on Two-hand Operation - 2x Dual Channel Complementary, 2x Complementary, 4 Terminals, 4 PNP
20-Sept-06 Rev. D - Moved 24V, ON and OFF text closer to drawings.
13-Oct-06 Rev. E Gray lines moved below the black lines
21-Nov-06 Rev. F - Added + sign to 2-Ch, 3 Terminals, 2-Ch, 4 Terminals, 2x Dual Channel Complementary, 5 Terminals
10-Jan-07 Rev. G - C sign text to outlines, changed gray lines to 6 pt. dashed lines
25-May-07 Rev H - Changed 2-Ch, 2 Terminals 2 PNP; 2x Complementary, 5 Terminals (centered arrow) and 2x Complementary, 4 Terminals, 4 PNP
24V
24V
OFF
OFF
ON
OFF
ON
OFF
2X Complementary (4 terminals or 5 terminals): The figure
below is a Type IIIc Two-Hand Control circuit as described by
ISO 13851, and typically can meet ISO 13849-1 (EN 954-1)
Category 4 requirements . In the actuated condition (e .g ., S1
open/S2 closed below) a short across the closed contact can
cause the response time to increase based on the debounce
time . In this situation, the response time could be longer as
specified, based on the (selected) debounce time, see Section
3 .2 .2
NOTE: Select this option if using Banner Self-checking Touch
Button models STBVR81…
Two-Hand Operation
2-Ch, 2 Terminals
2-Ch, 3 Terminals
2-Ch, 4 Terminals
2-Ch, 2 Terminals
2 PNP
Two Hand Operation - 2x Dual Channel Complementary
2x Complementary,
4 Terminals
2x Complementary,
5 Terminals
2x Complementary,
4 Terminals, 4 PNP
Revision History
Rev C - Corrected “OFF” and “ON” on Two-hand Operation - 2x Dual Channel Complementary, 2x Complementary, 4 Terminals, 4 PNP
20-Sept-06 Rev. D - Moved 24V, ON and OFF text closer to drawings.
13-Oct-06 Rev. E Gray lines moved below the black lines
21-Nov-06 Rev. F - Added + sign to 2-Ch, 3 Terminals, 2-Ch, 4 Terminals, 2x Dual Channel Complementary, 5 Terminals
10-Jan-07 Rev. G - C sign text to outlines, changed gray lines to 6 pt. dashed lines
25-May-07 Rev H - Changed 2-Ch, 2 Terminals 2 PNP; 2x Complementary, 5 Terminals (centered arrow) and 2x Complementary, 4 Terminals, 4 PNP
24V
24V
OFF
OFF
ON
OFF
ON
OFF
S1 S2
S3 S4
Two-Hand Operation
2-Ch, 2 Terminals
2-Ch, 3 Terminals
2-Ch, 4 Terminals
2-Ch, 2 Terminals
2 PNP
Two Hand Operation - 2x Dual Channel Complementary
2x Complementary,
4 Terminals
2x Complementary,
5 Terminals
2x Complementary,
4 Terminals, 4 PNP
Revision History
Rev C - Corrected “OFF” and “ON” on Two-hand Operation - 2x Dual Channel Complementary, 2x Complementary, 4 Terminals, 4 PNP
20-Sept-06 Rev. D - Moved 24V, ON and OFF text closer to drawings.
13-Oct-06 Rev. E Gray lines moved below the black lines
21-Nov-06 Rev. F - Added + sign to 2-Ch, 3 Terminals, 2-Ch, 4 Terminals, 2x Dual Channel Complementary, 5 Terminals
10-Jan-07 Rev. G - C sign text to outlines, changed gray lines to 6 pt. dashed lines
25-May-07 Rev H - Changed 2-Ch, 2 Terminals 2 PNP; 2x Complementary, 5 Terminals (centered arrow) and 2x Complementary, 4 Terminals, 4 PNP
24V
24V
OFF
OFF
ON
OFF
ON
OFF
2X Complementary (PNP device): The figure below is a
Type IIIc Two-Hand Control circuit as described by ISO 13851,
and typically can meet ISO 13849-1 (EN 954-1) Category 4
requirements . In the actuated condition (e .g ., S1 open/S2
closed below), a short across the closed contact can cause
the response time to increase, based on the debounce time . In
this situation, the response time could be longer than specified,
based on the (selected) debounce time, see Section 3 .2 .2 .
NOTE: Select this option if using Banner Self-checking Touch
Buttons models STBVP6…
S1 S2
Two-Hand Operation
2-Ch, 2 Terminals
2-Ch, 3 Terminals
2-Ch, 4 Terminals
2-Ch, 2 Terminals
2 PNP
Two Hand Operation - 2x Dual Channel Complementary
2x Complementary,
4 Terminals
2x Complementary,
5 Terminals
2x Complementary,
4 Terminals, 4 PNP
Revision History
Rev C - Corrected “OFF” and “ON” on Two-hand Operation - 2x Dual Channel Complementary, 2x Complementary, 4 Terminals, 4 PNP
20-Sept-06 Rev. D - Moved 24V, ON and OFF text closer to drawings.
13-Oct-06 Rev. E Gray lines moved below the black lines
21-Nov-06 Rev. F - Added + sign to 2-Ch, 3 Terminals, 2-Ch, 4 Terminals, 2x Dual Channel Complementary, 5 Terminals
10-Jan-07 Rev. G - C sign text to outlines, changed gray lines to 6 pt. dashed lines
25-May-07 Rev H - Changed 2-Ch, 2 Terminals 2 PNP; 2x Complementary, 5 Terminals (centered arrow) and 2x Complementary, 4 Terminals, 4 PNP
24V
24V
OFF
OFF
ON
OFF
ON
OFF
S3 S4