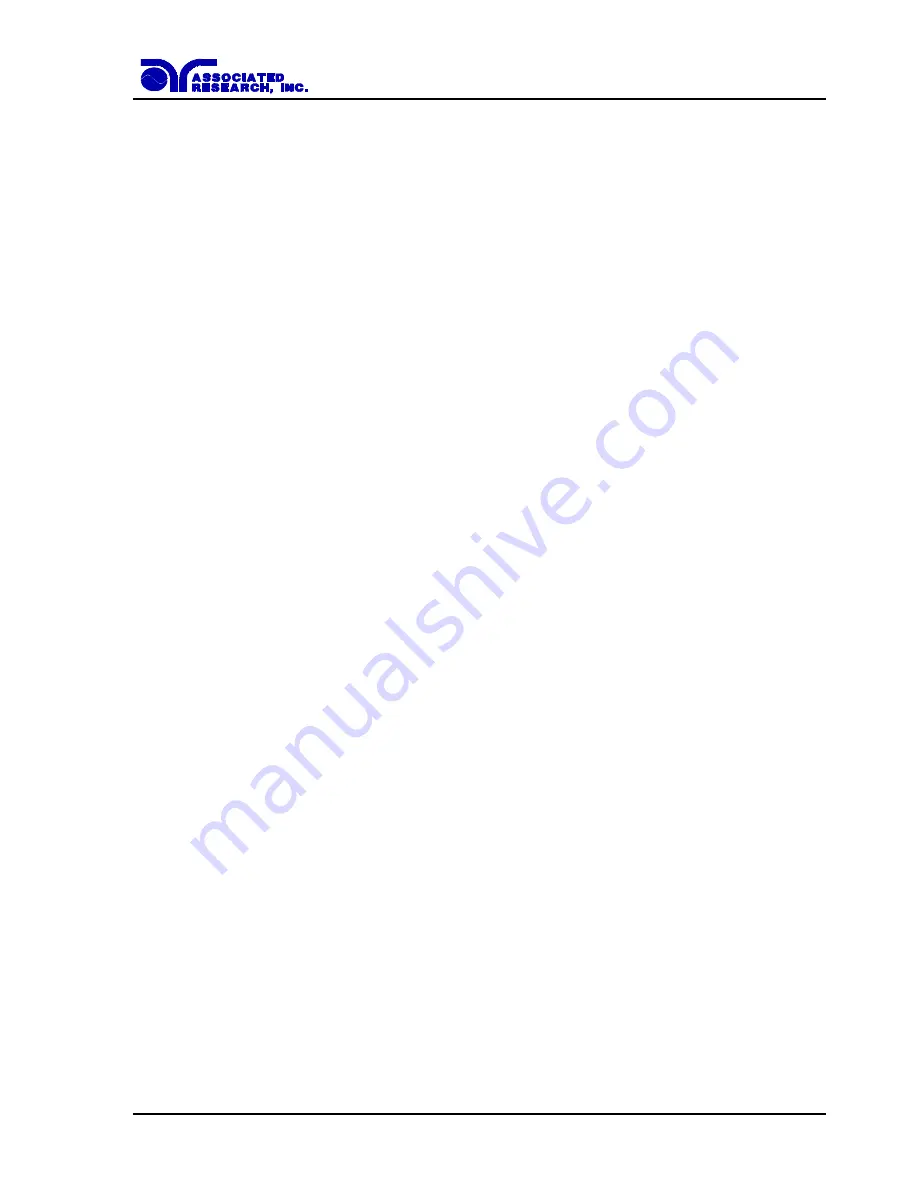
8
1.5. Introduction to Product Safety Testing
1.5.1. The Importance of Safety Testing
Product Safety Tests are specified during the design and development stages of a product as
well as in the production of the products to insure that it meets basic safety requirements.
These tests are designed to verify the safety of the electrical products in that they do not
jeopardize the safety of the people, domestic animals, and property of anyone who may come in
contact with these products. In an era of soaring liability costs, original manufacturers of
electrical and electronic products must make sure every item is as safe as possible. All products
must be designed and built to prevent electric shock, even when users abuse the equipment or
by-pass built in safety features.
To meet recognized safety standards, one common test is the "dielectric voltage-withstand test".
Safety agencies which require compliance safety testing at both the initial product design stage
and for routine production line testing include: Underwriters Laboratories, Inc. (UL), the
Canadian Standards Association (CSA), the International Electrotechnical Commission (IEC),
the British Standards Institution (BSI), the Association of German Electrical Engineers (VDE)
and (TÜV), the Japanese Standards Association (JSI). These same agencies may also require
that an insulation resistance test and high current ground bond test be performed.
1.6. The Different Types of Safety Tests
1.6.1. Dielectric Withstand Test
The principle behind a dielectric voltage - withstand test is simple. If a product will function
when exposed to extremely adverse conditions, it can be assumed that the product will function
in normal operating circumstances.
Common Applications of the Dielectric Withstand Test:
•
Design (performance) testing: Determining design adequacy to meet service conditions.
•
Production Line testing: Detecting defects in material or workmanship during processing.
•
Acceptance testing: Proving minimum insulation requirements of purchased parts.
•
Repair Service testing: Determine reliability and safety of equipment repairs.
The specific technique used to apply the dielectric voltage - withstand test to each product is
different. During a dielectric voltage - withstand test, an electrical device is exposed to a
voltage significantly higher than it normally encounters, for a specified duration of time.
During the test, all current flow from the high voltage output to the return is measured. If,
during the time the component is tested, the current flow remains within specified limits, the
device is assumed safe under normal conditions. The basic product design and use of the
insulating material will protect the user against electrical shock.
Summary of Contents for HYPOTULTRA III 7620
Page 7: ......
Page 8: ......
Page 130: ...122 configure it through the drive s properties in Windows ...