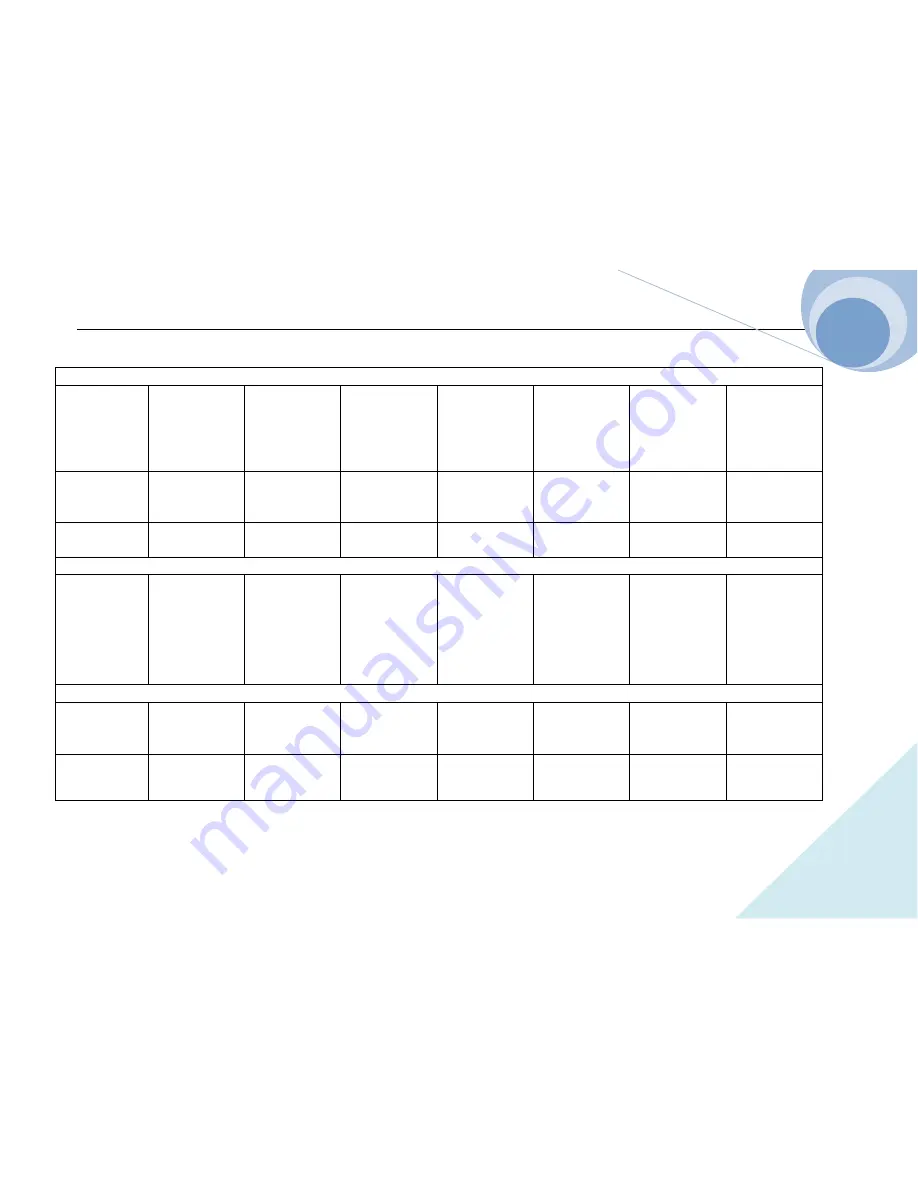
Chapter V Remote Programming Operation
108
ARRAY
Environmental Conditions
Temperature
*1
Relative
Humidity
0
~
50ºC
≤
85%
0
~
50ºC
≤
85%
0
~
50ºC
≤
85%
0
~
50ºC
≤
85%
0
~
50ºC
≤
85%
0
~
50ºC
≤
85%
0
~
50ºC
≤
85%
Remote
Interface
*5
RS232, GPIB, USB
RS232, GPIB, USB
RS232, GPIB, USB
RS232, GPIB, USB
RS232, GPIB, USB
RS232, GPIB, USB
RS232, GPIB, USB
Programmable
Language
SCPI
SCPI
SCPI
SCPI
SCPI
SCPI
SCPI
AC Input
Voltage
Frequency
Input Power
(AC110V
、
AC120V
、
AC220V
、
AC240V)±10%
48 to 63Hz
80VA
(AC110V
、
AC120V
、
AC220V
、
AC240V)±10%
48 to 63Hz
80VA
(AC110V
、
AC120V
、
AC220V
、
AC240V)±10%
48 to 63Hz
80VA
(AC110V
、
AC120V
、
AC220V
、
AC240V)±10%
48 to 63Hz
80VA
(AC110V
、
AC120V
、
AC220V
、
AC240V)±10%
48 to 63Hz
130VA
(AC110V
、
AC120V
、
AC220V
、
AC240V)±10%
48 to 63Hz
130VA
(AC110V
、
AC120V
、
AC220V
、
AC240V)±10%
48 to 63Hz
130VA
Outline Dimension
Net Weight
24kg
26.5kg
24kg
38kg
38kg
42kg
45kg
Frame
Fig1
Fig 1
Fig 1
Fig 1
Fig 2
Fig 2
Fig 2
Summary of Contents for 3750A
Page 1: ...Contents USER S MANUAL 375X SERIES ELECTRONIC LOAD ...
Page 63: ...Chapter III Installation 59 ARRAY ...
Page 114: ...Chapter V Remote Programming Operation 110 ARRAY Frame Diagram Fig 1 ...
Page 115: ...Chapter V Remote Programming Operation 111 ARRAY ...
Page 116: ...Chapter V Remote Programming Operation 112 ARRAY Fig 2 ...
Page 120: ......