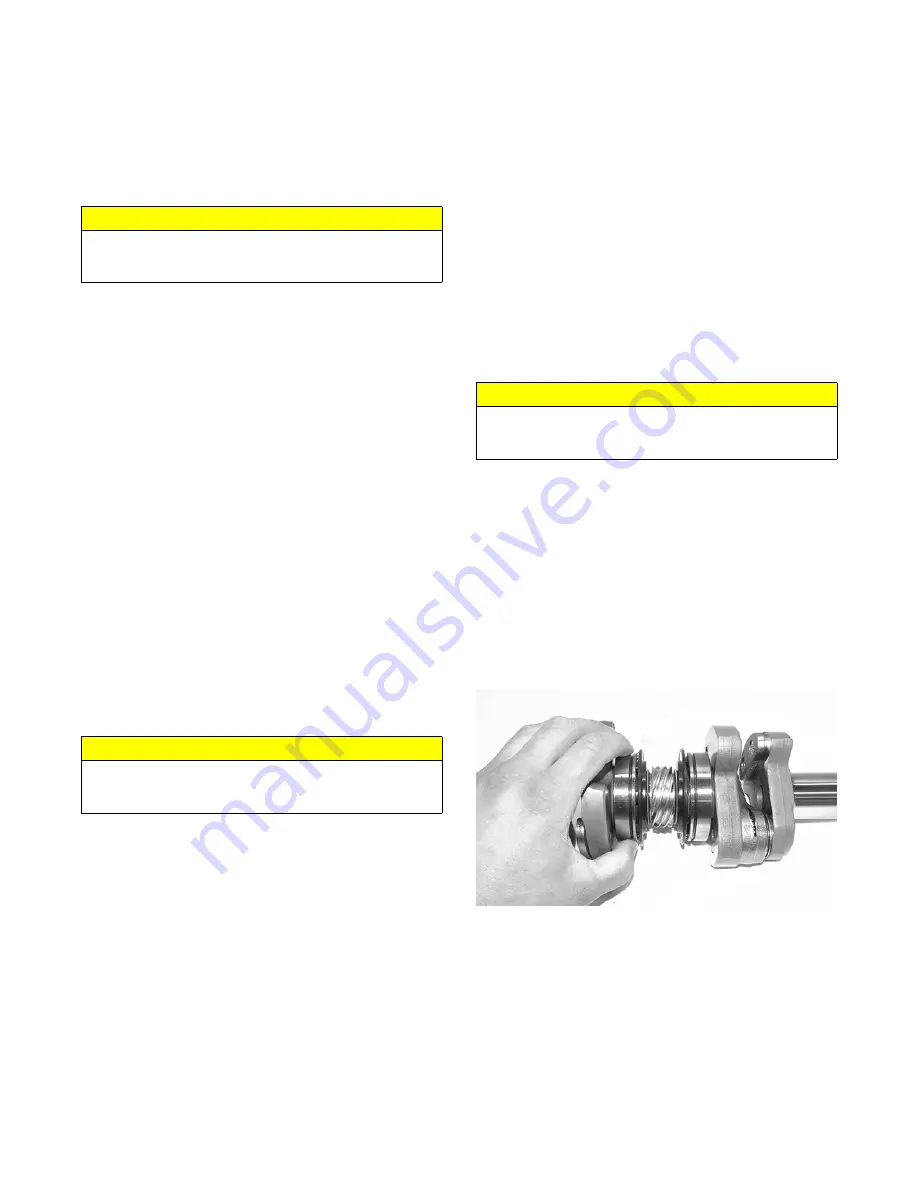
78
3. Place the cylinder head on a Surface Plate covered
with #400 grit wet-or-dry sandpaper. Using light
pressure, move each cylinder head in a figure eight
motion. Inspect the sealing surface for any indication
of high spots. A high spot can be noted by a bright
metallic finish. Correct any high spots before assem-
bly by continuing to move the cylinder head in a fig-
ure eight motion until a uniform bright metallic
finish is attained.
CYLINDERS
1. Using a non-metallic carbon removal tool, remove
carbon buildup from the exhaust ports.
2. Wash the cylinders in parts-cleaning solvent.
3. Inspect the cylinders for pitting, scoring, scuffing,
and corrosion. If marks are found, repair the surface
with the Ball Hone and honing oil.
NOTE: To produce the proper 45° crosshatch pat-
tern, maintain a low drill RPM. If honing oil is not
available, use a lightweight, petroleum-based oil.
Thoroughly clean the cylinders after honing using
detergent soap and hot water and dry with com-
pressed air; then immediately apply oil to the cylinder
bores. If a bore is severely damaged or gouged, the
cylinder must be replaced or replated.
4. Place the head surface of each cylinder on the sur-
face plate covered with #400 grit wet-or-dry sandpa-
per. Using light pressure, move each cylinder in a
figure eight motion. Inspect the surface for any indi-
cation of high spots. A high spot can be noted by a
bright metallic finish. Correct any high spots before
assembly by continuing to move the cylinder in a fig-
ure eight motion until a uniform bright metallic fin-
ish is attained.
PISTON
1. Using a non-metallic carbon removal tool, remove
the carbon buildup from the dome of each piston.
CRANKCASE
1. Scrape of any residual silicone from both the top and
bottom crankcase halves making sure not to damage
the sealing surface; then wash the crankcase halves
in parts-cleaning solvent.
NOTE: Before washing the crankcase halves, make
sure the four bearing dowel pins have been removed
and accounted for.
2. Inspect the crankcase halves for scoring, pitting,
scuffing, or any imperfections in the casting.
3. Inspect all threaded areas for damaged or stripped
threads.
4. Inspect the bearing areas for cracks or excessive
bearing movement. If evidence of excessive bearing
movement is noted, the crankcase must be replaced.
5. Inspect the bearing dowel pins for wear.
6. Inspect the sealing surfaces of the crankcase halves
for trueness by placing each crankcase half on the
surface plate covered with #400 grit wet-or-dry sand-
paper. Using light pressure, move each half in a fig-
ure eight motion. Inspect the sealing surfaces for any
indication of high spots. A high spot can be noted by
a bright metallic finish. Correct any high spots by
continuing to move the half in a figure eight motion
until a uniform bright metallic finish is attained.
NOTE: Care must be taken not to remove an exces-
sive amount of aluminum, or the crankcase must be
replaced. If excessive aluminum is removed, too much
pre-load will be exerted on the crankshaft bearings
when assembled.
CRANKSHAFT
NOTE: If any servicing of the connecting rods, cen-
ter bearings, or water pump drive gear is necessary,
Arctic Cat recommends the crankshaft be taken to a
qualified crankshaft rebuild shop for that service.
1. Wash the crankshaft with bearings in parts-cleaning
solvent.
2. Inspect the bearings for wear, scoring, scuffing, dam-
age, or discoloration. Rotate the bearings. Bearings
must rotate freely and must not bind or feel rough. If
any abnormal condition is noted, replace the bearing.
CWI-060
3. Inspect the connecting-rod bearings by rotating
them. The bearings must rotate freely and must not
bind or feel rough. If a connecting-rod bearing must
be replaced, the connecting rod and crank pin must
also be replaced.
CAUTION
Water or parts-cleaning solvent must be used in con-
junction with the wet-or-dry sandpaper or damage to
the sealing surface may result.
CAUTION
Water or parts-cleaning solvent must be used in con-
junction with the wet-or-dry sandpaper or damage to
the sealing surface may result.
CAUTION
Water or parts-cleaning solvent must be used in con-
junction with the wet-or-dry sandpaper or damage to
the sealing surface may result.
Summary of Contents for M 8000
Page 1: ...www arcticcat com SERVICE MANUAL www arcticcat com...
Page 42: ...41 500cc_2A_15...
Page 50: ...49 600_14_2...
Page 58: ...57 800_12_2...
Page 155: ...154 Troubleshooting Servomotor SERVO1A16...
Page 156: ...155 SERVO2rv16...
Page 193: ...192 0747 414 M 141 High Country Models...
Page 209: ...208 NOTES...
Page 210: ...Printed in U S A Trademarks of Arctic Cat Inc Thief River Falls MN 56701 p n 2260 847...