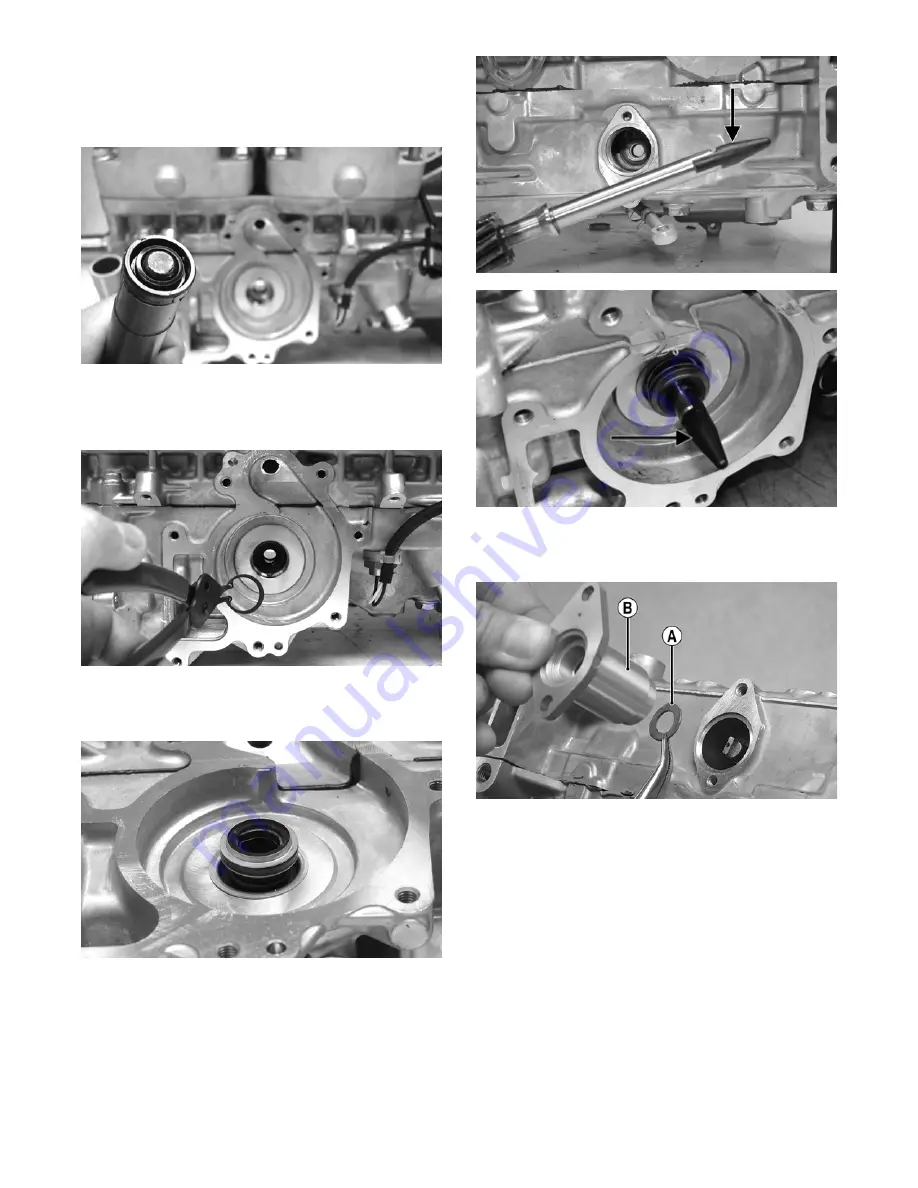
114
ASSEMBLING
1. Thoroughly clean the seal surfaces of the crankcase.
2. Position the oil seal onto the seal driver (spring side
towards the crankshaft). Gently tap into position.
FS230
3. Apply a small amount of grease to the oil seal lips.
4. Using a pair of snap ring pliers, install the snap ring
securing the oil seal in the crankcase.
FS228
5. Using the seal driver, carefully install the outer water
pump mechanical seal. Gently tap the seal down into
position until it seats itself against the crankcase.
FS232
6. Apply a light coat of grease to the sealing surface of
the oil-injection pump driveshaft; then install Oil
Seal Protector Tool at the end of the shaft. Twist the
shaft while pushing it through the oil and water
pump seals until the shaft gear engages with the
drive gear of the crankshaft; then remove the tool.
FS233A
IO025B
7. Position the shim (A) on the oil pump end of the
shaft; then with the O-ring in place on the retainer
(B), install the oil-injection pump retainer.
IO026A
8. With the O-ring in place on the oil-injection pump,
align the pump with the shaft; then install the pump.
Secure with the cap screws (coated with blue Loctite
#243) (B) and tighten to 96 in.-lb. Place the lower
check valve into position; then secure with the gas-
kets and cap screw (A). Tighten to 48 in.-lb.
Summary of Contents for M 8000
Page 1: ...www arcticcat com SERVICE MANUAL www arcticcat com...
Page 42: ...41 500cc_2A_15...
Page 50: ...49 600_14_2...
Page 58: ...57 800_12_2...
Page 155: ...154 Troubleshooting Servomotor SERVO1A16...
Page 156: ...155 SERVO2rv16...
Page 193: ...192 0747 414 M 141 High Country Models...
Page 209: ...208 NOTES...
Page 210: ...Printed in U S A Trademarks of Arctic Cat Inc Thief River Falls MN 56701 p n 2260 847...