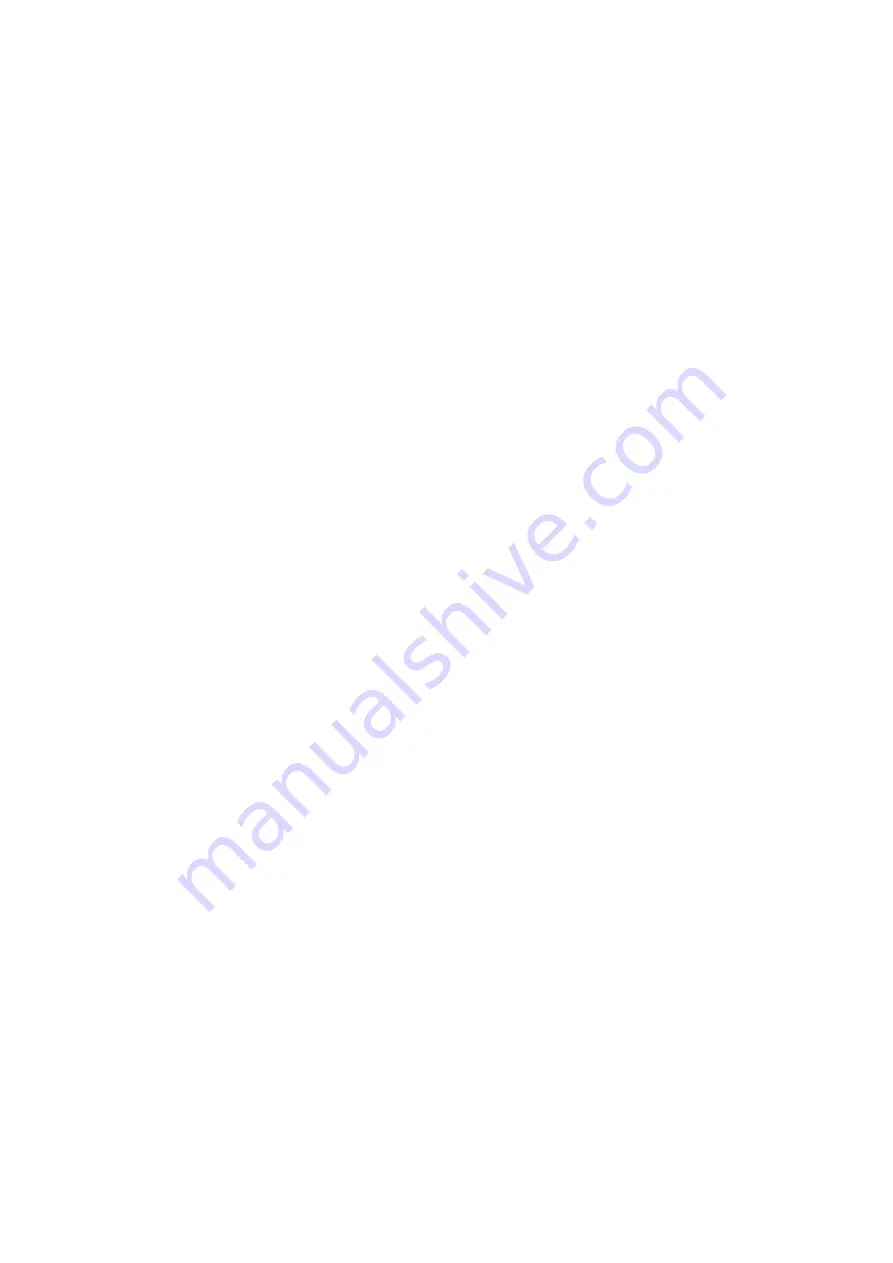
Page 4-9
c)
Supply coolant from the top of coolant tank.
7. Greasing the Chuck Master Jaws
a)
Stop the spindle
b)
Supply grease from the three grease cups around the chuck.
c)
Coolant splashed on the chuck will wash away the grease. Therefore,
supply grease as often as possible.
8. Check before Daily Operation
Before turning on the power
a)
Make sure that there are no abnormalities for external piping, cables and
coating intact, all doors closed ……..etc.
b)
Check the shop floor around the machine for the hazards from such as
coolant, hydraulic oil, lubricating oil, and obstacles.
c)
Make sure that the turret is not at the travel end in the x axis direction.
9. After Turning On the Power
a)
Listen to the sound of the hydraulic unit when it is operating.
b)
Make sure that the cooling fan in the electrical cabinet is operating.
c)
Make sure that the switches and indicators on the operation panel
operate correctly.
d)
Check the screen display: no alarm should be indicated.
Summary of Contents for ATL 1820E
Page 5: ...1 SAFETY INSTRUCTIONS ...
Page 22: ...Page 1 17 ...
Page 24: ...2 MACHINE SPECIFICATIONS ...
Page 25: ...Page 2 1 2 MACHINE SPECIFICATIONS 2 1 Dimensional drawing ...
Page 27: ...Page 2 3 2 1 2 Chip Conveyor ...
Page 31: ...3 INSTALLATION ...
Page 34: ...3 1 2 Layout floor plan Following is a top view drawing ...
Page 43: ...4 MAINTENANCE ...
Page 55: ...5 CHUCK ...
Page 64: ...Page 7 3 7 1 HEADSTOCK 1 HEADSTOCK _ 18 SPINDLE BORE 58mm 2 ...
Page 65: ...Page 7 4 18 SPINDLE BORE 58mm 2 ...
Page 69: ...Page 7 8 7 2 BED Z AXIS TRANSMISSION ...
Page 71: ...Page 7 10 7 3 CARRIAGE CROSS SLIDE ...
Page 74: ...Page 7 13 7 4 TAILSTOCK MANUAL TAILSTOCK _ 18 ...