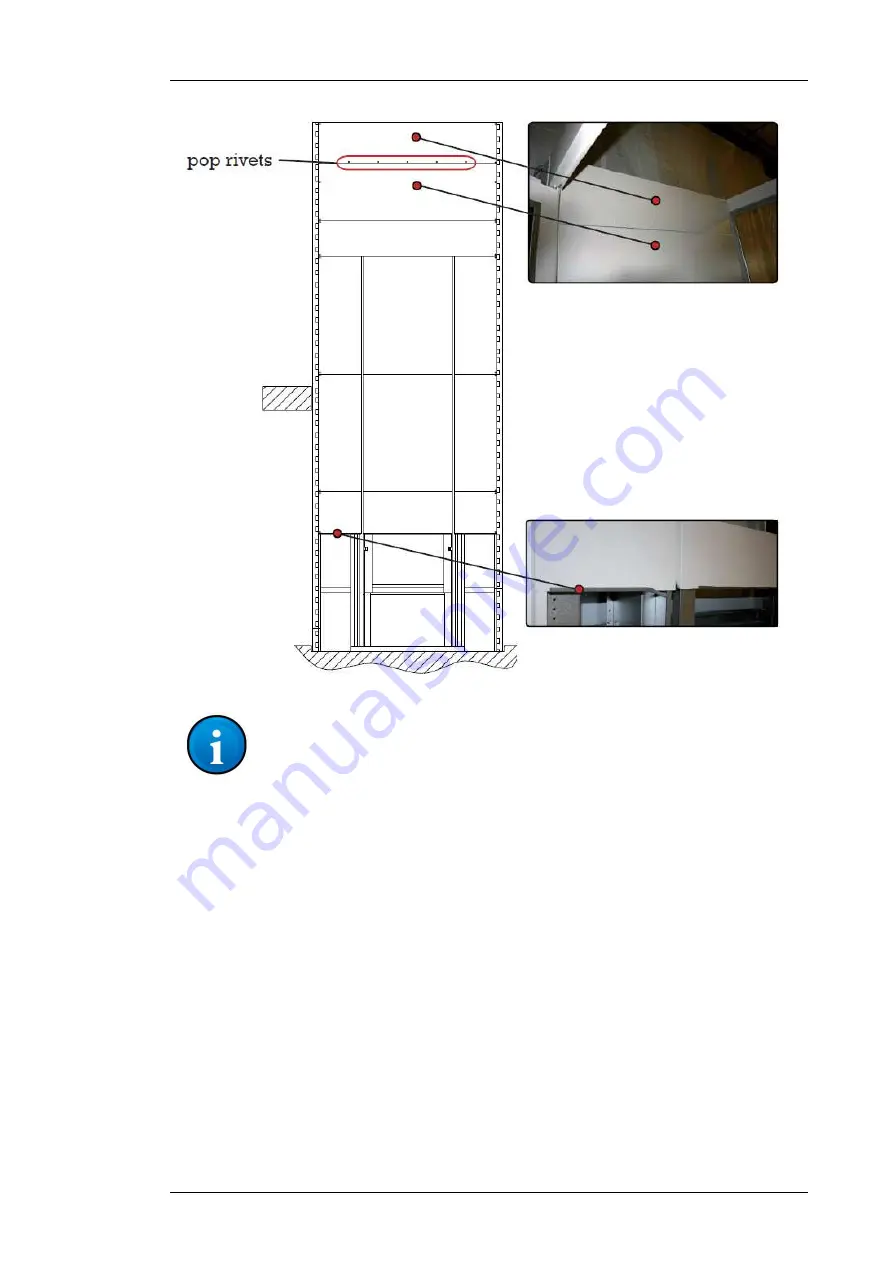
Fig. 77 Assembling the top cladding panels
Note:
For easier opening of the top/inspection panel, leave a 2 mm gap between the
top panel/inspection panel and top cladding panel.
• Use pop rivets 3.2x10 (delivered with the lift) for fixation between the full and half height top clad-
ding panels (see, Fig. 77
Assembling the top cladding panels
).
• Fasten the clip list for protection against sharp edges at the end of the cut middle and side cladding
panels (see, Fig. 77
Assembling the top cladding panels
5.10 DOOR ADJUSTMENTS AND COVER PANELS FITTING
5.10.1
COVER PLATES
• Assemble cover plates between door thresholds and filled shaft panels. Use pop rivets 3.2x10 (deliv-
ered with the lift).
7000 100 en-GB AD
85
Summary of Contents for 7000
Page 1: ...Vector Installation Manual HQ ...
Page 23: ...ASSEMBLY 5 ASSEMBLY 5 1 FIXINGS 7000 100 en GB AD 19 ...
Page 25: ...ASSEMBLY Fig 15 Mast preparation before installation 7000 100 en GB AD 21 ...
Page 27: ...ASSEMBLY Lift the top section 7000 100 en GB AD 23 ...
Page 33: ...ASSEMBLY 7000 100 en GB AD 29 ...
Page 34: ...ASSEMBLY 30 7000 100 en GB AD ...
Page 42: ...ASSEMBLY The mast shall stand upright the tolerance is Max 2 mm m 38 7000 100 en GB AD ...
Page 70: ...ASSEMBLY Fig 59 Mounting of Filled wall panels 66 7000 100 en GB AD ...
Page 72: ...ASSEMBLY Fig 61 Principal drawing Shaft corners 68 7000 100 en GB AD ...
Page 100: ...This page is intentionally left blank 96 7000 100 en GB AD ...
Page 117: ...OPTIONS Fig 126 Electrical connections external door opener 7000 100 en GB AD 113 ...
Page 140: ...This page is intentionally left blank 136 7000 100 en GB AD ...
Page 142: ...This page is intentionally left blank 138 7000 100 en GB AD ...