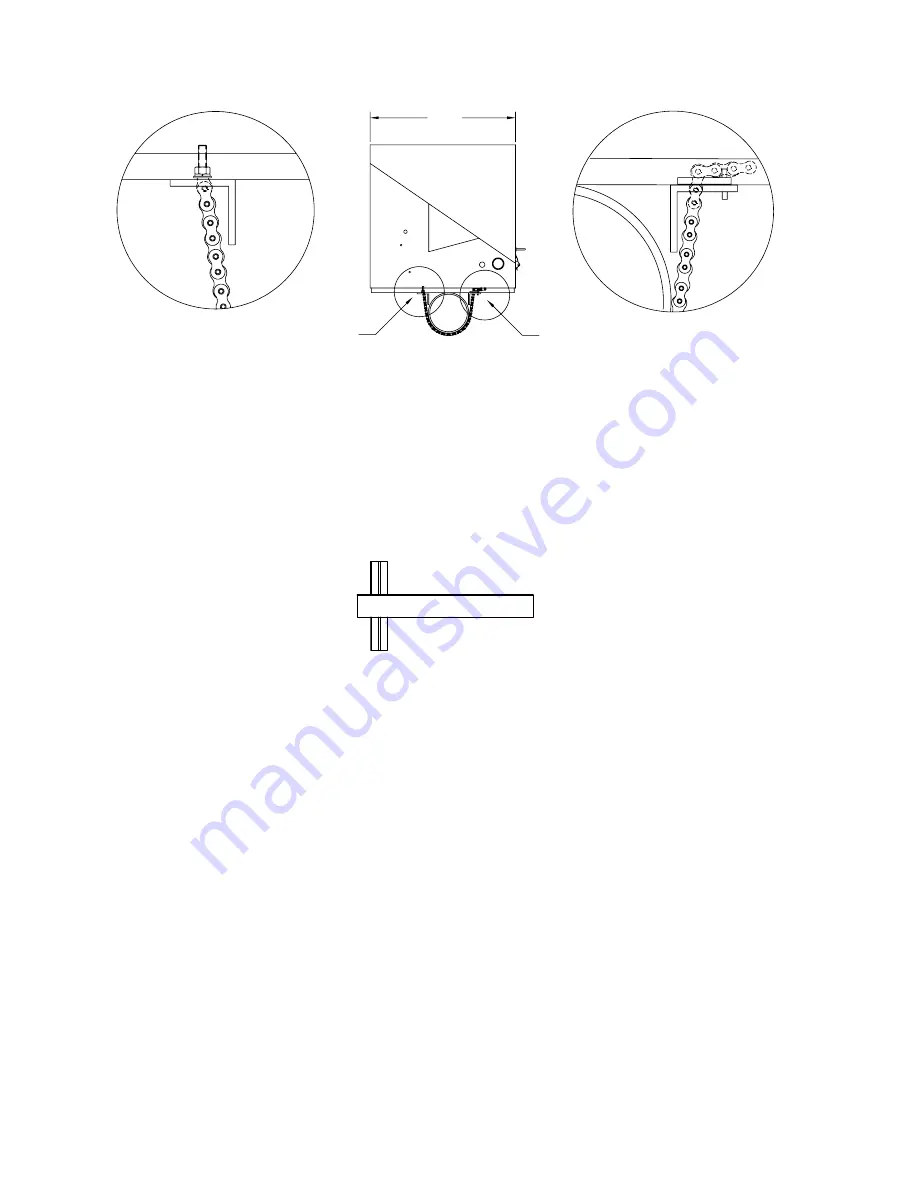
8
(31.00)
VIEW A-A
VIEW B-B
VIEW B
VIEW A
Figure 10 Pipe Mount installation
14)
Feed long flat end of Chain Retainer (see Figure 11) through middle of a
chain link then move retainer lock into position where round peg fits into small
round mounting hole.
15)
Adjust enclosure into final position on the pipe and tighten Nut on All-Thread
(adjustment assembly) until unit is securely in place.
16)
Adjust enclosure position on angle iron if necessary then tighten Bolts until
secure.
Figure 11 Chain Retainer Lock
V.
Optional Support Leg Kit Installation
If your installation includes a Pipe Mounted Cold Weather Enclosure and requires an
Optional Support Leg or two, follow these instructions, otherwise continue to the next
applicable set of instructions.
A. Materials
•
2 ea. ½-13 x 1 ¼ SST Bolt
•
2 ea. ½ SST Flat Washer
•
2 ea. ½” SST Split Washer
•
1 ea. Pre-assembled adjustable height Support Leg
NOTE:
Must use with Pipe Mounting Kit