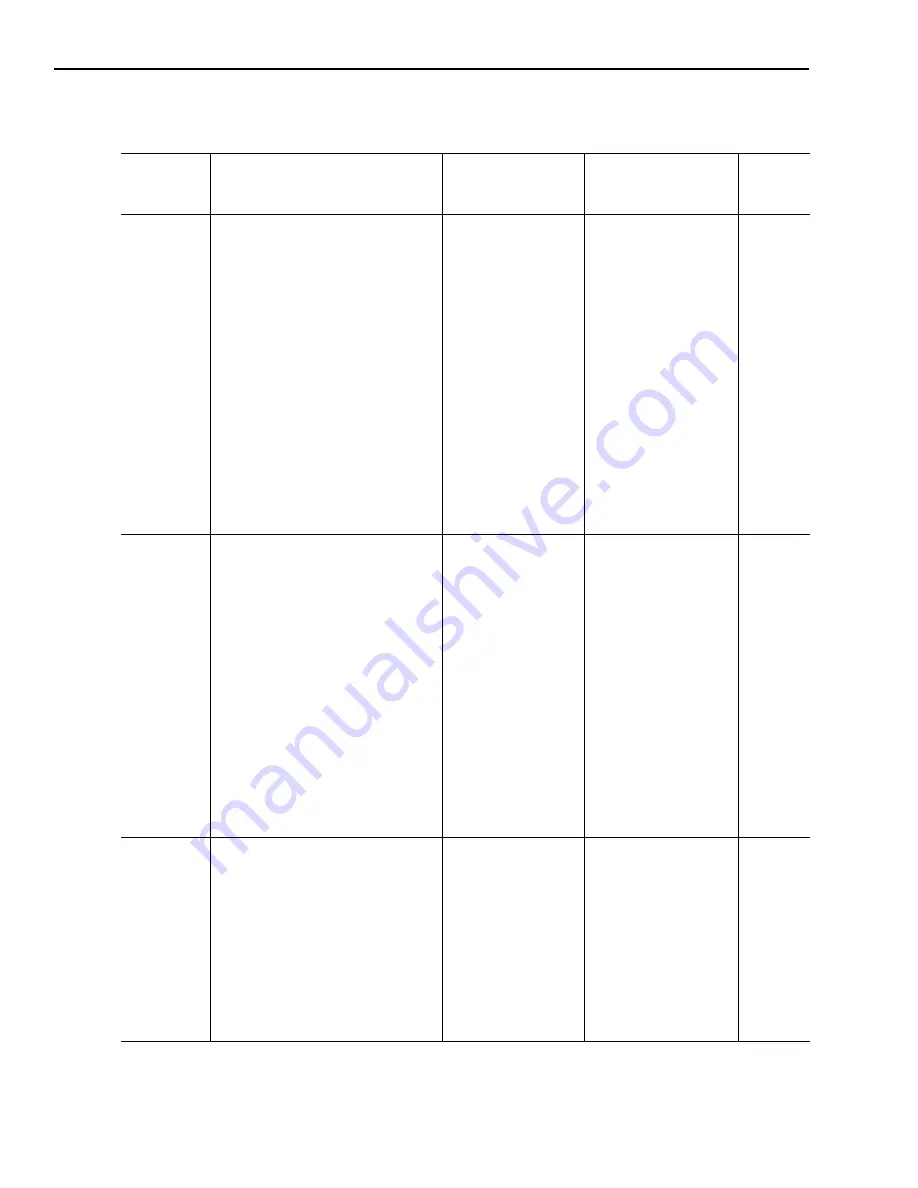
Publication 1394-5.0 — May 2000
4-6
Wiring 1394 GMC and GMC Turbo Systems
Wire:
Description:
Terminal connections for
1394
x-SJTxx-C, -C-RL
and -T, -T-RL systems:
Terminal connections for
1394C-SJT
xx-L and
-L-RL systems:
Mandatory
or Optional:
REG 5V, 24V,
COM
High-speed, optically-isolated filtered
registration input for each axis. Inputs can
be either 5 or 24V DC. Refer to Figure 4.5 for
typical registration device inputs.
Note: To further reduce electrical noise, a
dedicated power supply may be required for
the registration sensors.
You can disable the registration input filters
by removing jumpers P0-P3 on the input
wiring board.
For 5V
TB1 16 (axis 0)
TB2 16 (axis 1)
TB1 20 (axis 2)
TB2 20 (axis 3)
For 24V
TB1 17 - 18 (axis 0)
TB2 17 - 18 (axis 1)
TB1 21 - 22 (axis 2)
TB2 21 - 22 (axis 3)
For COM
(used with 5V and 24V)
TB1-18 (axis 0)
TB2-18 (axis 1)
TB1-22 (axis 2)
TB2-22 (axis 3)
For 5V
TB1 16 (axis 0)
TB2 16 (axis 1)
For 24V
TB1 17 - 18 (axis 0)
TB2 17 - 18 (axis 1)
For COM
(used with 5V and 24V)
TB1-18 (axis 0)
TB2-18 (axis 1)
Optional
A TEST 1
A TEST 2
A TEST COM
Two software-programmable outputs are
available:
•
A voltage corresponding to the motor
velocity and direction of rotation will be
present between these terminals.
±
1.0V/
krpm is available. Minimum impedance that
can be placed across this output is 10k ohm.
•
A voltage corresponding to positive and
negative current will be present between
these terminals.
±
2.5V DC equals 100% of
motor continuous current rating.
±
5.0V DC
equals 200%. Minimum impedance that can
be placed across this output is 10k ohms.
Any axis analog current/voltage output may
be linked to either analog output using
internal software parameters. By default
Axis 0 velocity is linked to A TEST 0 and
Axis 0 current is linked to A TEST 1.
TB1-24 (A TEST 0)
TB1-25 (A TEST 1)
TB1-26 (A TEST COM)
TB1-24 (A TEST 0)
TB1-25 (A TEST 1)
TB1-26 (A TEST COM)
Optional
DRIVE OK 1/2
When you apply 24V AC/DC control power
to the system and no system faults are
detected, the Drive OK relay contact closes.
The contact remains closed until a drive fault
occurs, the DC bus voltage is lost, or you
remove 360/480V input power from the
system module. If a drive fault is detected or
the DC bus voltage is lost, the relay contact
opens. You can wire the Drive OK contacts
into the Estop string to open the main power
contactor if a fault occurs. The contact rating
is 115V AC or 24V DC, 1A.
TB2 terminals 24 and 25
TB2 terminals 24 and 25
Mandatory
Summary of Contents for Allen-Bradley 1394
Page 1: ...User Manual 1394 Digital AC Multi Axis Motion Control System Catalog No 1394 50 Allen Bradley...
Page 10: ...Publication 1394 5 0 May 2000 viii Table of Contents...
Page 118: ...Publication 1394 5 0 May 2000 5 8 Wiring Your 1394 Analog Servo System...
Page 124: ...Publication 1394 5 0 May 2000 6 6 Commissioning 1394 GMC and GMC Turbo Systems...
Page 166: ...Publication 1394 5 0 May 2000 8 30 Configuring Your 1394 Analog Servo System...
Page 232: ...Publication 1394 5 0 May 2000 A 34 Specifications...
Page 292: ...Publication 1394 5 0 May 2000 D 14 Catalog Numbers...